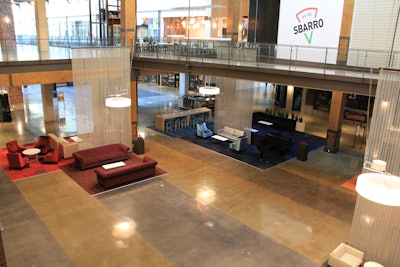
Opening in October 2015, the Liberty Center, located on I-75, between Cincinnati and Dayton, Ohio is a $350 million real estate development featuring retail, office and residential buildings. The sprawling campus includes the first enclosed mall to be built in the U.S. since 2007 and polished concrete floors plays a prominent part in the overall theme of the shopping center.
Joe McGovern, senior project manager at Hoar Construction (Birmingham, Alabama) was tasked with guiding the mall construction, as well as finding solutions to a project budget which could have ballooned out of control.
“All of that came about in the context of a broader mission for Hoar Construction,” says McGovern. “Our client, Steiner and Associates, came to us and asked what we could do to find a way to make some budget cuts for the project. They took that task away from the architect and put that on our team.”
The Liberty Center was designed to look like a rustic, old steel mill. Visitors will notice exposed iron, bricks and steel forms. Installed on the exterior of the building is a 90 foot tall, faux smoke stack that will not be painted. Designers wanted the smokestack to age naturally to create an early 1900s look.
At the request of the owner, Steiner and Associates, McGovern and his team examined the design and offered some ideas—one of which was changing the specified use of over 100,000 square feet of ceramic tile to polished concrete throughout the public concourses of the mall.
“All of that ceramic tile costs big bucks,” McGovern says. “We determined there were other ways to get a premium floor inside the mall, saving money and giving the project a better look for the overall theme of the building. Taking the standard, off-the-shelf option of ceramic tile would not fit into the desired theme. The owner was agreeable to dye and polish the concrete floor which would also offer liberal design parameters.”
McGovern was told the design could contain no more than four colors and no tight, checker board patterns. "Polished concrete offers design flexibility to designers," McGovern notes. “How much flexibility do you have with ceramic tile? Can you do circles?”
“With polished concrete, we are able to offer radiuses and diagonals. If the contractor has to cut a tile to achieve a specific design, the price of the project starts to ratchet up and up and up,” McGovern says. “It was important for the owner and the designers to know with a polished concrete option, I can chalk a line wherever I want, all day long, but the cost remains the same.”
Design flexibility and the cost savings convinced both parties polished concrete was the premium flooring choice.
Within the context of the budget, the budget drives the design and the budget drives the project. Canceling the ceramic tile floor option gave designers a chance to be creative and save money.
“And that’s what every designer wants to hear. Designers will receive more design liberties with this system (polished concrete) than with the stale, old, ceramic tile.”
Jeffco Concrete
Jeffco Concrete (Tuscaloosa, Alabama) was chosen as the contractor responsible for polishing over 100,000 square feet of concrete on two levels of concourse at the shopping center.
Jeff McCool started his contractor business in 1983. He began polishing concrete in 2000, transforming his contracting business into what it is today. Jeffco Concrete specializes in polishing concrete at schools, churches and large, industrial facilities. A resurgence of retail projects has helped Jeffco Concrete grow to performing work across 15 states around the country.
“You name it, we’ll polish it. We are a polished concrete contractor,” McCool proclaims.
McCool’s first machine was a HTC 800 HD and that machine is still on the floor, polishing. While the machine has been rebuilt several times, it’s still running and he now owns 34 grinding units in the company’s fleet.
With a 40,000 square foot warehouse, McCool employs seven crews to perform the work and he says polished concrete is 90 percent of the company’s volume per year.
McCool sums up his work perfectly, “If you place a perfect slab, I’ll polish you a great floor.”
McCool visited the jobsite in October 2014 and explained to the owner in detail about the process of polishing the floors. He says he discussed the floor maintenance options, the life cycle of the floor and of course, the cost.
Additionally, McCool helped coach McGovern and his team to develop an overall feel for what could be done with the floors. While ceramic tile was priced out at approximately $9.50 to $10 a square foot, a dyed and polished concrete floor was worth four dollars a square foot.
“We were looking at 107,500 square feet of concrete floor to be dyed and polished. Throw four dollars a square foot on that and it certainly gets an owner’s attention,” McGovern says. “Choosing a polished concrete floor offered a phenomenal savings.”
Before long, Steiner and Associates wanted to visit McCool in Alabama to see some completed projects.
“We walked around a lot of the jobs that I’ve performed and it was clear to me that the polished floor was going to fit nicely into what they were going to build,” McCool says. “But more importantly, choosing the polished floor saved the owners over $1 million dollars on the initial budget.”
The owners chose solvent-based concrete dye colors, matched to the owner’s selections by Ameripolish. 53,998 square feet of concrete received a natural polish meaning no dye was used, while 39,913 square feet was dyed using Repose Gray and 13,589 square feet was dyed in Barcelona Beige.
Another challenge to the contractor was the slab for the floor was to be placed before the steel framework of the building was constructed. Therefore the slabs needed to be protected throughout the construction process.
“Because the slab was to be polished, we didn’t want any damage to occur. We used a floor protection system from Skudo Floor Protection Systems and it was as good as it gets to protect the slab. Crews that came after the placement of the slab were driving lifts and building the shell of the building. Once the building was complete, we pulled up the protective covering and it was time for us to come in and polish the concrete.”
McCool offers a hat-tip to Lithko Concrete of Cincinnati, Ohio who placed and finished the slab. “They did an excellent job and it’s been a long time since we polished floors that good.”
A Maintenance Advantage
When speaking with his clients, McGovern says the maintenance advantage of polished concrete floors is a huge selling point.
“The one aspect of ceramic tiles that always fails first are the grout joints. The only way to save the floor is to fill the grouting joints and treat them with five to seven coats of sealant. Daily maintenance with a cleaning machine will wear off the sealant at the joint. The grout joint will take on dirt, dust and debris and it will be visible,” McGovern explains.
Working as a team with McGovern, McCool reached out to the maintenance team at the Liberty Center to inform and educate them about how to maintain the floor once it was completed. For assistance, he also recruited his supplier, SASE Company Inc., who took the lead to work with their team and gave them everything they needed to maintain the floors.
“I tell all of our clients, there is maintenance required for a polished concrete floor, it is not maintenance free,” McCool says. “But, it’s a lot less maintenance than any other flooring system such as carpet, ceramic tile or VCT.”
McGovern says the beauty of polished concrete floors is simple: “We can go to the Liberty Center in 2035 and that floor will look the same as it did the day the mall opened to the public in October 2015. And that’s an awesome selling point when pitching polished concrete floors to prospective clients.”