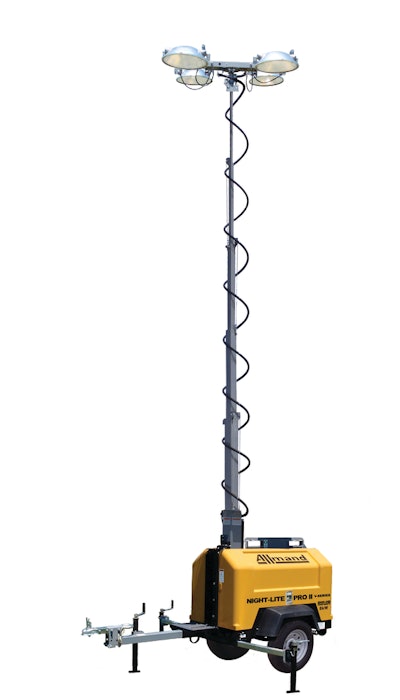
On any jobsite, the most important aspect of safety is the well being of the workers as well as pedestrians that happen to be on or around the jobsite. It's essential to make sure the product you choose to light your jobsite is set up correctly to provide the appropriate amount of light as well as a safe jobsite. It's also very important to position and adjust the lights correctly to avoid blinding workers or creating a glare hazard for nearby motorists.
Some companies claim to have non-glare light towers, and while there are ways to make the light less invasive, there is really no such thing as non-glare lighting. Any type of light that is shined into a person’s eyes is going to cause glare and be a safety issue. Some models allow for all of their lights to be aimed directly down for critical applications to prevent the light from blinding those on or passing around the jobsite. Visor shields are also offered by some manufacturers in order to shield some of the light from passers-by while still providing adequate light to illuminate the appropriate area.
Protecting sensitive environments is always a concern, not only for the environment but for the operator’s bottom line as well. Fines and clean-up costs for even the simplest oil or fuel spills can quickly eat up any profit. A fluid containment system holding at least 110% of the fuel and crankcase oil in the light tower can help prevent spills, and their resultant environmental damage and expense.
Fuel capacity is also an important factor when choosing a light tower. Some jobsites are very large or remote and the light towers need to be located in hard to access locations, so it can be very beneficial for a light tower to have a larger fuel capacity in order to lessen the number of times a fuel truck has to service them. Some manufacturers offer fuel tanks with 100 gallons of capacity, allowing the light tower to operate for extended periods before refueling. This kind of savings can add up very fast, especially on large and remote jobsites.
Hazardous gas accumulation is a real problem in the oil and gas industries. When you need to operate in this environment, the possibility of an accumulation of dangerous gases can create a serious danger. Light towers equipped with hazardous gas detection systems provide an extra layer of safety. The systems are designed to monitor hazardous gases, warn of any accumulation, and provide status identification by triggering lights, warning sirens, and shutting down the light tower.
Other aspects to consider on a jobsite would be wind and mother nature. Some manufacturers offer four- or even five-point stabilizer systems to ensure that a light tower can remain operational in gusts of up to 65 miles per hour. Making sure the product won’t be blown over, possibly causing damage to itself, other equipment, or bystanders, is very important and should be carefully considered.