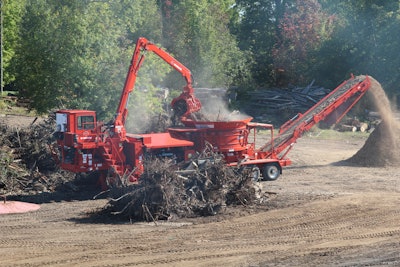
There are signs of recovery in the grinder market. “With the pipeline activity we have seen a real resurgence,” says Tom Mitchell, Northeast regional manager, Morbark. “Tub Grinders have been a big part of that.”
After several lean years, larger tub grinders are moving again. When selecting a large tub grinder, capacity and production are key considerations.
“Large land-clearing contractors look at the capacity – the diameter of the tub,” says Jay Sarver, sales manager, Vermeer. “That effectively controls the length of material that you can feed through it.” They also care about the overall weight and the resulting ground pressure.
Horsepower dictates the production rate. But in terms of sizing, there are no easy rules of thumb. “Every material grinds a little different. In addition, the support equipment can dictate how much material you can physically bring to the machine and get into the grinder,” says Mitchell.
To meet the varying production requirements, grinders offer several different power options. “For instance, the Morbark 1300B offers a choice of 800 or 1,100 hp. “There is a wide range depending upon what the contractor wants to do,” says Mitchell.
There has also been an electronics revolution primarily driven by emissions regulations. “We pay more for horsepower today than we did ten years ago. That is due to emissions and electronics,” says Sarver. “But the technology is much more responsive. There are on-board computers on grinders that weren’t there ten years ago.” They control the feed rate, provide engine information and data live via remote, and provide several different parameters for the operator to interface with the machine while it is running.
Automatic control of the feed rate has dramatic increased productivity. “Proportional feeding where you adjust your tub rotation, which is your feed speed, depending upon your engine load and how hard you are working it with the application has been a big advancement over the last couple of years,” says Mitchell.
“The electronics have been very reliable. Electronic controls just require increased education about how the systems work,” says Glenn Salyer, Red River Ranch. “The productivity through the smart grind is 20% more and the fuel consumption is down with the new electronics.”
Red River Ranch, Stanton, KY, currently has four Vermeer TG9000 and three TG800 tub grinders. It manages three yard waste facilities and has contracts with the City of Nashville and the City of Lexington.
Some features, such as a hydraulic clutch, have almost become standard. “The majority of big machines now have a hydraulic clutch,” says Mitchell. “PT Tech and Twin Disc are two of the hydraulic clutch offerings that we have.” While mechanical over-center clutches are still available, the industry is moving toward hydraulic clutches. While hydraulic clutches are more expensive, they offer self-adjustment, increased durability and remote operation.
All of Red River Ranch’s grinders currently have PT Tech hydraulic clutches. “We have used manual clutches in our rock crushers, but the hydraulic clutches really add a lot of safety and durability because they will not let the operator start with a jam,” says Sayler. “There is really no way to damage that hydraulic clutch other than oil contamination or just a lot of abuse.”
Current grinders run by St. Louis Composting also use PT Tech hydraulic clutches. The previous generation grinders, such as the Morbark 1300A tub grinders used manual clutches. “One advantage of the hydraulic clutch is operator safety,” says Patrick Geraty, St. Louis Composting. “The operator doesn’t need to get into the doghouse to engage the clutch.” It is done from the cab.
St. Louis Composting operates six facilities around St. Louis, MO and owns a fleet of horizontal, tub and slow-speed grinders. Tubs primarily grind yard waste, logs and pallet waste. The company also does a fair amount of contract grinding, including land clearing projects.
Magnetic tail pulleys on the discharge conveyors have also almost become an industry standard. “Probably 90% of our tub grinders go out with magnetic tail pulleys,” says Sarver. The end customer usually wants product as clean as possible. In addition, metal is worth money. “We have a nail shoot that attaches to the back of our discharge conveyor. As the metal comes around and the magnetic tail pulley captures it, the metal drops down a nail shoot on the discharge.”
Prevent Thrown Objects
Thrown objects have always been a concern with tub grinders, but options exist to minimize the safe working radius around the machine.
Vermeer tub grinders come standard with a two-piece Thrown Object Restraint (TOR) system. It consists of a hinged tub cover that covers about a third of the tub and a deflector plate mounted to the table just above the mill. It covers about one-third of the up-cut side of the mill. “The two-piece system allows you to work in a lot tighter work zone than what traditional tub grinders have to offer if there is no restraint system,” says Sarver.
The tub cover is hinged and can swing open. “If you work in a land-clearing application where you don’t have any traffic, you can swing the swing the tub cover open and feed the machine as you would without it,” says Sarver. But the tub cover actually proves beneficial to feeding certain materials. “When you feed green waste or wood waste, the cover actually helps funnel that material down into the middle.” Longer, 12-ft. logs run up onto the cover and it helps position the log vertically and feed down through the mill.
“The safety features in the Vermeer grinders, the tub shielding, the mill shielding, the thrown object deflectors are key for us,” says Sayler.
Morbark also offers options to minimize the risk of thrown objects. “We offer hydraulic covers that will close off the top opening,” says Mitchell. “Typically those are used when you are shutting the machine down at the end of the job. Then we offer a fixed cover that will help control projectiles on the side where they are most susceptible of coming out.”
Green Waste Recyclers has a lid for its Morbark 1300B, but the company also carefully evaluates where to place the tub grinder on the jobsite. “Look at your jobsite and set up the safest possible way,” advises George Partlow. “Regardless of what the material is, you can always bring the material to the grinder.”
Green Waste Recyclers has been in business for 15 years and is currently on its fourth tub grinder. The company currently owns two grinders, a Morbark 1300B tub and a 4600XL horizontal. The company specializes in grinding for several municipalities
Consider an integrated grapple
Integrated grapples offer several benefits including better visibility and the ability to grind with less support equipment on the site. “With longer material, you have a view into the tub to see what is going on,” says Mitchell. “You can manipulate the load to avoid bridging and to make sure that material is gravity feeding to the mill. You get a better sense for what is going on at the mill.”
Approximately 90 percent of large tub grinders sold by Morbark include an integrated loader. “The integral loader grapple offers an advantage in any situation outside of re-grinding,” says Mitchell. The only Morbark machine that doesn’t offer an integrated loader is the 1600. “That machine is typically so productive it takes two rather large excavators just to keep it fed.”
Vermeer also offers integrated loaders. “Our cab is about 17 ft. up in the air so the operator has good visibility down into the tub as he is loading the material,” says Sarver. The loader offers 370-degree rotation. “You can essentially stage material 180-degrees around the machine.”
Whether or not an integrated grapple is beneficial depends on your operation.
“In most cases land clearing contractors have excavators because they use excavators on land-clearing jobs anyway,” says Sarver. “Whether or not the unit has a loader isn’t as important as other features because you can feed them with the excavators.”
“Integrated loaders do not work in our business model,” says Sayler. “You almost always need two machines with an integrated loader. You need some way to push away and then you need some way to bring the material because you can only reach out to 20 to 30 ft. radius of reach.”
In many applications Red River Ranch supports its tub grinder with a single wheel loader. “Our machine of choice is a Cat 966 wheel loader with a 12-yd. light material handling bucket,” says Sayler. “That machine fits well with the capacity [of the tub grinder]. Depending upon the job, that machine can load the grinder, push the product away and load a few trucks in between. And when we are not using the grinder, we can use the loader for something else.”
“Where I see more applications for a self-contained machine are contract grinding for municipalities, storm cleanup or where there is a designated site,” says Sarver. In these instances they have a truck and a wheel loader to push material away from the grinder and material up to the integrated loader.
“The only way we have ever bought the tub grinders is with the built-in loading systems,” says Geraty. St. Louis Composting typically uses track loaders or wheel loaders as support equipment for its tub grinder. “The built-in loading system eliminates an additional piece of machinery, which would have to be an excavator, to feed that machine. It’s an all-in-one package.”
Green Waste recyclers also uses an integrated grapple on its Morbark 1300B. In land clearing operations this is often paired with a John Deere 644 wheel loader with a high-tip bucket and/or a John Deere 330 excavator.
The case for on-board air
On-board air compressors are a very popular option. “It is uncommon to sell a machine without one,” says Mitchell.
“We have air compressors on all of our units,” says Geraty. “They are for keeping the machine clean, blowing out radiators and changing inserts.”
Both of Green Waste Recycler’s grinders – the Morbark 1300B tub and the 4600XL horizontal – are equipped with air compressors. “They are a must,” says Partlow. These compressors are used to power tools for tool and screen change outs and to clean the machine every night.
Red River Ranch has a different approach. Only one of its grinders is equipped with an air compressor. “All of our operators have their own service trucks and air compressors,” says Salyer. “We found out it is easier for to maintain a service truck for the guys to carry the tools and wear parts. I don’t think there is a right or wrong approach, we just found out it works better for us. The compressor on that grinder, after so many years, eats so much dust and is exposed to so much vibration.”
Many Red River Ranch operators carry backpack leaf blowers to clean the grinders at the end of the day. “It is hard for an air compressor to spin that much air to blow it off,” Salyer explains. “You need the volume more than you need the pressure.”
Evaluate ground pressure requirements
Tracks are becoming more common on grinders. “We are doing quite a bit with track machines, more on the clearing for the pipeline side,” says Mitchell. “We sell more chippers and horizontal grinders than tub grinders [with tracks], but there is an occasional tracked tub grinder as well. As far as our tub grinder goes, we offer tracks on everything except our largest – the 1600. Because it is such a big machine (over 95,000 lbs.) it doesn’t lend itself to tracks.”
Often tubs are placed on sites where tracks are not necessary “A track grinder is great for tracking down a right-of-way or going long distances, but at the end of the day, if you are going to be taking product out of the field, then usually you have a pretty good landing pad because you need the ability to put trucks on site and load them,” says Sarver.
Instead, Vermeer offers flotation tires on its tub grinders, also known as Super Singles, “Flotation tires give you much lighter ground pressure [that standard tires],” notes Sarver. Another advantage is that mud often packs between standard dual tires, which creates problems going down the road.
But specific circumstances dictate the correct choice. For instance, Red River Ranch prefers conventional duals over Super Singles due to the availability of take offs from the local school bus fleet.
“We had machines with Super Singles,” says Salyer. They are useful if you need them for weight considerations. But replacement tires are needed on occasion as the tires can be damaged when the grinders are dug out. “We can get take-off school bus tires that are really good. There are a lot of casings available real cheap.”
Investigate new suspension option
Mechanical suspensions have long been the norm for tub grinders, but now there is another option.
Vermeer offers an air suspension on its TG7000. “When we built the 7000, we added the air suspension because we wanted a grinder that was high horsepower, high throughput and on as light of platform as we could get so we could travel off road and have good ground stability,” says Sarver. The air ride suspension provides an even load across the wheels so your ground pressure is more consistent across your triple axles. With a mechanical suspension the front axle typically carries more weight than the rear axle due to the weight of the mill and the engine.
“With an air-ride suspension, once the grinder is put in place the customer dumps the air bags on the grinder,” says Sarver. So you are grinding on the rigid framework. “You are not continually working the suspension as you are grinding.”