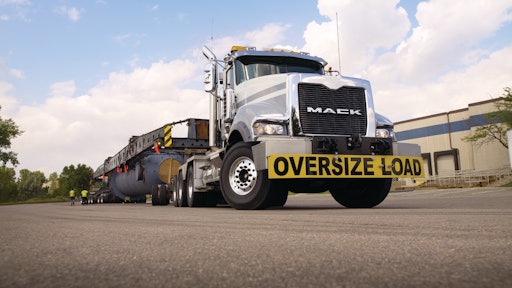
Not that many years ago, it was common to spec your preferred brand of engine with your preferred brand of transmission and axles. One truck model could offer three different engine makes and a couple of different transmission choices.
While you can still order a truck this way, there has been a definite move toward total vehicle integration where the manufacturer offers a proprietary engine, transmission or axle package. The theoretical benefit is a truck optimized for performance and efficiency, with components perfectly matched and seamless communication between the engine, transmission and various truck functions.
“Vertical integration... was a good decision years ago, but with the current cost of diesel fuel at $4 per gallon, it’s a great idea today,” says David McKenna, director of powertrain sales, Mack Trucks. “Mack Trucks has been vertically integrated from nearly day one.
“The immediate benefit is the capital cost of the vehicle,” he continues. Providing three or four different engine manufacturer choices for each chassis model could drive up the cost. “A significant amount of that cost would be directly attributable to EPA HDDE emission compliance for each engine offered, not to mention the complex installation and cooling ‘opportunities.’”
But there are performance benefits, as well. “The real benefit is the lower day-to-day cost of operating the vehicle — whether that is in the fuel efficiency area or as a chassis maintenance expense,” says McKenna.
Delivering a Unique Pedigree
Designing an integrated vehicle requires expertise. “Vertical integration can also be risky,” notes McKenna. “A great chassis, an engine, a competitive transmission and drive axle package are not enough to make the grade or close the sale in today’s marketplace. You have to excel in all areas. If not, you lose the whole deal. Customers have a lot of choices today, so we have to offer significant product differentiators and an understandable and accepted value proposition.”
Mack Trucks offers a Pedigree Powertrain that consists of a Mack engine, transmission and axles. “We offer customers a choice of three engine displacements: the 11-liter MP7, the 13-liter MP8 and the 16-liter MP10,” McKenna points out. “Within the MP7 and MP8 family, we offer three distinct engine performance profiles with four horsepower ratings in each. We also have the Super Econodyne MP8 engine. With all of these options available, there is not much of the market that we cannot commercially address.”
He adds, “To back up these engines, we offer Mack T300 series manual transmissions from six to 18 speed, and the Mack mDrive, which is a 12-speed automated manual transmission. To get the power to the wheel ends, we offer drive axles from 21,000 to 65,000 lbs. with leaf spring, walking beam and air ride suspensions.”
McKenna cites three main areas of benefit to the customer in selecting a Pedigree Powertrain:
- Hardware: Various mechanical devices still have to work efficiently together. For example, the right horsepower with the correct engine profile must be mated to the optimal transmission connected to the proper drive axle arrangement.
- Software: Communication and control are two key items to manage vehicle performance. Each applicable powertrain module must communicate with the other in a timely manner (milliseconds) and communicate in a language that is completely understood. Also, the amount of information exchange must be 100% all of the time, so that the engine knows exactly what the transmission is doing (and sometimes what it may do). This can improve vehicle performance while simultaneously lowering fuel consumption.
- Uptime: If the truck is in the shop for unplanned downtime, this adds nothing to the customer’s bottom line or their credibility with their customers.
The benefits to vertical integration vary according to the application. Fuel-conscious on-highway users will witness the greatest return. For example, the Mack Super Econodyne MP8-445SE engine/mDrive/C120 drive axle combination offers an engine that is comfortable cruising at 1,150 rpm at highway road speed. This reduces noise, vibration and fuel consumption. “But it is not as simple as clipping 300 to 400 rpm off the typical cruise speed,” says McKenna. “This involves matching the SE engine to the 12-speed mDrive, allowing the engine to remain at ultra-low rpms for highway cruise speeds, while shifting to 11th gear to maintain a higher road speed when operating on rolling hills, and still be well below typical engine rpms.
“There are certain occasions when the mDrive may actually take over full authority from the engine to maintain optimal performance,” he adds. “This simply cannot occur with different make powertrains.”
Integration Allows New Solutions
The integration of components allows truck manufacturers to pursue concepts that would not otherwise be possible.
“Volvo’s integrated powertrain allowed the company to introduce our XE exceptional fuel efficiency concept, which improves fuel efficiency by reducing engine rpm at a given road speed — a concept Volvo calls ‘downspeeding,’” says Chris Stadler, product manager, Volvo Trucks. “Fuel efficiency improves by about 1.5% for every 100 rpm of downspeeding. So customers spec’ing the XE package can expect up to a 3% improvement when compared to another overdrive transmission in a similar operation.”
To accomplish these breakthroughs, the components must be designed to work together. “The technology that enables the Volvo engine and transmission to act as one is the outstanding communication we achieve with a proprietary interface,” Stadler explains. “This allows us to give the transmission authority over the engine in some instances, and allows the design to be optimized to a higher level of performance.”
A properly optimized engine and transmission can deliver better fuel economy, better performance and longer driveline component life. This is why Volvo Trucks developed the I-Shift automated manual transmission paired with its proprietary engines. Volvo Trucks will now offer its 12-speed, two-pedal, I-Shift automated manual transmission as standard on all Volvo-powered trucks, including the vocational VHD and VNX heavy-haul tractor.
“I-Shift gives outstanding vehicle performance in challenging off-highway situations and has a number of specialized features to enhance performance in difficult situations,” says Stadler. “These include Power Launch, Rock-Free, Downhill Control, Greatest Possible Downshift and Avoid Shifts.”
In 2012, nearly one in two Volvo Trucks built in North America featured an I-Shift transmission. By using microprocessor technology, integrated sensors continuously monitor changes in road grade, vehicle speed, torque demand, weight and air resistances to place the truck in the right gear per the conditions with smooth and optimum shifts. This operation extends clutch life and service intervals. I-Shift reduces wasted revs and boosts fuel efficiency. It also helps improve driver safety by reducing fatigue and allowing drivers to give their full attention to operating the vehicle.
The I-Shift is a truly interactive product that shifts based on several variables. “We are sometimes asked, what are the shift points of the I-Shift? The I-Shift is not like that popular imported car that simply has a I on the speedometer’s 15-mph mark, a II at the 30 and a III at the 45,” Stadler comments. “The I-Shift knows exactly the performance of the Volvo engine mated to it, and will select shift points based on the whole realm of dynamic inputs.”
An integrated electrical system ties everything together. “The communication between the engine and transmission is important and the electrical integration is a key to successful performance of the engine,” says Stadler. “Volvo engineers develop an electrical platform that closely interacts with all the components within the vehicle. They use that platform to ensure these electronics are communicating the correct information to the transmission so that it can place the engine in the correct gear based on the current road conditions.”
Integration Ties All Systems Together
Daimler Trucks has also made great strides in vehicle integration that have led to performance gains. This includes a proprietary line of Detroit engines and axles.
“Detroit components account for the majority of components spec’d in Freightliner and Western Star products. There are many advantages of a completely integrated powertrain to customers,” says Brad Williamson, manager, engine and component marketing, Daimler Trucks North America. “Detroit and Freightliner (and Western Star) engineers collaborate on projects to make sure every design works together and is optimized for fuel economy, performance, reliability and durability.”
An example is the integration of the Detroit DD15 engine with the DT12 automated mechanical transmission. “The DT12 transmission and DD15 engine integrate and leverage shift schedules only achievable by both components being offered by one manufacturer,” Williamson indicates. The Freightliner Cascadia Evolution equipped with the new DD15 engine, DT12 transmission and Detroit axles provides up to 7% better fuel economy than the previous Freightliner Cascadia powered by the Detroit DD15 engine.
“Another benefit of an integrated powertrain design is to be more cost efficient when emission and regulatory changes occur,” he continues. “These changes often require thousands of man hours to design, test, validate, optimize and integrate various components to deliver products that meet the customers’ needs. So instead of repeating this process with multiple brands of components, our integrated design makes the process less challenging and ultimately more efficient.”
Integration can also reduce downtime. “The Detroit integrated powertrain is monitored by Virtual Technician. [This is] Detroit’s proprietary onboard diagnostic system that monitors and communicates directly with truck owners on all potential and real issues,” says Williamson.
One stunning example of where integrated design is headed can be seen in the on-highway market with Daimler Trucks’ Predictive Powertrain Control. The truck’s cruise control system can see the topography of the road ahead. The powertrain then responds in the most fuel-efficient manner. While this technology sounds like science fiction, it is already in use.
Freightliner is currently using Predictive Cruise. Unlike a cruise control system that tries to maintain a given engine speed regardless of the terrain ahead, the Predictive Cruise uses GPS to look at the terrain up to a mile ahead. The system adjusts the actual speed of the truck for maximum fuel efficiency based on the terrain, while staying within 6% of the set speed.
Daimler Trucks North America worked with NAVTEQ, a provider of digital map data for location-based solutions and vehicle navigation. Using advanced digital map slope data from NAVTEQ, RunSmart Predictive Cruise combines high-precision GPS road coordinates with road grade data of more than 200,000 miles of the most widely used truck routes in the continental United States.