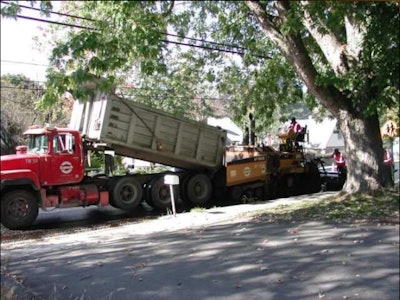
We’re curious just how many pavement preservation treatment acronyms there are for all the different ways we extend the life of a pavement. One we heard recently was PPEST. Given that it sounded something more likely to be found in the extermination industry and not the asphalt industry, we looked in to it.
“Paver Placed Elastomeric Surface Treatment or PPEST is a preventive maintenance pavement treatment that provides a sealed, smooth, durable, long lasting, thin, flexible hot mix pavement that extends the road’s service life delaying the need for more costly reconstruction efforts,” says Charles St. Martin, acting chief of public affairs for the Rhode Island Department of Transportation (RIDOT).
St. Martin explains that Paver Placed Elastomeric Surface Treatment is really just a long name for a polymer/rubber modified thin overlay placed at 1-inch thick. Produced in a conventional hot mix plant, PPEST is a mixture of coarse-graded 3/8-inch crushed aggregate and a chemically modified crumb rubber (CMCR) asphalt binder. The binder is PG 70-40 and contains a minimum 5% CMCR. The mix has a binder content of 6.0 to 7.5%.
This surface treatment however is gap graded, as opposed to the usual dense graded HMA. “This allows more room in the aggregate structure for the highly modified binder that we use,” St. Martin says.
PPEST Placement
PPEST is recommended for use on roadways with moderate cracking of any form (fatigue or thermal), except those with reflective cracking. It can also be used on roadways with light rutting and cracks less than ¼-inch wide. However, if rutting is more than ¼-inch and the cracking is more severe, the rutted area should be leveled and the existing cracks should be sealed before PPEST is applied.
PPEST HMA is applied directly to a tack-coated surface, placed to a 1-inch compacted thickness. A tack coat is needed between the existing surface and the new layer to ensure adequate bonding.
As opposed to some surface treatment options that require special equipment, microsurfacing for example, PPEST can be installed using conventional paving equipment that you use to place hot mix asphalt; a hauling truck, a hot mix paver and a steel drum roller.
“RIDOT wanted to develop a preventive maintenance treatment that could be placed by conventional paving methods in urban localities, PPEST is that method,” St. Martin says.
Because it is thin and highly modified, it can be difficult to place by hand, St. Martin says.
“PPEST can be difficult to place by hand and rolling must take place immediately since it cools quickly,” he adds.
However, since PPEST has a thick asphalt film and highly modified binder, it is very resistant to cracking. St. Martin says PPEST does costs more per ton than conventional HMA, approximately $86,280 per lane mile, but since it is placed thin, the cost to pave a road is approximately the same. The mix is designed to last 10-12 years.
RIDOT’s Mission
Since 1995, RIDOT and their Highway Assessment Committee (HAC) have been researching ways to extend the life of their roads. The committee incorporates members from various engineering divisions in RIDOT. The team focuses on five year old roads to determine the impact of design and construction practice on highway maintenance.
In 1998, the HAC turned their focus to researching a pavement preservation program. They started with researching cracksealing initiatives on their roadways and then began incorporating preventative maintenance surface treatments with experimental test sections in following years.
RIDOT began using PPEST in 2001, the first project was worth $1 million. In 2015, RIDOT paved eight roads using this surface treatment for a total of 6.1 miles, totaling $2.2 million.
St. Martin says that many other states have also used this application or are looking in to it. Has your state used this? What are some other pavement preservation treatments that are working in your area? Let us know at [email protected].