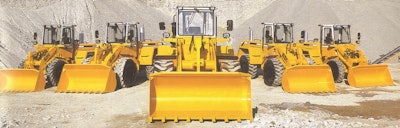
Prior to the 1960s, much of construction equipment still relied on winches and cables. “Dozer blades were moved with winches and wire ropes,” recalls Keith Haddock, national director of the Historical Construction Equipment Association. “Shovels and backhoes were operated with cables with winches and clutches. There were no hydraulics on most machines.”
This resulted in very simple machine designs. “Anybody could fix the cable systems in the field with a hammer to install wedges and renew the rope. It was easy, but not as efficient as the hydraulic systems,” says Haddock.
The adoption of hydraulics transformed equipment design. “The introduction and development of hydraulics was pretty significant when you consider cranes and excavators were mostly rope-operated equipment,” says John Patterson, former CEO and president of JCB. “The development of hydraulics led to equipment that is much more productive, much more cost effective and more durable. Starting in the ’60s, there was a transition to hydraulics.”
“By the end of the decade, almost everything was hydraulic powered,” says Haddock. “There were some exceptions, but the hydraulic excavator, for instance, took over from the old cable machines. By the end of the ’60s decade, there were not many small cable-operated shovels.” The larger cable-operated shovels were still very popular in the surface mining industry. “But in the ’60s, even some of those were being challenged with large hydraulic machines.”
50 Years of Construction Equipment History: Interactive Timeline
More Pressure and Tighter Tolerances
One of the most important advancements has been the increase in operating pressures. “If you look at any hydraulic excavator in the ’60s that was available in America, the average operating pressure was 2,000 to 2,500 psi,” says Haddock. “Today, most excavators operate between 5,000 and 6,000 psi.”
This has increased machine efficiency. With higher pressures, the pistons in the hydraulic cylinders can move more quickly vs. the comparatively slow and sluggish operation under the lower pressures.
The tighter manufacturing tolerances allow parts to be made more accurately. “The advancements were specifically in the components themselves, like hydraulic pumps, hydraulic cylinders,” says Patterson. “They were manufactured to much finer tolerances that improved the durability and hence productivity and reliability.”
“This means they are less prone to leakage,” says Haddock. “When hydraulic machines first came out, they were always oily. They were regarded as dirty machines. A few contractors pulled away from that, but they came back when hydraulics improved.”
Initially, there were improvements in the effort required to operate these systems and then advances were made in operator precision. “The evolution of hydraulic systems first made them more controllable and then more fuel efficient,” says Brian Rauch, senior vice president of engineering, manufacturing and supply management, Deere & Company. “We now have pressure-compensating and load-sensing systems.” If you look back 30 or 40 years, the control levers were connected to the hydraulic valves via mechanical linkages. “Now we have pilot- or electronic-controlled hydraulics.”
Hydraulic pumps have evolved and become more efficient. “We have gone from gear pumps to high-pressure piston pumps where you can get even better performance,” says Patterson. This allowed the development of highly efficient load-sensing hydraulic systems.
50 years of construction-equipment history in an interactive timeline