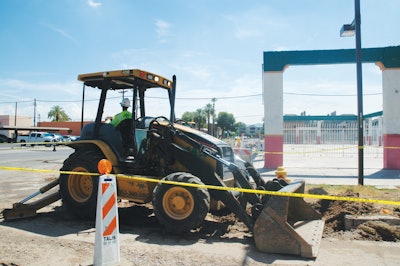
While backhoe loaders have many of the same maintenance requirements as any machine with a diesel engine, there are unique maintenance demands.
The backhoe is the working end of the machine and deserves careful attention. “The backhoe swing system is often the most highly loaded, and it’s important to keep it properly greased,” says Kevin Hershberger, senior market professional for backhoes, Caterpillar. “Since it’s difficult to inspect the condition of specific parts, it is important to make sure that the swing system pins and bearing are getting greased and see the grease extruding from the area. Disassembly and parts inspection will normally be driven by pin and bearing joint wear, which will normally be signaled by noise from the joint.”
Damaged or rupture hoses account for a significant portion of downtime. “The most failure prone items on a backhoe are probably the backhoe hydraulic hoses,” notes Dan Livezey, product specialist, New Holland.
Many problems result from hose routing. “On most machines they are simply strung up on the boom and tend to catch any obstruction as the hoe is working in or near the trench. On the New Holland unit we try very hard to keep the hoses tied closely to the stick and boom.”
In addition, every piece of equipment has commonly overlooked maintenance items. On the backhoe-loader one of these areas is the front axle and trunnion bearings. “These items are put under strain as the machine spends a lot of time with the front axle off the ground,” says Livezey. “Under hard digging the front axle is bouncing a lot. It needs a coating of grease to prevent damage of the bearings.”
To really cut downtime, you need to become familiar with the suggested maintenance intervals on all of the machine systems. “Neglected machine maintenance will result in earlier component failure in virtually any system or component of the machine,” says Hershberger. “If all systems were neglected on a new backhoe loader, the first failures would probably occur in pins and bushings which had not been greased, simply because they are highly loaded, and some require daily greasing.”
There is no such thing as a completely maintenance-free system. “Every machine system has some maintenance items,” says Hershberger. “For example, while Caterpillar Backhoe-loaders have maintenance-free batteries, it is still important to occasionally check things like battery cable condition and engine belt condition to ensure the alternator and the rest of the electrical system will provide dependable service.
Some maintenance items will have more of an impact than others. Livezey explains that the five areas that can have the most impact on backhoe loader uptime are clean fuel, clean oil, daily lubrication of high use areas and inspections of the hard points of the machine.”
John Deere stresses the importance of daily greasing, following all fluid and filter recommendations and following the periodic maintenance recommendations. “They are the best proactive work you can do to keep a backhoe running in prime condition,” says Louann Hausner, backhoe loaders and tractor loaders marketing manager, John Deere. “Those areas that are in the dirt, such as pins and bushings, may be easy to overlook, but are essential to grease daily.”
Proper greasing tops the list
Backhoes are joint intensive machines with many pivot points. Consider the Caterpillar 428F backhoe. “This machine has over 50 zerks on it,” says Jeff Payne, preventative maintenance instructor, Caterpillar. “You need to know where they are located.” Refer to the owner and operator manual.
Missing critical joints can add cost quickly because you are going to gall pins, or wipe out bushings or bearings.” Carrying a few extra grease zerks with you can save time and expense. “I usually carry some new ones with me. If you have a grease zerk that is not taking grease, take the old one out and put the new one in and usually they will take grease,” notes Payne.
Also consider that not all grease is created equal. “Use the right quality and specification of grease to ensure long life of major wear areas,” says Hershberger. Refer to the literature and service plates to ensure that all grease fittings are serviced. Make sure the grease is right for the region that you work. There are a variety of different greases to match the application and temperature of your region.
Keep in mind that improper greasing procedure can create as many problems as it solves. Wipe the grease zerks off with a rage prior to greasing. “We don’t want to pump any dirt that is already on the zerks into the joint,” says Payne. And you should use the right amount of grease. “Typically, if you are greasing daily like you are supposed to, it doesn’t take more than a couple of pumps [from the grease gun]. You are going to hear it or see it start to squeeze out. You don’t need to over grease. That just allows dust and dirt to stick to that grease and that is not a good thing.”
The daily Inspection
“Performing daily inspections is vital to maximize uptime,” says Hausner. “Preventative maintenance can prevent unplanned downtime.”
Perform a walk-around every day before you start the machine and drain water from the drain water from the fuel water separator. Manufacturers provide detailed lists of the daily check points. “Caterpillar provides this information in the Operation & Maintenance Manual shipped with every machine,” notes Hershberger. “In addition, a grease point diagram is located on the engine air filter housing in the engine compartment.”
Many manufacturers, such as John Deere, post maintenance checklists right on the machine. “Due to the fact that customers are entering and exiting the cab on the left side of the machine every day, the preventative maintenance checklist is conveniently located on the left side of the machine, right where the operator will easily be able to access the list,” says Hausner. .
Pay special attention to anything that makes contact with the ground. “As this unit is operating in the dirt the unique maintained items are the loader and backhoe, mainly the bucket pins and the swing pins.” says Livezey. “Backhoe hoses need to be inspected as they are the one item that also makes contact near the trench or dirt pile.”
On the front of the machine check the cutting edge on the bucket. “The cutting edge is a lot cheaper than a bucket so if that starts wearing into the bucket you need to replace that edge,” says Payne. Make sure all of the bolts on the cutting edge are all present and tight.
On the back of the machine inspect the boom and stick for damage. “Look for leaks and rubs,” says Payne. Then check the bucket teeth. “Make sure they are all present and the retainer pins are secure. Those are wear items that need changed out pretty often.”
Check under and round the machine for any leaks. Be sure to check the swing casting area for any damage to the structure, pins and hoses. Visually check the boom, stick and bucket structure, pins and hoses for any damage, looseness or missing parts.
Since this equipment often runs in dirty environments, air filter maintenance is a must. Air filters need periodic checks. If there is not an air restriction gauge, you may need to pull the air filter out and inspect it once a week. If you have an air restriction gauge, go by it. There is no need to unnecessarily open up the filter and risk getting dust in the intake tract. “This indicator will tell you, without opening it up, the condition of the air filter,” says Payne. “It doesn’t need to be changed until it starts getting into the red.”
When performing your daily inspection, remember that even the small details matter. For example, consider an empty windshield wiper container. “It may not seem like much, but if you have a guy in here with a dirty windshield he is going to be pretty appreciative that he can clean the windshield off,” says Payne.
Keep oil clean
While clean oil helps extend engine and transmission life, it is vital to the tight tolerances of today’s hydraulic systems. Just the smallest amounts of contamination can accelerate wear. “Maintaining a clean hydraulics system is essential to the health of all hydraulic components,” says Hausner. “Fluids should be topped off using new oil that meets the specifications found within the operator’s manual.”
Then make sure you don’t contaminate the hydraulic system when topping off the system. “Clean hydraulic oil is very important to long and cost-effective operation of a backhoe,” says Livezey. Good housekeeping is critical. “Oil should not be simply carried around in a 5-gallon pail. Oil in an open barrel is already contaminated. Moisture as well as dirt are not kind to oil.”
“Without clean oil, you risk high repair costs to perhaps the most critical system on the machine,” says Hershberger. “Caterpillar hydraulic filter systems ensure that oil is clean, and require replacement every 500 hours. With our Caterpillar HYDO Advanced 10 oil, replacement can be extended up to 6,000 hours depending on job conditions, regular filter service and SOS (Scheduled Oil Sample) monitoring.”
Attention to small details can help prevent contamination. “It’s very important to clean around any dipsticks before checking the fluid levels. “We don’t want to knock any dirt down those tubes,” says Payne.
And make sure the machine is positioned properly before checking fluids. “The hydraulic tank level needs to have the machine in the proper service position with the bucket flat on the ground and the bucket curled up,” says Payne. “If I don’t have it in that position that level is not going to be right.”
Don’t neglect the tires
Tire checks should go beyond a visual inspection to make sure there are no flats.
“Maintaining tire pressure is essential for maximizing your backhoe investment,” says Hausner. “Proper tire pressure not only minimizes tire wear, but also maximizes traction and stability. This provides stronger backhoe performance and less backhoe service costs.”
“If the pressure is too low the machine will be unstable, operate sluggish and put extreme wear on the sidewalls,” says Livezey. “If the pressure is too high the machine will have no suspension and give a very rough and harsh ride – the operator will be fatigued in a short time. Also tire wear will be extreme in the center of the tire. Finally, the pushing power of the unit will be reduced as the tire will not have the correct footprint to put the optimum amount of power to the ground.”
“Tire heat, wear and life will be affected by air pressure, as well as ride quality and performance, especially in loading and roading applications,” says Hershberger.
Also make sure you do a visual inspection for any cuts.
Maintain extendible dipper sticks
One of the most overlooked areas is the hydraulic extendible dipper. “The hydraulic extendible dipper operates in extreme conditions and is subjected to extreme forces,” says Livezey. It should be inspected on a regular basis, and adjusted to keep it in optimum shape. On the new Holland backhoe, our hydraulic extendible dipper is easy to inspect and also very easy to adjust. In just a couple of minutes you can take out any slop.”
On backhoes with extendible dipper stick it is important to keep clearances within spec. “Correct adjustment of the wear pads is necessary to give you smooth E-stick operation,” says Payne. On the Caterpillar F Series there are four bolts on each side of the stick which can be loosened to adjust stick play. Don’t over-tighten the extendible dipper stick as it will bind and not function properly.