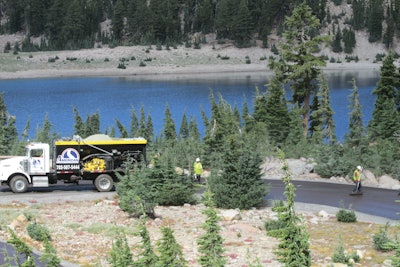
American Pavement Preservation (APP), an asphalt and paving contractor specializing in slurry seal, crack seal, seal coat, and asphalt placement for over 30 years, recently had the opportunity to perform pavement preservation at two national parks located on the west coast.
Lassen Volcanic National Park, located in northeastern California, features the largest plug dome volcano in the world and the southern-most volcano in the Cascade Range of mountains. The other park, Oregon Caves National Monument, is located in the northern Siskiyou Mountains of southwestern Oregon. Both locations had unique challenges – from foreign weed seeds to tourists to bears.
“These two parks are located in mountainous areas with varying elevations and heavily shaded by trees,” explains Eric Reimschiissel, president of APP, which is headquartered in Las Vegas. “The asphalt on these roadways was continually exposed to freeze-thaw conditions, snow plowing, and chain or studded tire wear.”
The national parks had used several pavement preservation practices and application processes in various locations throughout the parks to maintain the roadways. It was determined that micro surfacing was the correct method of pavement preservation for both parks’ environments, says Reimschiissel.
Micro surfacing is a versatile tool in the road maintenance arsenal. It’s a polymer-modified cold-mix paving system that can remedy a broad range of pavement problems.
Micro surfacing begins as a mixture of dense-graded aggregate, asphalt emulsion, water and mineral fillers. The new surface is initially a dark brown color and changes to the finished black surface as the surface cures, permitting traffic within one hour in most cases.
For both projects, the micro surfacing was a Type 2 FHWA specification. Emulsion and aggregate were located in Northern California and hauled into the parks.
Lassen Volcanic National Park
The Lassen Volcanic National Park project requirements for APP included placing micro surfacing on roads intermingled with approximately 600 campsites, including the parking areas at each campsite. Micro surfacing was also placed on parking lots surrounding the park stores and delivery areas, park employee residential areas, maintenance yards, and the law enforcement facility.
Micro surfacing is made and applied to existing pavements by a special machine that carries and mixes all components on site, then spreads the mixture onto the road surface. Materials are continuously and accurately measured, then thoroughly combined in the machine’s mixer. As the machine moves forward, a “surfacing” box spreads the width of a traffic line in a single pass.
For both projects, APP utilized two micro surfacing machines with a micro surfacing auger spreader box, emulsion tankers, storage trailers and loaders.
For the Lassen project, APP placed micro surfacing over chip seal near the north entrance to the park for review and analysis by park officials.
Communication and cooperation was key during the Lassen project, says Reimschiissel.
“We were performing this work during the height of tourist season, so coordinating the work with park officials was paramount in order to minimize any interference with normal park operations and park visitors,” he says.
Camping areas were alternated and vacated for 48 hours for the work to be performed, including all cleaning and surface preparation prior to the micro surfacing being placed. Access to the park store, parking lots, employee residential parking, maintenance areas, and law enforcement was required at all times. The “cut- in” work had to be accomplished prior to the roads being completed.
The project Lassen Volcanic Park was completed in August 2013.
Oregon Caves National Monument
The work at the Oregon Caves National Monument involved placing micro surfacing in an environment of higher humidity and frequent chance of rain. For this project, APP placed micro surfacing on main access roads, visitor parking lots, maintenance areas, and park headquarters parking.
“Work at the Oregon Caves was different from that in Lassen in that there were to be no full road or parking lot closures allowed during the course of work,” says Reimschiissel. “The entrance road to the caves and the resort at the caves is off a narrow 18-foot road. The micro surfacing work had to be performed in such a manner as to allow visitors, emergency services and employees access to the Caves Monument at all times.”
As with Lassen, partnering with the park services provided positive solutions to difficult scenarios when considering the visitors to the facilities at both locations. “Working with the chief of maintenance at Lassen Park and the chief ranger at the Oregon Caves proved to be the most effective communication link for the work to stay on schedule,” says Reimschiissel.
Performing micro surfacing work within a national park always has its share of unique challenges. In addition to being mindful of park guests, APP had to consider the well-being of Oregon Caves’ inhabitants, both animals and plants alike.
“Special care was taken to be sure the equipment was extremely clean without and dirt of debris because park management was concerned about weed seeds that were foreign to the park, keeping the native vegetation growing only,” says Reimschiissel.
Because wild animals use the park as their home, APP’s crew completed a bear training class to provide information about the natural habitat of the bears and address any concerns regarding interactions of the crew and native bears in the park.
Protecting the environment was critical, and APP’s crew had to set up storm water protection devices and use BMP (Best Management Practices) at all time. Plastic sheeting was placed under the equipment to prevent any spills to avoid any contamination to the environment.
“Because of the critical nature of the historical park stone walls, walkways and buildings, our crew took great care to prevent any asphalt from getting on these locations,” says Reimschiissel. “Polyethylene plastic sheeting and duct tape were placed to prevent any spills or splatter.”
Safety was a very big part of the project with fire extinguishers in all locations and fire prevention training was completed by the crew.
Reimschiissel notes that both the subcontractor, Eagle Peak Construction, and his APP crew did an excellent job on both projects and were a large part of the success each project had.
"I have to give a big thank you to Eagle Peak Construction and my own crew," he says. "The people on the crew were experienced and did an excellent job from coordinating the work with all the various locations and doing an excellent quality project."
The project at Oregon Caves National park was completed in September 2013.