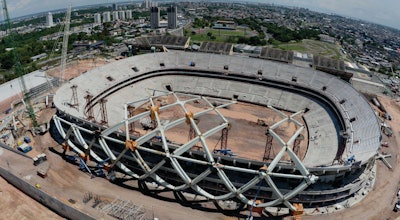
The challenge:
Constructing a stadium for the 2014 FIFA World Cup in the middle of the Amazon rainforest
The players:
GMP Architekten
Andrade Guitierrez
ENTEC
Tomiasi
Martifer S.A.
The process:
Located 932 miles from the sea, in the middle of the Amazon rainforest, Manaus is where the Rio Negro and Rio Solimões run together to form the Amazon, the world’s largest river. It is also the capital of the Brazilian state of Amazônia. Manaus, with what is said to be one of the world’s most beautiful stadiums, will be the host of four matches during the upcoming 2014 FIFA World Cup. For the construction of Manaus’s “Arena da Amazonia” stadium, three different companies - Andrade Guitierrez, ENTEC and Tomiasi, combined their expertise and Terex equipment to work on one of the world’s most innovative stadiums. They used Genie aerial working platforms and Terex tower, crawler, all terrain, rough terrain and truck cranes.
The project was designed by “GMP Architekten” a German architecture firm and the same firm that designed the Commerzbank arena in Frankfurt for the 2006 FIFA World Cup.
Energy efficient design
With a maximum capacity of 45.000 spectators, design cues symbolizing its location in the Amazon and under a banner of a sustainable world cup, the “Arena Da Amazonas stadium” in Manaus features multiple innovative design features and will be a LEED certified building. The stadium’s most striking feature is its roof, a structure made with mutually supporting cantilevers whose steel hollow core girders function simultaneously as large gutters to drain the 86 inches of rain water that fall on average during the year. To cope with the average temperature of over 86 degrees Fahrenheit and 80 percent of relative humidity in Manaus, the stadium’s roof will be covered with translucent PTFE (Teflon) membranes that reflect heat and at the same time let light through. Additionally, ventilation is provided by movable vanes within the roof structure that allow the wind to flow through or can be configured to use convection as a means of ventilation on non-windy days.
Phase one
Construction activities of the Arena Amazonas stadium started with the demolition of the Vivaldão Stadium that stood where now the new stadium is being built. During this stage, the lawn was reclaimed and stored for future use and a large percentage of the material from the old stadium was recycled for use in the construction of the new stadium.
When the old stadium was demolished, construction of the stadium’s basic structure began. For this phase, foundations and supporting structures were laid, and two Terex SK 575-32 hammerhead tower cranes were erected to lift and place precast concrete components. The cranes had heights of 196 and 170 feet and jib lengths of 177 and 193 feet respectively. The cranes have a maximum lifting capacity of 70,547 pounds and were mounted on bases on rails over 328 feet long. “These cranes had to pick and placed hundreds of precast pieces that assemble the seating tiers. We chose the SK for its robustness and lifting capacity,” said Thiago Bezerra, Construction and Equipment Engineer, Andrade Gutierrez S.A. “The setup we chose is very efficient, as we can cover a large surface with only two tower cranes, this saves costs and time when comparing erecting multiple towers.”
Assembly of the last row of the upper tier of the Arena da Amazonia was completed on May 30, 2012. With this phase complete, the focus shifted to the finishing stage of the stadium’s structure and to the construction of the facade and roofing structure. The Head of the Public Projects Management Bureau for the World Cup (UGP-COPA), Miguel Capobiango Neto, pointed out that according to the schedule, the end of the assembly of the stands was anticipated in two days. "With this step, we will concentrate on the more sensitive and complex process of the work, that's the roof/façade system," he said.
During the construction of the stadium’s basic structure, the two SK 575 tower cranes performed the majority of the lifts, but when more mobility and versatility were needed, the lifting duties were assumed by Terex AC 200-1 and AC 350/6 all terrain cranes, an RT 280 rough terrain crane and a TC 780 truck crane.
The all-terrain and truck cranes belong to the local Manaus based lifting and rental company ENTEC Longhi S.A. and were used for multiple kinds of lifting, from loading heavy steel components to placing precast components in difficult and hard to reach places. “For this kind of work, we needed cranes that could handle the variety of different lifts, such as heavy lifting and long radii lifts. The cranes also needed to move from place to place relatively quickly and be able to be set up equally fast. We chose an AC 200-1 and an AC 350/6,” said Reinaldo Longhi, operational director, Entec. “We had the cranes on site with maximum counterweight and just the main boom. The boom length and capacity of these machines without attachments are very solid, no attachment meant faster set up times for each new lifting location. These two (cranes) handled most of the lifts around the stadium. We also brought a TC 780 when we needed to step up the number of lifts within the restricted timeframe. We get a lot of rain here so we really need to be precise and efficient to keep to schedule.”
The cranes were on site for six months and carried out over 90 lifts. Some of them at 82 feet high, 78-foot radius and lifting 61,729 pounds. “Of the 11 cranes working on site, eight were Terex. I was impressed by the reliability of all of them, this provided me with peace of mind that operations and timing wouldn't be jeopardized because of equipment failure,” Gutierrez said.
During the finishing process, Genie products from the Terex Aerial Work Platforms business segment assumed a prominent role at the worksite. Andrade Gutierrez utilized Genie GS 2646 electric scissor lifts to mount fixtures and general finishing work.
Constructing the roof
The roof of this stadium is unique and provides functionality by moderating temperatures and draining immense quantities of water. The design cues were inspired by local flax basket weaving made by indigenous Amazonas inhabitants. The self-supporting roof is anchored to the stadium structures via tie bars and made from over 200 pieces of steel weighing over 14,704,834 pounds all together with the largest components 72 feet long and weighing 66,138 pounds.
With most of the routine precast assembly work behind, the construction of the roof could start. The journey of the parts that compose the roof’s structure started in Portugal, where the company Martifer S.A. produced them. The parts were shipped by boat directly to the Port of Manaus. After being unloaded, the parts were loaded to semi-trucks with the help of a Terex TFC 45 reach stacker.
The construction of the steel roof structure is by far the most complex part of the stadium. The construction was divided into 11 phases, including the erection of prefabricated structures, building and placing temporary support structures to bear the weight of the structure during construction, and the final phase, when the top pieces (compression stress) are placed. Once completed, the structure becomes self-supporting and the temporary supports can be removed.
Once the parts arrived at the jobsite, the work was coordinated almost like an assembly line. Boats arrived from Portugal periodically with the parts, the parts were unloaded and transported onsite where Terex all terrain cranes, previously used for precast lifting duties, lifted individual parts of the structure to form sub-assemblies, which in turn were lifted and placed with a Terex CC 2400-1 crawler crane belonging to Tomiasi Logistica Pesada. Finally, construction workers welded them together with the help of Genie Z 80/60 booms.
For this job, the CC 2400-1 was configured with a 275-foot main boom, SH/LH configuration and vario superlift. "We had to lift sub-assemblies weighing up to 202,825 pounds. In the beginning, we were working at 65-foot radius or less and we didn't need to use the additional superlift counterweight, but when we had to place the roof trussed well inside the stadium, the radius was much larger so we connected the vario superlift,” said Marcelo Vinhote da Silva, commercial analyst, Tomiasi Logistica Pesada.
Once the roof structure is finished and is self-supporting, the last step is to install the PTFE membrane. This is expected to occur towards the end of 2013.