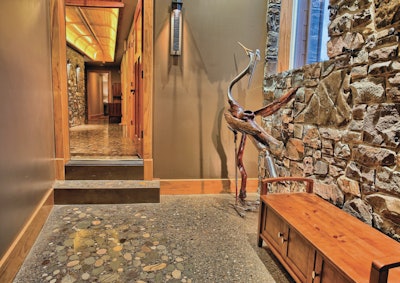
The River Lodge on the Susquehanna is a 1,940-square-foot residential home located on the Susquehanna River in central Pennsylvania. The owner, a jewelry designer by trade, was heavily involved in the floor design. She wanted to create the appearance of a dry riverbed winding throughout the main corridors of the home using hand-picked river rock, much of which she found on her property.
It was a great idea, but to say this project was a “challenge” is stating it mildly. First, the large exposed stone and 1-inch glass aggregate that made up the riverbed had to be hand placed in what would be the home’s main entrance then wind to the kitchen and living room areas before any of the interior walls were set. Second, the remote location of the home paired with a hot, sunny day left our crews little time to place and finish the concrete.
Proper planning was the key to this project. Before the concrete arrived on site, our crew measured out where the walls and doorways would be built and noted the center of the doorways and hallways with stringline. This gave workers a rough map of where they would later create the dry riverbed look with the hand-seeded river stone and glass aggregate.
Things moved quickly on placement day. Because the first floor of the house was on insulated decking, we had to pump in the special river gravel mix with an overhead pump before the roof was installed. The concrete producer was over an hour away and the weather was very hot that day. The concrete was setting up quickly, so immediately after the screeding process crew members hand placed the river rock and glass aggregate utilizing knee boards and a suspended planking system. Then they bull floated and troweled as usual.
Polishing process
The grinding and polishing process took place over two mobilizations. Our crew was able to perform the initial cut and early grinding steps on the concrete before the interior walls were built. Then we covered the floors for the duration of the interior homebuilding process. When the home was close to being finished, we came back to take the floors up to a 3,000-grit polish, adding a brown dye and densifier at the appropriate times.
All our efforts were well worth the work. The customer was very happy with her floors and the project achieved the green building designation it hoped for, becoming the first LEED Gold certified home in Dauphin County, Pa.
About the Author
James Peachy is sales/estimator for Rosebud Concrete, a full-service concrete contractor in Myerstown, Pa. Learn more about the company’s traditional and decorative concrete work at www.rosebudconcrete.com.