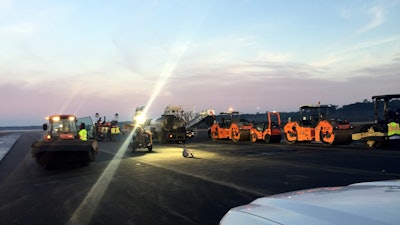
When visitors come to Marine Corps Air Station (MCAS) Cherry Point, they’re likely to forge lasting memories of roaring jet engines and pilots taking off in some of the world’s fastest aircrafts.
Commissioned in 1942, MCAS is an airfield located in Havelock, NC, which has been a source of pride for local residents and Marines from around the globe for more than 70 years. It is currently home to the 2nd Marine Aircraft Wing, who conducts various air operations in support of the Marine Forces.
In accordance with its mission to provide the highest quality operating environment, MCAS trusted S.T. Wooten to repave two important runways, 23R and 15L, to safeguard the nation’s airmen and its aircrafts.
The project began on June 6, 2015, and was completed a little over a year later on July 21, 2016.
Project objectives & preparation
The existing pavement on the runways was extremely oxidized with both transverse and longitudinal cracking.
The contract for the project called on S.T. Wooten to produce smooth pavement and joint transitions across the runways while exceeding the required percentage of compaction. The treatment and processes for the pavement repairs were also named in the contract.
“A number of best practices and innovative methods were used to ensure the project exceeded MCAS’s expectations,” says Chris Croom, division manager of asphalt materials and quality control at S. T. Wooten. “These included the pavement milled to grade, cracks sealed, and leveling performed prior to paving the surface mix.”
To prepare for paving, S.T. Wooten used robotic total station technology with the milling machine to ensure the runways were cut to grade requirements on the project. This technology uses an electronic (transit) system integrated with an electronic distance meter (EDM) to read slope distances from the instrument to a particular point.
“Providing the capability to precisely control the instrument from a distance via remote control, the total stations helped our operators increase efficiency on the project,” says Croom.
Mix design challenges
The mix designs for Runways 23R and 14L were specified by the government using U.S. Army Corps of Engineers standards for hot mix asphalt (HMA) airfield paving. There were two mixes applied: HMA surface and HMA leveling.
One two-inch-thick layer of HMA surface mix combined with HMA leveling of variable thicknesses was placed on this project, with a total of 55,110 tons of asphalt placed.
“These mixes were intended to give MCAS Cherry Point Airfield a long service life under variable conditions and the ability to handle load from military aircrafts,” says Croom.
A portion of the project was paved in colder weather, during the winter months, so S.T. Wooten used an anti-strip warm mix additive called Evotherm M1-3G, produced by Ingevity, which helped with mix compaction in cooler temperatures.
A 2015 Caterpillar AP1000F paver with a vibratory screed was used to pave both runways. The maximum screed width used was 18.4 feet. S.T. Wooten also used a Roadtec SB-2500 material transfer vehicle (MTV).
Two 2015 Hamm HD 120 IVVHF steel wheel rollers and one 2015 Hamm HD VT steel/pneumatic combo roller were also used to help achieve desired density.
New tech helps overcome challenges
“The challenge with this project centered on the balance of achieving multiple specifications, producing smooth pavement and joint transitions across the runways while also ensuring the project surpassed the required percentage of compaction on the mat and the longitudinal joints,” says Croom.
“To accomplish this, we implemented a cohesive strategy to ensure that not only were the customer’s needs met, but their expectations were exceeded,” he says. “We incorporated a Willow Designs wedge device, with vibration, to shape and compact the edge of the mat to an angle of about 30 degrees. Tack was applied to the joint prior to placing the adjacent lane of asphalt, and an Asphalt Reheat Systems infra-red joint heater was used to heat the longitudinal joints as the next lane was being placed. A Hamm combo roller was used primarily on the longitudinal joint.”
The joint heater and wedge devices were two innovative solutions used on this project. “We used a Roadtec SB-2500 MTV to produce a smooth pavement without mix or temperature segregation, and to reduce the potential pickup of foreign object debris (FOD) by not having trucks on the tacked surface,” says Croom. “FOD can be picked up by jet engines and result in significant damage.”
S.T. Wooten also used non-tracking tack supplied by SEACO Emulsions Inc., to further help address the concern for FOD which could have been created by the haul trucks or the paving equipment. A broom tractor and sweeper truck were also used nonstop to mitigate FOD and ensure a quality finished product.
Other innovative equipment utilized included:
- A Road Dryer 1200 used to dry the milled surface after a rain, to keep paving as continuous as possible
- A portable asphalt plant onsite to help facilitate efficient hauling of the mix to the paver and improve mix temperature retention
- Light plants to continue paving into the night and start earlier in the mornings to limit the number of transverse joints on the project
“With this combination of best practices and innovative equipment, we were able to ensure both smooth pavement and smooth joint transitions, in addition to achieving the required densities.”
Lessons learned
Croom says S.T. Wooten learned that the paving techniques used on this project gave the company the best opportunity for successful paving on similar applications in the future.
“It will help us continue to build on the innovations that we implement for our customers, helping set ourselves apart and get the job done better,” he says.
And as always, communication and coordination between S.T. Wooten and the Naval Facilities Engineering Command was crucial to the success of this project.
Says Croom, “This project was a great example of how S.T. Wooten strives to investigate and utilize innovative paving technologies and techniques in order to accomplish our project goals while ensuring we construct high quality pavement.”