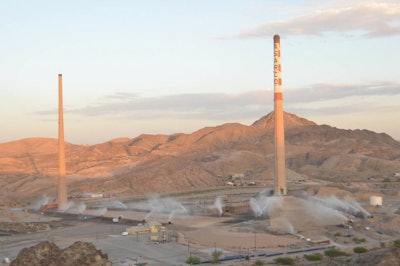
Information from this article was first published in Demolition Magazine and is being reused with permission from the National Demolition Association.
Thirty five seconds was all it took for 12,000 cubic yards of concrete and 210 miles of rebar to come crashing to the earth, an important milestone in the remediation of the historic ASARCO El Paso, Texas, copper smelter. Environmental Resources Management (ERM) performed the design oversight and execution of a multi-year demolition and asset recovery project, which culminated with the explosive demolition.
ERM, led by Global Demolition Director Robert Klotzbach and Senior Partner Jeff Bauguss, assembled a world class team that included NDA members Brandenburg Industrial Service Company and Dykon Explosive Demolition to complete the event.
The planning process for the demolition of the chimneys originally started in 2010. The first issue to be resolved was the direction of fall of the chimneys. The jobsite is centrally positioned between two major rail lines, a state highway, an interstate, a canal, a river and an international border. The chimneys were located on the extreme west side of the property, the foundations of which were located approximately 65 ft. above the highway, one of the rail lines, the American canal, the Rio Grande and the international border.
After factoring in various outcomes, the decision was made to fall the chimneys to the east, which was not without challenges. The original adobe administrative building built in 1897 and slated to be preserved is located east of the chimneys’ location.
The smaller chimney was constructed of 3,200 cubic yards of concrete and 378 tons of rebar with walls 33 inches thick at the base and about 8 inches thick at the top. It stood 612 feet tall and 46 feet in diameter. The taller chimney measured 828 feet tall and at the time of its construction it was considered the tallest chimney in world. The chimney was actually a chimney inside a chimney to manage two exhaust streams. The outer chimney had a diameter of 62 feet and was approximately 38 inches thick at the base and contained 6,250 cubic yards of concrete and 465 tons of rebar. The inner chimney had a diameter of 32 feet at the base and the walls were approximately 42 inches thick at the base.
The potential for dust generation and narrow fall zones required development and implementation of customized mitigation measures. Berms comprised of crushed concrete were built in an attempt to curtail the lateral motion of dust generated from the demolition and to protect the onsite structures from fly rock. The team decided to extend the berms around the fall zone.
The soil on the site was impacted with heavy metals, primarily lead, cadmium and arsenic, left behind by the smelting process over the last 100 plus years. The fall zone had to be designed to reduce the potential of these potentially affected site soils to become airborne during the demolition. Geotextile fabric was placed over the site soils and then covered with 12 inches of imported clean soil. Approximately 35,000 cubic yards of soil was used to prepare the fall zone. This soil was then treated with a soil tackifier to limit the dispersion of dust during the demolition event.
NDA Associate Member Company Wrench was selected to develop the misting component of the dust control system for the demolition of the chimneys. The event drew upon the company’s resources from around the country to supply the system of 24 misting machines consisting of a combination of Dust Destroyers and specially modified Dust Fighters. The system encircled the fall zone and provided a mist blanket using approximately 3,000 gallons per minute of water. Maximum effectiveness with the least amount of water use was the goal in the drought stricken area of West Texas. An extensive air monitoring network was established on site, in El Paso and in Ciudad Juarez, Mexico to monitor dust during the event and to evaluate the effectiveness of the control measures.
The chimneys were felled using explosives on the east side to cause them to fall like a tree onto the prepared fall zones. Brandenburg and Dykon prepared the chimneys by manually removing a hinge point in each to allow it to rotate to the east. They then drilled 194 holes and filled them with nearly 300 pounds of dynamite.
This past April just after sunrise, the signal was given to fire the explosives. The 612-foot chimney was first. As gravity began to take hold of the smaller chimney and drive it to its ultimate destination, the explosives were fired on the 828-foot chimney. The sequence took 35 seconds.
After the event, constituent data from the air monitoring network was evaluated and demonstrated that the dust controls were effective. The event required months of planning and the engagement of more than 30 government agencies and private companies located in the US and Mexico.
After operating for over 100 years and manufacturing zinc, lead, antimony, and copper products, the smelter closed. ERM was hired to decommission, decontaminate and demolish the facility. For nearly three years, the team salvaged and recycled materials, bringing in over $25 million for the client. The team (including subcontractors) has worked for nearly 200,000 hours on this project with no recordable or lost time injuries.