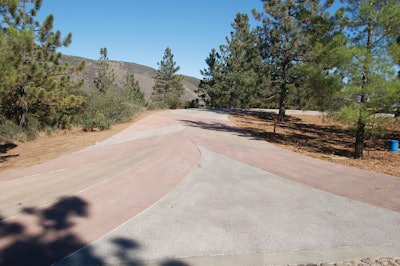
Hamann Construction, a general contractor in El Cajon, Calif., has built hundreds of concrete tilt-up and block building projects ranging in size from 5,000 square feet to over 250,000 square feet; and whenever possible the parking lots surrounding those buildings.
In 2011, after two years of declining business due to the ongoing economic recession, Gregg Hamann, president of the Hamann Companies, had some decisions to make that would affect the direction of his construction division in the years to come.
On a piece of property Hamann owns in Julian, Calif., he decided to build a house. Since forest fires are an ever present concern in the area, he decided to build a concrete home utilizing both tilt-up and poured in-place concrete and as many environmentally friendly building products and technologies he could include in the house to make it a real life model he could show clients.
Before he could build the house though, a driveway had to be built to not only serve as a roadway for all construction traffic but also as a residential driveway. He chose concrete the 700-foot by 14-foot driveway as well as the 150-foot-long drive to the garage. But the real gem of the project is the pervious concrete circular driveway that goes around the front yard, under the fiber optic lit carport back out to the driveway.
Hamann contacted Bob Banka, president of Concrete Management Solutions (CMS), a pervious concrete consultant and NRMCA Certified Pervious Craftsman based out of Medina, Ohio, to help with the project. Hamann emailed Banka some photos of the exterior of what is known as The Julian House, and they started discussing materials and processes that would work well for the job.
Challenge 1: aggregate supply
Challenge number one was the aggregate supply. A 3/8’s gravel pervious mix design did not meet the criteria that Banka has for his pervious concrete. "The key to successful pervious concrete that we have learned over the years is to avoid stone normally used in concrete production," Banka says. "Typically it is not clean enough due to the fines and dust that pass the 50 and 100 sieves. In regular concrete these fines become part of the paste of the final product, but in pervious they become problematic to regulate and force us to use a viscosity modifier. We choose to promote and use a 1/4-inch crushed stone that is typically used in asphalt. Not only does it produce pervious that looks superb, it is 60 percent easier for an owner to maintain due to the smaller surface voids that do not allow leaves and other debris to be ground into the surface as easily as 3/8-inch mix."
"When deciding what stone to use, you have to determine the A.S.T.M. C-29 void content of the stone. This dictates everything else needed to design a well balanced mix," Banka says. "For example, if a stone is clean and has 20 percent voids in it, and we add in a 20 percent paste to it, the finished product should have 20 percent voids, which is almost perfect. Then, to help ensure a mix that is able to travel from the plant to any job we have the batch plant add in a healthy dose of a hydration stabilizer (between 14 and 24 oz/cwt), Buckeye Cellulose Fibers at three pounds per yard and internal curing provided by HydroMax, an absorbent polymer manufactured by ProCure that allows the pervious to cure from the inside out while allowing us to increase our water cement ratio to between a .34 and a .38 inch."
Challenge 2: forming
Challenge number two was how to form the job in the shapes and five different colors (to match the five colors of the concrete in the house) that Hamann wanted to incorporate. CMS has previously used a unique forming material from K-Form Concrete Formwork System - a lightweight, cast-in-place screed rail strong enough to handle all types of mechanical screeds as well as provide control, construction and isolation joints. Although the material comes in straight pieces, Hamann’s crew figured out how to bend the forms and wet set them in concrete. The forms held their shape for two months until the concrete was placed.
Challenge 3: delivery
The challenge here was how to deliver concrete that was batched at 450 feet above sea level but needed to be transferred more than one and a half hours away in the mountains at 3,600 feet. This turned out to be the easiest challenge to fix as the mix design called for a higher dosage of hydration stabilizer, which at 23 oz/cwt allowed the concrete to travel as far as it did and still gave the finishing crew plenty of time to place it and correct any visible blemishes while still in the plastic state.
Challenge 4: placing
Challenge number four was how to place the concrete considering the size of the driveway, the round shape and a tree located right in the middle of the front yard. A Putzmeister TB 130 did an excellent job of placing the concrete.
Hamann used a Lura Lightning Strike Screed for the concrete placement. Since the Lightning Strike is made of aluminum - compared to steel rollers - it can do a better job of screeding pervious concrete, Banka says. In addition, the lighter weight of the aluminum roller was able to screed off the K-form without causing the forms to dislodge.
Challenge 5: curing
Challenge number five was how to cure the surface of the pervious on the day of placement and still be able to place concrete the next day on a section directly next to each previous placement as the sections were strategically placed around the entire driveway. The solution was to use PerviouShield, a spray-on 28 day dissipating curing compound with a built in densifier rather than poly which would not only be problematic in properly securing it, it would also take away from the "green" environmentally friendly process that Hamann was trying to achieve.
On day one of the project, Hamann’s concrete crew and Banka held a class/demo pour to evaluate the mix design, but more importantly to teach the crew how they would be finishing the pervious concrete.
The next day, Banka and Hamann were at the batch plant to go over loading procedures as well as the process and chemicals to be used by the batch man and quality control technicians. The first truck was loaded with the pervious ingredients and integral color and then met at the slump rack where Banka explained the tempering process to the driver and added the HydroMax internal curing to the load.
It took four days to finish the job based on the number of colors used. With careful planning by the contractor, the ready mix supplier and the consultant, the job was completed without issues.