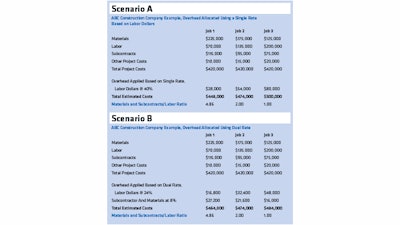
Last month, we provided an article on overhead calculation and rate. That was Overhead Rates 101. In this month’s guest column, Ken Hedlund, Somerset CPAs (somersetcpas.com), introduces a more sophisticated approach to rate calculations that may help you fine tune bids toward hopefully a higher acceptance percentage.
A significant factor in the profitability of any company is an appropriate allocation of its overhead. This fact is especially true for construction companies. Just like direct costs, overhead is the real cost of doing business. In addition, projects vary significantly in mix of costs — predominately comprised of direct labor, materials and subcontractors. Depending on the mix of costs, different projects inherently consume varying degrees of overhead resources. An appropriate estimate of overhead should be considered during the estimating and bidding process, and overhead should be applied to projects as they progress to en-sure overall firm profitability.
The procedure for analyzing overhead includes identifying those expenses that should be included in overhead, determining an appropriate allocation method (labor hours, labor dollars, job costs, etc.) and developing an overall overhead rate to apply to jobs as they progress.
Most contractors allocate some overhead costs to projects. Using a single rate method based on labor hours or labor dollars appears to be the most commonly used method. However, this method has an inherent flaw. Under this method, projects that are predominately self-performed and therefore have significant labor costs will also have a heavy allocation of overhead. Alternatively, projects that are not self-performed and are predominately subcontracted may have minimal or no overhead allocation. Therefore, the single rate method utilizing labor hours or dollars does not consider the potential mix of costs projects can have and, in effect, will penalize projects that are labor intensive.
We support the presumption that labor is the major driver and consumption of overhead resources. However, not all overhead costs are caused by direct labor costs. Alternatively, not all overhead would be eliminated if there were no labor costs. Managing subcontracts, materials and other project costs also consume resources and should have an allocation of overhead.
The most accurate method of overhead recovery is the dual overhead rate method. This method utilizes two different overhead rates — one for subcontractors and materials and one for direct labor. As previously indicated, labor represents the largest component of risk and opportunity for profit on most construction projects. However, labor also consumes and generates the greatest amount of overhead. Therefore, under the dual method, labor will be allocated to the largest portion of the overhead. However, a second rate will also apply overhead to projects that have a component of subcontractors and material costs.
The dual overhead rate method, developed by FMI Corp., is based on years of research on the behavior of overhead costs. It has been proven that overhead costs vary as the ratio of materials and subcontracts to labor varies. This supports the theory that overhead (as a percent of total direct cost) varies inversely with the Materials and Subcontractors to Labor (M&S/L) ratio. The formulas for determining the dual overhead rates are provided below:
Rate on Materials and Subcontractors = Allocated Overhead/[(X) * Labor] + Materials and Subcontractors
Rate on Labor = (X) * Allocated Overhead/[(X) * Labor] + Materials and Subcontractors
Dual Rate Calculation Example
Values for X are determined by the M&S/L ratio. These values are available in a precalculated published schedule called “Dual Rate Recovery, Table of Overhead Factors.” For a copy, please contact [email protected].
The calculation for our example company, ABC Construction Company, is based on the financial information obtained from its budgeted financial statement:
Materials -$7,500,000
Subcontractors - $2,500,000
Labor - $5,000,000
Overhead - $2,000,000
The dual rate calculation can be obtained as follows:
① Calculate the M&S/L ratio: ($7,500,000 + $2,500,000)/$5,000,000 = 2/1, or 2
② Use the Dual Rate Recovery, Table of Overhead Factors to obtain the X value of the M&S/L. In our example, an M&S/L ratio of 2 yields an X value of 3.13.
③ Calculate the dual overhead rates using the formulas provided above.
Rate on Materials and Subcontractors = $2,000,000/[(3.13) * $5,000,000] + ($7,500,000 + $2,500,000) = 8%
Rate on Labor = (3.13) * $2,000,000/[(3.13) * $5,000,000] + ($7,500,000 + $2,500,000) = 24%
Thus, the dual overhead rates are 8% of Materials and Subcontractors cost and 24% of Labor cost.
For comparison purposes, if ABC Construction Company allocated overhead using a single rate calculation based on labor dollars only, the rate would be calculated as follows:
Total Overhead - $2,000,000
Labor Dollars - $5,000,000
Overhead Rate Based on Labor Dollars Only = 40.00%
Scenarios A and B (page 50) provide an example of a project that utilizes a single rate based on labor vs. a dual rate using the calculations above.
As you can see, when comparing the two overhead allocation methods, the overhead applied to projects 1 and 3 vary widely. But Project 2 remains the same regardless of the method. This is because Project 2 has the same material and subcontract to labor ratio as the company has with its budget. If every project had the same ratio as the company budget, either overhead allocation method would be accurate. But in the real world, projects vary and the mix of costs can vary significantly. The dual rate method has been found to be more accurate than any other method.
It is also important to note that the development of dual overhead rates should be based on projected future costs. The best way to determine dual overhead rates is to use a comprehensive 12-month budget tied into the company’s fiscal year. If this computation is not possible, a 12-month current statement may be used. However, when this is done, the company is being guided by last year’s information. You should recalculate the dual overhead rates at a minimum on an annual basis. Significant fluctuations in the company’s business operations may require updating the dual overhead rates more frequently.
The biggest argument we have heard contractors use against utilizing the dual rate method is the perception that it is complicated. But practically speaking, the calculations are simple and easy to apply, and no more effort is required than with any other method.
The benefits of utilizing the dual overhead rates method are great. Comparing overhead costs to industry norms and benchmarks will identify those costs that should be monitored to assist in improving profitability. This is a “best practice” for the industry that you should consider.
The Lines Are Open
The last two months, we discussed ways to improve your hit ratio and overall profits. As with any other business, the devil is in the details. You have to understand the numbers and have a system to provide data that lets you know how you’re doing from a financial performance standpoint. An industry specific system will allow you to calculate and apply overhead rates to the type of work you’re getting.
We’re keeping the Contractor Help Station hotline open, so feel free to contact me at (708) 347-9109 or [email protected].