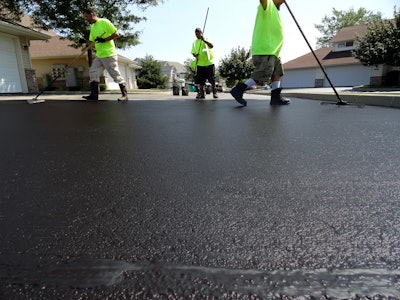
Asphalt parking lots and driveways are capital investments, increasing the value and functionality of a property. Like any infrastructure investment, the asphalt surface must be maintained to keep both value and functionality over time. Maintenance options include resurfacing or replacing the asphalt periodically or extending the service life of the asphalt by sealcoating, thereby greatly reducing resurfacing/replacement expenses.
Sealcoating extends the useful life of the capital asset – an asphalt parking lot – by protecting the pavement from the natural aging process caused by sunlight, water and debris. An added benefit is that sealcoating adds to the “curb appeal” of a paved surface, giving it a clean, uniform look.
There are two essential options for sealcoating: refined coal tar-based sealers and asphalt-based sealers. Refined coal tar-based sealers (RTS) are based on a selectively refined fraction of crude coke oven tar, which is a byproduct of the steel making process. Similarly, asphalt-based sealers (ABS) are based on a selectively refined fraction of crude petroleum oil. Other options are cost-prohibitive for most applications.
There are several important differences between refined tar-based sealers and asphalt-based sealers. The most important difference is RTS protects the underlying asphalt pavement from leaking oil, gas spills and other petroleum products, which are chemically and physically similar to the petroleum from which the asphalt itself is derived. Obviously, ABS cannot, by definition, be fuel resistant. Other advantages of RTS use are greater resistance to natural aging processes caused by exposure to the elements (sun, rain, freeze-thaw, etc.), stronger cohesion (“sticks” to itself better.), and stronger adhesion (“sticks” to the underlying pavement better). Finally, RTS are manufactured to a performance-based specification defined by past federal specifications and now ASTM specifications using ASTM approved testing protocols. There is no industry-accepted ABS formulary, performance testing protocol or specification.
Most sealer manufacturers make both refined coal tar-based products and asphalt-based products. Even though most sealer manufacturers make both, most recommend RTS for most applications because the superior performance of tar-based sealcoat allows the manufacturers to stand behind the performance of their products, enhancing the reputations of their businesses. Research and development projects continue to improve the performance of ABS, but there remains a long way to go.
Some say that RTS is a health threat. But across the two-, three- and four-generation memories of the many family-owned companies in the business of making or applying sealcoat, there are no reports of adverse chronic health effects that can be attributed to exposure to sealcoat.
Expanding the search for possible health hazards to other products made from refined tar, every day millions of people world-wide use coal tar soaps, shampoos and creams approved for use as over-the-counter medicines to treat skin disorders such as eczema, psoriasis and dandruff. Coal tar and coal tar derivatives are listed by the U.S. Food and Drug Administration (FDA) as “generally recognized as safe and effective” active ingredients for use to treat these skin ailments with coal tar concentrations up to 5% in over-the-counter products. Because of its use in medicines, many studies have been performed over nearly a century to see if the patients who intentionally expose themselves to high level doses of coal tar for long periods of time have increased risk of cancer. All the studies have reached the same conclusion: there is NO evidence of cancer.
Controversies about the safety of RTS began because one of the components of coal tar-derived materials is a class of chemical compounds called polycyclic aromatic hydrocarbons (PAHs). The FDA evaluated the safety of coal tar based on exposure of humans to medicinal products that contain coal tar. Classifications by environmental agencies typically evaluate how laboratory animals such as rats and mice react when exposed to very high doses of PAHs dissolved in a solvent and painted on the skin of a shaved mouse. Then they use that information to make assumptions about how humans might react if exposed to PAH-containing materials.
Studies of humans exposed to coal tar can be summarized as follows:
- There is no evidence that low-level or intermittent exposure to coal tar or coal tar pitch has caused cancer in humans. This category describes exposures to RTS.
- There is little evidence that high-level, repeated exposures has caused cancer in humans, and what evidence there is is largely reports from the past, such as chimney sweeps in London in the 18th Century. But, chimney sweeps in other European countries at about the same time did not display high cancer rates. Furthermore, studies from these earlier times are when industrial hygiene practices were virtually non-existent.
- There are some studies conducted in modern factories with high temperature (1000s of degrees Fahrenheit) industrial processes such as aluminum smelting or coke oven gases that show some adverse effects. But, these are not relevant to the materials and applications of sealer.
- Studies performed in 1991 by refined tar producers, emulsion producers and contractors using both spray and squeegee methods proved that PAH exposures were well below and sometimes even unmeasurable using OSHA evaluation methods and established threshold limit values.
PAHs occur naturally. They are all around us and always have been. PAHs are made whenever something organic is heated up or burned. Smoke from forest fires and wood burning fire places contain PAHs. Plants decaying in a swamp or a compost pile are making PAHs. Emissions from planes, trains, and automobiles, cooking food, petroleum products like lubricants and fuels, and volcanic eruptions contain PAHs, as well as materials derived from coal tar.
Some other FAQs about refined coal tar-based sealers:
Why is refined coal tar-based sealer not used as much on the West Coast?
Crude coal tar is a byproduct of making steel. The steel industry is largely located east of the Rocky Mountains. To be close to the source of their raw materials, coal tar refineries that make the base material for RTS are located near where steel has historically been made. Transportation costs make locally produced asphalt-based sealers the cost effective choice on the west coast.
Are asphalt-based sealers cheaper?
All else being equal, asphalt-based sealers are generally cheaper on the West Coast because of transportation issues, but not in the Midwest or East. The pricing of the asphalt-based product is more volatile as it fluctuates with the price of crude oil. Another cost factor can be that manufacture of refined tar-based emulsion is a one-stage process. Finally, to help improve performance, ABS typically require additives for biocides, color, and resistance to ultraviolet light.
Is there a difference between “drying” and “curing” sealer?
Like latex paints, RTS and ABS are applied as water-based emulsions. Evaporation of the water starts the process of adhering the sealcoat particles to each other and to the pavement. Sealer that is dry to the touch means that the surface can be open to foot traffic, but not vehicle traffic. Sealcoat can be driven on once the process of curing is well underway, meaning that the sealer particles are sticking to each other and the pavement. Curing takes more time than drying because it takes longer to drive out moisture that remains within the coating after the initial surface drying.
Why can you sometimes still smell the sealcoat even after the lot is open to traffic?
The odor of refined tar-based sealer is easily identifiable, for good reason: refined tar-based sealer has a very distinct odor, and the human nose is able to detect it at extremely low concentrations. But, just because it may smell bad doesn’t mean it is bad! The smell is primarily the presence of one substance among the many that refined tar-based sealer– naphthalene (Yes! Your grandmother’s closet moth balls). The odor threshold for naphthalene is below three parts per billion (ppb), a very low concentration. To put this concentration into perspective, the odor threshold for nail polish remover is 7,000. That is 2,333 times greater than naphthalene.
According to the American Conference of Governmental Industrial Hygienists, the level of naphthalene that is considered safe for workers is 10,000 parts per billion. So the difference between being able to smell it and worrying about it is huge – 3,333 times greater, to be exact. Even refined tar-based sealer workers don’t experience those levels of exposure. Finally, the odor fades quickly as the sealcoat cures.
Why is sealcoating not recommended if the weather is cold or it’s going to rain?
For the same reason that exterior painting is not recommended in cold or wet weather, sealcoat is not applied in those conditions because the water in the emulsion won’t evaporate. If the water doesn’t evaporate, sealcoat particles can’t begin the process of sticking to each other and the coated surface.
Is it poisonous?
Dried sealcoat does not wash off and is no longer sticky. If any sealcoat – either asphalt-based or refined tar-based – washes off before it dries, it can suffocate fish and other aquatic life. The fish are not poisoned. Autopsies have shown that the fish suffocate because sealcoat particles cover the fish’s gill plates. Dried sealcoat particles are not bio-available people and most other species.