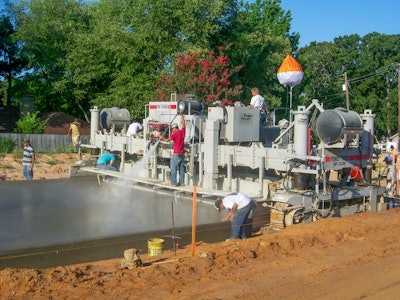
The “paving environment” has become more challenged in recent years. “The days of pointing a paver in a direction and paving continuously for 20 miles are gone,” says Tim Nash, director, Concrete Products, Wirtgen America. “Jobs are cut up into segments, which require frequent mobilization, with constantly changing paving widths... Tolerances are tighter and larger sums of bonus pay and/or grinding costs are now central to bids.”
To address today’s more complex project requirements, paving contractors are turning to the latest concrete paver solutions. “Contractors getting the work want the latest technology,” says Kevin Klein, vice president of Engineering/Research & Development, GOMACO, “and they have to work smarter to make a profit.”
“Technology in paving equipment is no longer a dirty word,” adds Nash. “It’s a requirement.”
Modern slipform pavers incorporate “smart” features that enhance both functionality and flexibility. “Project owners have been increasingly shortening construction times and narrowing construction sites,” says David Lipari, marketing manager, Guntert & Zimmerman. “Without these features, these challenges would be insurmountable by both build costs and requirements.”
Advances in Controls
Advances in control systems are at the heart of “smart pavers.”
“With the advancement of computers, the controls on machines and pavers are no exceptions,” says Randy Peters, Power Pavers division of Power Curbers. “The days of manual controls are over. The new generation [of operators] wants to see buttons or joysticks to control their machines.”
This is achieved through the Controller Area Network (CAN) system — the “brains” that enable programmed controllers to read and manage all paver functions. “The information is instantaneous and the reaction time of the controls is just as fast,” says Peters. “These features allow contractors and operators to do things much faster.”
Take the transition from pave mode to transport mode. “With the push of a button, all four tracks on a paver will automatically turn 90° and align themselves to be able to drive onto a truck. With the aid of sensors, the control system on the machine knows exactly where the track is and can turn all four to the same degree,” says Peters. “This saves the operator from trying to line up the tracks individually, hoping they are aligned so it does not stress the frame. He can just go with the confidence that everything is aligned.”
Smart pavers are both quicker to respond and easier to use. “Our new pavers are getting smarter for simplicity,” says Klein. “The paver of today has to work with 3D guidance and smart accessories like transition adjusters, flying shoulders and bar inserts. A smart paver provides accuracy in all of its functions and is user friendly and simple to operate.”
3D Technology Simplifies Concrete Paving Operations
It is also capable of managing multiple functions simultaneously. For example, the G+ intelligent control system used on GOMACO’s new GP3 paver can make adjustments to the speed of a single track and the radial configurations in steering as the paver width is changed.
“We’ve designed the paver to make quicker and easier physical changes with fewer or no changes in the controls setup,” says Klein. “The GP3 is an intelligent paver, so it is programmed to do many functions smoother and better without the operator giving it any thought or attention.”
The GP3 gets its intelligence from the G+ control system. “Because the G+ control system is designed in-house, we can continuously build into it specific smart functions for concrete paving,” says Klein.
[Video] GOMACO GP3 Smart Paver
Faster Width Changes
Smart features are intended to help contractors quickly and cost-effectively complete jobs while maintaining ever-tighter project specs.
“Simply stated, it’s in the interest of manufacturers to stay in front of technology to assure that our users are able to execute jobs with a favorable competitive posture,” says Nash. “It’s about providing tools for contractors that allow them improved rideability, decreased operating costs and increased production.”
To that end, Wirtgen offers such smart paver features as:
- hydraulic frame telescoping for quicker width changes
- mainline paving molds to enable minor paving width changes in hours vs. days
- worm gear drive track steering, which permits 90° track turning capability
- smart steer control features that permit optimized jobsite maneuvering, more precise turning capability and less wear on the legs and frame
- push-button counter-rotation, which enables a four-track paver to turn 360° within its own dimensions
- hydraulic leg swing to aid in transitioning from paving to transport quickly and with less effort
- major attachments such as the Super Smoother that can transport still attached to the main frame, maintaining an under 12-ft. transport width
“[Such features] result in decreased transport times, decreased setup times and decreased paving width change times,” says Nash, “not to mention improved paver control system accuracy.”
The emphasis for many paver manufacturers is on simplifying paver width changes to reduce the time it takes. For example, GOMACO’s GP3 incorporates Smart Width, which enables easy, accurate widening setup, as well as a reference for the G+ system to maintain proper steering and track speeds at varying paver widths. Changing the main frame width is accomplished with the roller frame and double parallel, hydraulically telescoping tubes in the front and rear frame for dual telescoping capability.
“The GP3 can telescope up to 7 ft. on each side of the frame for a total of 14 ft. of automatic frame widening,” says Klein. “Smart hydraulic cylinders provide the telescopic stroke in the frame widening and also an automatic reference of the paver’s width to the G+ controls.”
Pivot arms for the tracks utilize sensored, hydraulic rotational swing (Smart Pivots) to provide the G+ with information on the degree of swing. This enables the control system to maintain the tracks in the straight-ahead line and for steering.
Such use of sensors in four-track pavers provides the ability to monitor and manage more functions. In the case of swing arm cylinders, Peters notes, they are typically used to indicate the position of the arms, each of which can be moved individually or can be positioned to the same degree, with position information then displayed on the control screen. “The operator doesn’t need to leave the console to put the arms where he needs them to be,” he explains.
The time and cost savings can be substantial. “With previous generations of four-track pavers, it would take several people to manually move the arms, and then the crew would have to take measurements to make sure the arms were in the same position,” Peters points out.
The GP3 also takes advantage of sensors on its hydraulic rotational drives for track steering and rotation. “Smart Track Rotation provides the G+ controls with exact track location and position,” says Klein. “Extreme steering is now possible, with the tracks having the ability to rotate further than ever before.”
Smart Pivots and Smart Track Rotation enable the control system to automatically maintain travel direction of the tracks, regardless if the frame is in paving, transverse or travel mode.
“All of this provides for easier width changes and accurate steering controls for changing paving widths and travel modes,” says Klein.
Guntert & Zimmerman has also introduced features designed to speed paver adjustment. For example, TeleEnd was developed to reduce the time it takes to change the width of the paving kit — the mold under the machine that makes the slab.
Traditionally, such adjustments have been a time-intensive task. “Contractors can spend up to two days changing width and may require the need of a crane,” Lipari notes. “With TeleEnd, a contractor can change widths in an hour with one or two people.”
VariWidth speeds tractor width adjustment. “No bolts, no cranes, just a flip of the switch,” says Lipari, “and a contractor can change the tractor width.”
[VIDEO] Features of Guntert & Zimmerman's S400 Concrete Paver
Maneuverability is another function being addressed. “With jobs being cut up and paver jumps being more common, contractors need a highly maneuverable piece of machinery,” says Lipari. “[AccuSteer and SmartLeg] give them that versatility. They also allow a contractor to change the leg angle during paving on-the-fly to allow the contractor to maneuver around a light box, fire hydrant, etc. This saves valuable time.
“All of these features are aimed at making contractors more productive, and allowing for quick width changes without sacrificing smoothness of the concrete,” he adds.
Evaluate the Advantages
Though increasingly essential on many concrete paving projects, not every contractor wants or needs smart features. As such, not all manufacturers offer them as standard.
“Some will create a base machine with less of these features and then provide them as options,” says Peters. “At Power Pavers, we try to supply the features that we know the customer will want and need for their jobs as part of our standard machine... but if they want a little more ‘wow factor’ or extra control, we have some of those more advanced options.”
Cost is often a factor. “The cost of the machines is always dependent on how many features you want, so the more features and technology, the higher the price,” says Peters. “Comparing the machines from 20 to 30 years ago, the cost of the modern ‘smart’ paver has increased because of the technology and design time invested.”
Yet, the advantages are hard to ignore. “The benefit of these machines is that it is easier to learn to operate the machine and more things can be controlled from the operator station. With the push of a button or turn of a dial, you can control every feature of your paver,” says Peters. “This means the operator can respond quicker to issues and not have to climb off and on the machine to make changes.”
Lipari agrees that some contractors still prefer a base machine. But perception can change once they recognize the potential. “[Smart features] can increase the cost of the machine,” he acknowledges. “But with a few moments of explanation, contractors come to see that they can recoup the costs quickly.”
“It all comes down to what you need to do and how much effort are you willing to invest to get the job done well,” says Peters. “If investing in a modern machine will make the job easier and provide consistent results, then that will outweigh the increased cost.”