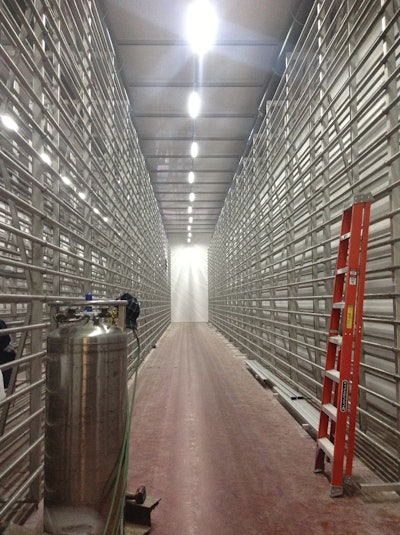
Since 1991, The Face Companies has been recognizing the flattest and most level concrete floors with its Golden Trowel awards. The company named seven Gold Plate and four Silver Plate winners in the 2012 competition, three of them world records. Entries from three countries — the United States, Canada and Australia — were among this year’s acknowledged contractors.
Floor levelness and flatness measurements used to determine winners in the competition are based on the F-Number system, first introduced to the concrete industry by The Face Companies in 1982 and adopted by the American Concrete Institute (ACI) in 1990 (ACI 117). Following are descriptions of two winning projects. See the sidebar on Page 32 for all the 2012 Gold Plate winners.
Emmi Roth Cheese Factory
Smykal Construction took home a 2012 Golden Trowel Award for its floor at the Emmi Roth cheese factory in Platteville, Wis. It was Smykal Construction’s first superflat placement, narrowly missing a world record in the Narrow Strip category with its FF 171/FL 95 on the 19,500 square foot job. Smykal Construction enlisted the help of consultant Eric Palmquist of Precision Concrete Floors, LLC, in Oshkosh, Wis., for the superflat portion of project.
Emmi Roth is an international cheese and dairy products company. Smykal Construction had the full concrete package at the new cheese factory, supplying an 80,000-square-foot foundation for the steel building along with thick foundation bases and walls for the milk silos. The cheese factory required a superflat floor in the room where the cheese ages. That’s because the aging process is aided by a robot that runs up and down the narrow aisles picking up cheese wheels, flipping them and returning them to the rack.
The 9-inch-thick superflat floor in the climate-controlled room included #5 rebar placed 1 foot on center. The slab sat on a 3-inch mud slab with 4 inches of foam and a 45-mil vapor barrier. The placement was done in 16-foot-wide strips, 130 feet long.
Shane Smykal, VP and partner at Smykal Construction, explains the superflat process demands more precision and time than your typical flatwork placement. “Formwork is the key to getting high FL numbers,” he says. “The formwork has to be dead on.”
Smykal adds that achieving high FF numbers is all in your placing and finishing technique, which requires a lot of handwork. The finishing crew on the Emmi Roth project truss screeded, hand struck with a saw beam, bump cut, panned with riders, then hard steel troweled the floor. “Everyone on your finishing team has one or two jobs to focus on, and if one person isn’t doing his job properly it can throw things off,” Smykal adds. “It is critical that everyone works together as a team.”
Smykal also credits his ready mix supplier, Bard Material. “They did an outstanding job with service and consistency, which is crucial in any slab placement,” he says.
Adding to the challenge of the project, the floor was designed jointless to reduce the chance of curling. The engineer specified a wet cure to reduce the chance of cracking. Smykal says despite his skepticism, there isn’t a crack anywhere on the floor.
Rigby’s Family Entertainment Complex
The roller skating rink floors at Rigby’s Family Entertainment Complex in Warner Robbins, Ga., garnered one of the two world records Birdwell & Associates and Skene Concrete collected in the 2012 Golden Trowel Awards. Bryan Birdwell of Birdwell & Associates says everything aligned for this project to result in a world record, including the owner essentially turning the job design over to his company, allowing them to plan the mix design, subgrade prep, and concrete place and finish.
Birdwell & Associates utilized its proprietary floor system, F.A.S.T. Floor, on this project. F.A.S.T Floor is a jointless, shrinkage- and curl-compensating concrete slab design that uses high doses of macro fiber as the reinforcing agent. Birdwell says the Rigby floor has no curling, and Dipstick measurements taken periodically in the floor’s first year show elevations consistent with the original placement.
Birdwell explains how the high-dose macro fiber contributes to a floor’s flatness and levelness results. “In my opinion, one thing the macro fibers assist with is in holding the concrete in place, reducing the differential surface shrinkage. So if you strike off at the right elevation, the concrete will stay at that elevation,” he says.
Precision in fine grading, form set-up, and place and finish operations are all instrumental in achieving high F-Numbers. The crews from Birdwell & Associates and Skene Concrete took special steps to precisely set form grade. “Everything starts with the accuracy of grade and the accuracy of the formwork,” Birdwell says. “We made sure all the forming done on the Rigby project was within 132 of an inch. It was probably the best forming job we have ever been a part of.”
Birdwell also explains that when he is on a project with high F-Number specifications, special care is taken to make sure the laser-guided screed is properly calibrated and operated. “We find that any tool or piece of equipment can be set up and operated with varying degrees of accuracy — even something as inherently accurate as a laser-guided screed. So the more you fine tune what you’re doing and how you do it, the higher level of results you get,” he says.
Through years of systematically testing various finishing scenarios, Birdwell has identified several best practices that maximize results on his company’s floors, including slab and mix design, screed set-up, placement speed, and finishing techniques. “Quality concrete floors are a process, not a product. This slab demonstrates that perfectly,” Birdwell says.
The result was a world record floor that measured FF 123/FL 123, both the highest FL numbers and highest combined F-Numbers ever for this type of project. Birdwell & Associates holds 23 Golden Trowel awards, the second highest number of awards won over the history of the competition. The company also currently holds three world records in the competition.
Birdwell & Associates will return to the Rigby project to polish the floors, adding additional benefits to the owner. “A polished finish will prevent the rink owners from having to reapply a $10,000 to $15,000 epoxy coating every year,” Birdwell explains.
Center for New Media
First-time entrants Messerly Concrete took home two 2012 Golden Trowel Awards, including a Gold Plate award for its work at the Center for New Media on the campus of Salt Lake Community College. The 6,639-square-foot film studio floor was specified at FF 100/FL 50; Messerly Concrete achieved an FF 114/FL 79 on the project.
The Messerly Concrete crew placed the monolithic, jointless slab with a 1.5-pound traprock mix, which Todd Messerly says offers a durable wear surface with a long service life. The crew reinforced the slab with #5 rebar, 16 inches on center. The mix included a shrinkage compensating additive, which Messerly explains causes the mix to expand rather than contract for the first 10 days after placement. After 10 days, the concrete has gained enough strength so when it relaxes it doesn’t crack.
Messerly says the entire construction process for a floor like this requires a high level of attention to detail. “There is a lot of prep and care necessary on the edge forms to ensure they are at the precise elevation. We use a laser to set initial grade, then go back with a builder’s level to make sure they are dead on,” he explains.
In the placement and finishing process, Messerly Concrete crews took numerous passes with the Laser Screed at different angles, then used bump cutters and check rods to cut off any excess material. The troweling process, Messerly adds, is an important step and requires continued attention to detail to ensure flatness.