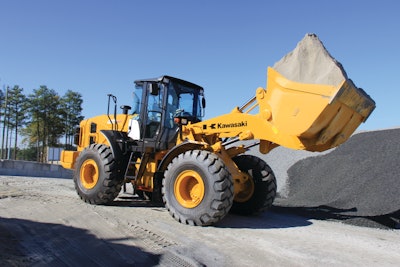
By design, wheel loaders are very versatile tools on a jobsite. Whether operating in special applications such as hot slag, logging, scrap and recycling, or any of the mainstream applications, wheel loaders carry some inherent safety concerns. Here are a few reminders, before you even turn the key.
Perform a walk-around inspection
The careful safety inspection of jobsite machinery should be an integral part of an operator’s daily schedule. Wheel loaders should be inspected at the beginning of every shift prior to starting the machine.
Begin with a review of the overall condition of the wheel loader:
• Check transmission fluid level
• Look for wear in the driveline area
• Inspect all hoses for wear and leaks
• Check for loose lug nuts and general wheel condition
• Look at tires for embedded stones, foreign material, cuts, overall tread condition and sidewall condition
• Verify correct tire pressure before beginning work
After a general exterior inspection has been completed, specific attention should be paid to the business end of the wheel loader: the lift arm and bucket. These areas are both the identifying components of a wheel loader as well as the most dangerous.
When reviewing the conditions of the lift arm:
• Inspect pin areas for wear
• Look for loose or broken greasing tubes
• Look for loose or leaking lines, fittings or hose clamps
• Check coupler for wear (if equipped)
• Check all lube points for proper lubrication
Next, move to the bucket:
• Inspect the cutting edge (if the cutting edge isn’t square with level ground you might have an under-inflated tire)
• Inspect the edge for loose, broken or missing parts
• Look for unusual wear patterns and cracked welds around the bucket
• Examine the cylinder rod (make sure the tilt cylinder rod isn’t scratched or dented)
Once the equipment inspection is complete, give some thought to your own safety. Consider your safety gear and use it.
• Hard hats
• Hearing protection
• Safety vest
• Gloves
Employ safe practices
• Mount and dismount - Always use the handholds and steps to maintain three-point contact when climbing on or off any piece of equipment. Three-point contact means either two hands holding the handholds and one foot on the step or two feet on the steps and one hand on the handholds.
• Use your seat belt
• Check your mirrors
• Check your settings
• Check your gauges
• Check around you
While regularly scheduled safety inspections will reduce the risk of injury, wheel loader injuries often occur during simple daily practices and might be prevented by following the best practices above. Operators must take care to use proper safety procedures to protect themselves, their equipment, and their jobsite, now and for the future.
Technicians, even on today’s loaders, might have to work close to an open engine compartment with a running engine where the sound levels during diagnostic work can be quite high.
Today there are many types of hearing protection that were either not available 20 years ago or were frowned upon by co-workers as being “unfashionable” and were unused. Foam ear plugs costing only a few cents are now much more common and acceptable throughout the industry and are very effective in preventing hearing loss. Over the ear “ear muffs” are also more widely accepted and more comfortable than ever before.
With an eye toward maintaining hearing for life, proper hearing protection should be used whenever there is a high sound level around equipment.
So preventing injury, short term or long term, should be the personal goal of every owner and every operator.