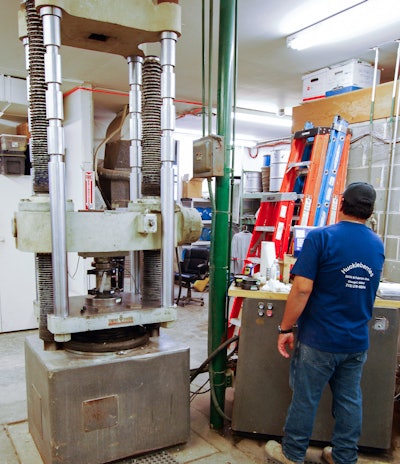
When the new Wanda Vista Towers building is completed in Chicago it will be 1,140 feet tall with 95 floors. The footprint of the building will be approximately 350 by 150 feet and will feature a hotel on the first 11 floors with condos occupying the floors above. An unusual aspect of the structure is that floor plate sizes change with each floor, the smallest being 82 feet square and the largest being 92 feet. Additionally, most of the columns will not be aligned from the bottom floor to the top floor. The core of the structure—where elevators, emergency stairs, and utilities are encased by concrete walls—will be engineered to provide primary strength for the structure and minimize building sway due to the wind. For the concrete mix used in the core, the modulus of elasticity (also referred to as Young’s modulus or the letter “E” or “MOE”) is a more important consideration than the compressive strength. Here’s why.
What is modulus of elasticity?
Increasingly, engineers are specifying MOE requirements for concrete for super-tall buildings, bridge piers, and other structural applications where the stiffness of the material is of central concern. For this type concrete there is a relationship between high MOE and high compressive strength but the stiffness or the deflection of concrete—its resistance to bending—is more important than its compressive strength, a measure of hardness or brittleness. In simplest terms the modulus of elasticity is a number representing the stiffness of a material. In the U.S. the number is measured in pounds per square inch (psi) or thousands of pounds per square inch (ksi). ASTM defines MOE as the graphed slope of a cylinders length change when compression up to 40 percent is added to the cylinder. For example, if a 7,000 ksi MOE concrete shortens a 1-inch specimen by 0.001 inches when a load of 7,000 psi is imposed, and a 3,500 ksi MOE concrete would shorten twice as much with a 7,000 psi compression. For a super-tall building this difference could cause dramatic differences in wind sway.
The effect of mix ingredients
As a composite material all the ingredients in concrete affect its MOE and the task of creating a mix that meets the specified requirements involves researching materials and testing. This process often starts a year or more before construction actually begins.
Kevin MacDonald, president of Beton Consulting Engineers, Mendota Heights, Minnesota, says the large aggregate in concrete is an important first consideration because its MOE is usually higher than cement paste. “Crushed limestone, though plentiful around the country, is often too soft so “trap rock,” basalt or other fine-grained igneous rock, is the more usual choice.” The MOE of trap rock can be as high as 17,000 to 18,000 ksi but how it is mined is also important. Granite, composed of mica, feldspar and quartz, can sometimes be used if the mica content is low. Iron aggregate would have the strength needed but it’s too dense and heavy, structures would have to be significantly increased to carry the load, likely negating the benefits of increased stiffness. Whatever choice is made, rock for this kind of concrete is always crushed.
The MOE of both cement paste and large aggregate is all-important. Cement paste must be present in the right amount in order to achieve proper bond to aggregates and along with the compressive strength of concrete, the proper water-cement ratio becomes a critical element. Other ingredients in concrete can include pozzolans such as fly-ash, silica fume, slag, and admixtures including high range water reducers (super plasticizers), viscosity modifying, and shrinkage compensation admixtures—all can play an important part.
To determine what the MOE is for concrete either, six by 12 or four by eight inch concrete cylinders are cast and cured underwater in a curing tank. Then they are placed in the same machine used for determining compressive strength. Force is applied to the sample to compress it, changing its length and causing the cylinder to bulge at its diameter. This change in length and width is measured and entered into the formula for MOE along with the force applied.
Designing the mix
“The best high MOE concrete is the mix with the least space between large and small aggregates,” says MacDonald. Often referred to as “well-graded”, you start with the largest aggregate size and then add the right amount of next-size smaller to fill the void spaces between the larger stones. This “particle packing” process continues down to the small aggregate sizes and can even include using secondary cementitious materials (SCM) such as fly ash, slab, or silica fume of different particle sizes. The goal is to use the least amount of cement possible to coat aggregates and bind them together.
These mixes are almost always pumped so they must be able to flow through a pipeline and be placeable. In order for this to happen MacDonald says he calculates the optimal amount of cementitious material and adds five percent extra paste to serve as a lubricant for the concrete and facilitate good placement.
Central mix concrete plants are the best way to batch these kinds of mixes.
Testing for MOE
Flood Testing Laboratories located in Chicago, Illinois is one of four accredited testing companies in the Chicago area to do MOE testing. Their principal engineer, Walter Flood, says they have been running tests for the Wanda Vista project for the past year. The testing protocol for MOE testing is defined in ASTM C469.
Testing starts with four-inch diameter, eight-inch long cylinders taken from the quarry that produces the proposed aggregate and tested for the project. Sometimes there are defects in the rock that aren’t observable so multiple cores are tested. Trial mixes are constructed based on this information.
Flood says that most of the MOE testing they perform is for ready-mix producers for development but they are also hired by owners to do testing during production placement. Trial batches are created and tested from mix designs that companies submit to them for testing. These batches are created in the lab, cast into cylinders and cured. Compressive strength and MOE testing are then performed. One set of cylinders is placed in a concrete compression testing machine and tested for compressive strength. When this strength is known another cylinder is taken from the curing tank and fastened into a cage with pins to the specimen to measure deflection. Then it’s placed into the same testing machine and stressed to a known force and the amount of deflection in the length of the cylinder is noted. The test only takes about 15 minutes to run and Flood says they typically run the tests at 28 days and at 56 days, though occasionally 90 and 180 day properties are confirmed.–MOE increases with time but not quite the same as compressive strength. Flood adds that MOE testing is performed on four- by eight-inch cylinders mostly due to capacity limitations in breaking six-inch specimens at 15,000+ psi. Testing is currently under way in cooperation with ASTM to determine whether test results on six- by 12-inch cylinders report the same data.
In the process of deciding what mix will be the best on to use for a project such as Wanda Vista, several hundred mixes might be tested.
Flood says transportation and pumping are important issues too. So self-consolidating concrete (SCC) mixes are often used for super-tall buildings because they must be pumped a thousand or more feet straight up before placement. Spread measurements of approximately 27-inches are needed and admixtures are used to achieve this. Without admixtures these concrete mixes can be difficult to place or shovel.
What Wanda Vista wants
David Fields, Senior Principal for Magnusson Klemencic Associates (MKA), Seattle, Washington, is the project manager for the Wanda Vista project. His firm is the engineer of record and is responsible for specifying the concrete requirements for the concrete. He says their specification for the concrete in the core structure is 12,000 psi with a MOE requirement of 7,000 ksi. “All tall buildings fall within this range. Increasing concrete strength by 10 percent can bring about ready-mix cost increases as much as 100 percent,” he says. Some specifications require minimum values, meaning that MOE can’t go below the target value, so MKA decided to specify “average values,” meaning that an occasional load of concrete could fall below the specification by as much as 300 ksi without being harmful to the structure. Their hope is that this change would make it possible for ready-mix producers to provide better pricing.
A key benefit for high MOE concrete is that buildings will sway less in high wind events, building occupants don’t like being in structures that sway very much. With this concrete the Wanda Vista building is projected to sway a maximum of approximately 2.3-feet each way at the roofline for a wind with a 10-year return period.
Fields estimates that 123,000 cubic yards of concrete will be needed for the construction of the building, about 40 percent of which will have a high MOE requirement.