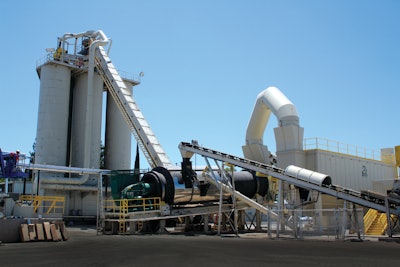
Building a new asphalt plant in California requires the use of state-of-the-art technology to meet strict environmental compliance standards and the task of satisfying an array of agencies with overlapping jurisdictions.
This was the challenge that Vulcan Materials Company faced when building their new Fresno plant. Over 12 years ago, Vulcan made the decision to close their hot mix asphalt (HMA) operation on West Ashlan Avenue and supply HMA only out of their Friant Road operation in Fresno. When the decision was then made to close the Friant plant, Vulcan began the process of reopening Ashlan HMA.
Originally the site included an asphalt plant and a small train kids could ride on. Although the train is gone, some of the original building still remain. Despite having an asphalt plant on the property previously, agencies, including the air district, required that a new plant be built to meet the stricter environmental standards of today.
Higher standards, new technology
So what did this mean for Vulcan? They were charged with installing an asphalt plant which can meet today's varied material demands from customers and satisfy the demands of agencies and neighbors alike.
The plant site is in the San Joaquin Valley Air Pollution Control District air district which has one of the toughest NOx burner requirements in the state. San Joaquin Rule 4309 requires facilities to test and meet NOx of 4.3 PPMV at 19% O2 (this is equivalent to 40 at 3% O2) and CO of 42 PPMV at 19% O2.
To meet this challenge, Vulcan rebuilt with an Astec double barrel drum mix plant and a Butler-Justice Blue Smoke Control unit. The plant incorporates the latest in asphalt drums, low-NOx burner emissions, blue smoke control, advanced plant controls, warm mix capabilities and the abilities to use recycled asphalt pavement (RAP), if desired.
The asphalt dryer utilizes an Ultra Low NOx Phoenix Phantom burner manufactured by Astec. The burner achieves its emission reduction through a lean burn premix design. By carefully controlling the mixing of air and fuel, the burner can achieve the low NOx emissions.
Vulcan had to use a burner that could be relied upon to stand up to the demands of a high-volume plant with strict compliance standards. The site will be required to demonstrate compliance with this standard into the future with source testing. Rule 4309 also requires monthly compliance test demonstrations with a hand-held analyzer plus an additional compliance source test every two years.
How it works
The plant operates with four 32,000 gallon CEI vertical asphalt tanks. These tanks are required to meet emission standards for burner emission control, vent control, and spill control. The tanks use an Ultra Low NOx burner fired on natural gas to keep emissions as low as possible. Six inches of insulation is used on each tank to minimize hear loss which helps reduce demand on the burner. The exterior piping on each heating unit is also insulated. A mist eliminator vents each tank to control emissions that result from heating the oil and loading of the tank. Spill control for the tanks includes the use of secondary containment and released hoses.
For product storage, the plant includes five 300-ton silos. These silos are completely enclosed which prevents emissions from escaping. The sealed silos also help to maintain the temperature of the materials which helps increase efficiency.
The silos also use a multi-stage blue smoke control unit to capture fugitive emissions that occur as the silos are being loaded from the top and as mix is transferred from the silos to the trucks. The truck load-out area is also controlled by a tunnel that encapsulates and traps blue smoke emissions as the hot asphalt is dropped into the waiting trucks.
These emissions contain primarily oil droplets which are trapped in the filter media. Residual oil collects in the bottom of the unit and can be recycled back into the process. The blue smoke control unit achieves its collection efficiency using six stages of filters that control the progressively finer particulate. This reduces visible emissions and controls odors that are sometimes associated with older plants.
Prepared for growth
The plant also is equipped with Astec's WMA System. This allows asphalt plants to provide material at reduced temperatures while still meeting the demanding performance specifications needed in California.
While there are many benefits to WMA technology, including reduced fuel consumption and fewer emissions, the universal acceptance of WMA on many jobs is a long way off. Astec's technology allows a facility to produce traditional mix and WMA from the same equipment. The system injects air and water through nozzles into the asphalt which allows it to foam. The foamed oil has a reduced viscosity and allows the oil to coat the aggregate which makes the final product workable at lower temperatures.
Once the asphalt is placed, it looks and functions similar to traditional asphalt mixes. As acceptance of WMA continues to increase, the ability of this plant to produce the materials will allow this facility to produce asphalt and reduce emissions.
The plant sits on a large piece of property which allows for adequate material storage to feed the plant. A portion of this property includes storage for aggregate and recycled asphalt. The plant is able to receive reclaimed asphalt pavement (RAP) for the plants and also to sell direct to customers.
RAP is produced from jobs where asphalt is removed during demolition or road improvements. Recycling asphalt eliminates a waste stream from the landfill and allows oil and aggregate to be reused. Once processed, the aggregate and oil is recycled and blended with new asphalt to be put back into paving projects.
Vulcan's Ashlan HMA site has been rebuilt to today's environmental requirements and demands for environmentally conscious products. Utilizing state-of-the-art technology, this equipment allows the facility to meet the requirements of today, while being prepared for the demands of tomorrow.
Portions of this article are reprinted with permission from California Asphalt magazine, the official publication of the California Asphalt Pavement Association