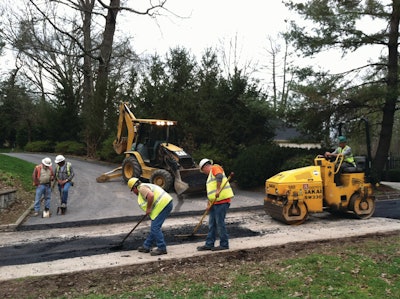
By Steve Blackburn, VP at Navman Wireless
Until GPS fleet tracking came along, every piece of heavy equipment involved in road construction and resurfacing was invisible to logistics managers once it left the storage yard. Today, the GPS location of every machine as well as every on-road vehicle can be captured and displayed on a digital map in real time, complete with icons identifying each asset by type such as mill, paver, reclaimer or tractor.
That’s a big step forward for operations management, but it’s only the tip of the telematics iceberg. Just ask Midland Asphalt Materials, an asphalt supplier and pavement resurfacer with five plants in New York and Pennsylvania and a fleet of 110 off- and on-road assets.
Midland deployed Navman Wireless’ OnlineAVL2 telematics system fleetwide in mid-2012. Beyond core location tracking, results have included dramatically reduced paperwork for DVIR, IFTA, New York Highway Use Tax and off-road fuel tax rebate reporting; improved dispatching, driver communications and preventive maintenance scheduling; and even hard savings. Almost immediately, for example, the company trimmed $500+ in daily overhead by using the platform’s integrated navigation to shorten routes for three tanker trucks that deliver base asphalt to Midland’s hot mix asphalt plants.
“We knew that telematics would allow us to keep track of our fleet, but it’s also increased our efficiency in other areas,” said Midland logistics manager Jeremy Crist. “Adopting fleet tracking has saved us time and money both in the field and in the office, automated a lot of previously manual processes, and made us better at doing our job overall.”
In fact, telematics can help asphalt contractors drive more efficient and profitable operations in a variety of ways. Among the benefits:
1 – Just-in-time dispatching
Knowing where your equipment is makes it possible to dispatch the next machine needed for a project, reassign equipment based on variables such as weather conditions, and respond to other operational needs on a just-in-time basis. This minimizes delays for equipment changes, speeds up paving production, and helps avoid the steep cost of downtime during the paving season.
If you know the precise location of a chip spreader, for example, you can dispatch an asphalt distributor directly to the site at the appropriate time instead of sending it to an intermediary location like a highway department office and requiring the operator to wait for a personal escort to the work site.
2 - Mobile fleet visibility
If your telematics provider offers a mobile app, real-time fleet location information can be retrieved from a smartphone or tablet for on-the-road dispatching as well as faster emergency repairs. “Our mechanics have our telematics app on their phones, so if they have to work on a piece of equipment in the field, they can pinpoint the location of the asset themselves without calling our dispatch center,” noted Midland’s Crist. “This eliminates phone calls and saves time.”
3 – Optimized routing
Telematics platforms that include integrated in-cab navigation/messaging terminals like the Navman Wireless M-Nav 800 enable dispatchers to send job site or other routing instructions directly to each vehicle with a click – either from the office or the road. The terminal displays a map to the destination and delivers audio turn-by-turn directions without requiring the driver to enter an address or geographical coordinates, ensuring efficient routing that not only conserves fuel but also expedites work completion by shortening drive times.
4 – Phone-free driver communications
The messaging capability of these same terminals also allows dispatchers to send job instructions to drivers electronically instead of relaying the information by phone. This reduces the driving-while-talking safety risk, lowers phone bills through fixed-price instant messaging, and frees back-office staff for more productive activities.
“We used to write down job instructions in a log, but drivers wouldn’t always pick up their messages so we frequently had to dictate their assignments by phone. Given the size of our fleet, that took several hours every day, including my entire 75-minute commute to work as well as Jeremy’s 90-minute ride,” said Midland’s Joe Bambino. “Now our drivers can retrieve the information on their terminals whenever it’s convenient and safe.”
5 – Electronic DVIR reporting from the field
Navigation/messaging terminals can also be used for driver vehicle inspection reporting (DVIR) required to comply with Federal Motor Carrier Safety Association (FMCSA) regulations. Terminals can be equipped with pre- and post-trip DVIR forms – customized to the contractor’s needs – that drivers can complete with a few taps. Inspection data submitted by the driver can then be automatically imported into an Excel spreadsheet or another application of the contractor’s choice every day. This ensures immediate notification of vehicle defects and eliminates the delays involved in completing, submitting and inputting paper reports.
6 - Expedited IFTA reporting
Since telematics systems document every mile traveled by date, time and GPS location, the data can be used to automate IFTA (International Fuel Tax Agreement) reporting designed to ensure that each state receives its proper share of fuel use taxes. The raw telematics data can be delivered electronically to the telematics vendor’s IFTA tax services partner for processing and report preparation, eliminating the need for drivers to record their mileage and turn it in to the office for data entry. This reduces clerical overhead while also preventing errors.
The same benefit applies to reporting for regulations like the New York Highway Use Tax (NY HUT), which requires documentation of total miles traveled in the state as well as on toll-paid portions of the New York State Thruway. Midland estimates that automating both IFTA and NY HUT reporting via telematics has saved 20 to 30 hours a month in clerical labor, including time spent chasing mileage sheets from every driver in the fleet.
7 – Higher off-road fuel tax rebates
Currently, asphalt contractors can apply for off-road fuel tax reimbursements for pavers and other off-road equipment simply by reporting the number of gallons of undyed diesel fuel used. However, machines like chip spreaders and asphalt distributors are typically ignored because it is difficult to distinguish between fuel used on-road and off unless the machine is equipped with separate tanks for dyed and undyed fuel. That limits the size of your tax rebate.
Telematics systems can solve the problem by connecting a telematics sensor to each relevant machine’s PTO switch. The system’s sensor report will show how many hours the PTO switch is engaged, indicating off-road work. Quarterly off-road totals for these machines can then be used to calculate what percentage of fuel was used for off-road activities. Adding this data to your tax rebate request will help you collect your full share of these credits.
8 – Fuel savings
Telematics platforms can also help trim the fuel budget through a combination of just-in-time dispatching capabilities that reduce idle time for machines waiting for their turn to work, management visibility into vehicle movement that discourages unauthorized use of company trucks and equipment, and the routing efficiencies gained through the integrated navigation mentioned earlier. When Midland began using its fleet management system to optimize routing for just three trucks, for example, the company cut each vehicle’s drive time by 90 minutes per day, yielding significant reductions in fuel consumption over time.
9 - Cycle time measurement
Knowing key metrics about your operations – such as how long it takes for dump trucks to drive from the plant to the job site, whether they wait too long to unload, how many asphalt deliveries are made to your pavers per mile of road, and so on – can help you spot and correct inefficiencies. Telematics systems capture this information through GPS location and timestamp abilities as well as with a newer feature called machine-centric geofencing.
A geofence placed around each paver, for example, allows the system to detect and document every time a dump truck breaks the geofence to deliver a load, what time it arrives, and what time it leaves. This data can then be used to determine whether your just-in-time dispatching strategy is working and potentially make adjustments to improve your material flow.
10 – Electronic readings for PM scheduling
With telematics, no manual readings are required to document engine hours or mileage for PM scheduling. The data is collected electronically and forwarded to the telematics system’s built-in PM module or third-party PM application. This saves time, reduces errors, avoids delays in checking and submitting hour meter and odometer data to the back office, and allows PM schedules to be tied to actual machine or vehicle usage so that they won’t be serviced too early (wasting money on consumables like oil, filters and tires) or too late (such as past the 500-hour point when your asphalt mill needs teeth replacement).
Yes, fleet tracking technology is also a GPS location tool that lets you see where each sprayer or 18-wheeler is situated at any time, but you’re shortchanging yourself and your business if you don’t use it to its full advantage. Start with the basic capabilities – then add as you go along. You’ll see the results in the field as well as on your bottom line.
Steve Blackburn is vice president of Navman Wireless (navmanwireless.com), a leading provider of GPS-based fleet optimization systems and services that enable companies to monitor, measure and improve fleet-related costs and efficiencies.