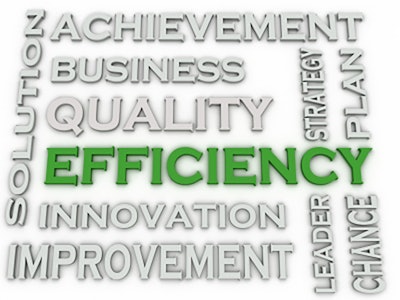
Answer the following questions that I posed to contractors at an international meeting for construction owners and leaders. (Might make a great discussion topic with your leadership team.)
- Is every project fully “flushed out” with a written plan?
- Do crew leaders thoroughly consider crew member roles and responsibilities before the job starts?
- Does every project have a clear tracking system for field leaders and their crews to benchmark and review?
- Are crews knowledgeable about each other, and do they recognize each member’s strengths?
- Is every job estimate validated/confirmed and then clearly set out as a project budget?
- Does every project have periodic “job reviews” to specifically capture best lessons learned?
- Do crews and “hot-trucks” take longer than they should when going from Point A to Point B?
- How much “extra” inventory do we have due to poor inventory management?
- Do we know what our “wastes” in job preparation, execution and completion are?
- Are we working to eliminate such “wastes,” and are we effective at preventing the return of such “wastes”?
Answers to these 10 questions can be quite revealing about the efficiency and effectiveness of your company. Honestly addressed, you will most likely find that there is undoubtedly room to improve. Answering the questions leads us to consider what we can do to make our construction efforts more productive, profitable and just plain smarter!
The economy has perhaps had the biggest impact on getting most contractors to think “lean.” For many, this has resulted in layoffs, budget reductions for services from office cleaning to advertising, and extending the life of company vehicles for owners and leaders. In short, most of us have tried everything we can think of to stretch our “falling” dollar as far as we can.
The term lean construction, however, moves past our efforts to only run our companies as tight and smart as possible. Lean construction is actually a proactive strategy of reducing many of the contributors to poor performance.
The strategies associated with lean construction may very well lead a contractor to reduce expenditures on purchasing new equipment, but the strategies are more directed at reducing every hurdle that prevents crews from producing great work the first time.
At its heart, lean construction is about identifying and eliminating waste in the entire construction process. From sales and marketing efforts to estimating, from “pre-con” to our closeout procedures, lean construction is designed to strengthen our every work process. Lean construction isn’t about doing things with as few workers or as little material as possible but instead with exactly what is needed to perform A+ work the first time, every time!
To better understand lean construction it is important that you understand the “seven wastes.” I’ll present the seven wastes below and then expand on them over future articles. It is important that you and your leaders learn how each waste can hurt your construction process and prevent you from realizing effective and profitable results.
Lean construction: the seven wastes
- Overproduction
- Waiting
- Motion
- Transport
- Over-processing
- Inventory
- Defects
AND a bonus waste…people utilization
Briefly, the seven wastes are based on the early works of quality gurus such as Dr. Ed Deming, known as the “Godfather of Quality.” Dr. Joseph Joran, Dr. Deming’s contemporary (and industry nemesis) also greatly contributed to the overall quality movement dating back to the late 1940s. Companies such as Toyota, Honda, Allied-Signal, Ford and Motorola are just a few of the giants of industry that conducted world-renowned research and testing that furthered the understanding of eliminating wastes to improve quality and lower costs.
I share this brief history of “lean” with you because it is critical that construction companies of all sizes and specialties understand that getting better is possible…very possible. As bidding work has become more competitive than ever, embracing and integrating lean construction will strengthen your grip on your own work processes and help to reduce surprises and setbacks to your construction efforts.
For a moment, reflect on something that I wrote about in another article about the construction “disease” I call “looking for stuff.” It is estimated that construction workers can spend between 60 to 90 minutes per workday looking for tools, equipment, materials, their boss, etc. If you use a conservative 60 minutes per day and multiply that by the number of workers on your crews you will soon see why this “disease” is not so funny.
Calculate the number of total man-hours lost per week for your entire construction season and then multiply that time amount by your average fully burdened hourly rate and you begin to see why I am so focused on helping contractors get their companies and crews better organized. For most contractors, “looking for stuff” is simply costing thousands of dollars, further reducing the profitability that should be made!
Lean construction isn’t another gimmick to cut costs. It’s a way of constructing that engages people to think first, think smart and think with respect to others. If you will begin to think, talk and act “lean” you will begin to see your company achieve new heights of success and effectiveness!
We'll take a close look at each of the seven wastes individually in separate articles. I’ll tell you how and why each waste occurs, and I’ll provide specific, contractor-tested practices you can implement to reduce each specific Waste.
Until then… Stay Lean!