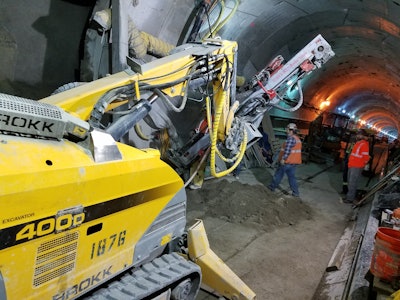
Seattle-area voters, tired of long commute times, approved a project to relieve one of the area’s most congested traffic areas by connecting the Northgate, Roosevelt and University District neighborhoods to existing routes, including downtown Seattle and SeaTac airport. The transit lines will join 36 miles of new and under construction light rail lines running north, east and south from Seattle. Completion will mean just a 14-minute ride from Northgate to downtown for an extra 60,000 passengers by 2030.
But while passengers will eventually benefit from quicker commute times, there’s no fast way to add more than four miles of track, most of it underground, to the Sound Transit Link Light Rail system. That was the challenge a joint venture of several tunneling contractors faced when starting its portion of the $1.9 billion Northgate Link Extension in 2013, and which continues to keep them busy three years later.
Sound Transit dedicated more than a quarter of the project’s $440 million estimated expense to general contractor JCM Northlink LLC to handle the tunnel segment. JCM is a joint venture formed in 2013 between Jay Dee Contractors of Livonia, MI, Frank Coluccio Construction of Seattle and Michels Corporation of Brownsville, WI. The contractors regularly collaborate on large-scale projects and brought experience working on a different section of the extension they completed in 2013.
JCM project leaders knew immediately that the schedule would be demanding. They had to work around the clock six days a week to meet deadlines. The extension runs through highly populated areas, meaning contractors had to follow strict city noise restrictions between 10 p.m. and 7 a.m. Plus, supervisors needed to manage the scheduling of nearly 250 employees to keep work running smoothly.
“We had eight different operations and four different subcontractors trying to work in one tunnel,” says Chris Wood, JCM site project superintendent. “It’s important that we keep work linear. That’s the biggest challenge – keeping a path in and out so you can pour concrete, keep electricians and carpenters going, and accomplish everything else.”
Project planners also realized they wouldn’t be able to use the same equipment they had in the past for tunneling projects. The tunnels would run directly below the University of Washington, which has longstanding, ongoing sensitive science projects. The train and tracks JCM used for past projects to transport crews and supplies through tunnels are loud and produce significant vibrations, which would have disrupted the experiments.
To lower noise levels throughout the tunnel and to avoid disturbing the university, project leaders incorporated new sound abatement methods. JCM brought in seven Metalliance rubber-tired vehicles that stretched 52 ft. long but were just 6 ft. wide and could handle 45 tons. Crews could use them as an alternative to a locomotive on rail for transportation in and out of the tunnel. In addition, the vehicles work with a number of attachments, including high-car platforms and concrete distribution attachments, reducing the need for additional equipment.
More Innovative Equipment Solutions Required
Crews started the tunneling portion of the project by digging two large vertical shafts and a tunnel portal to initially be used as access points for tunnel boring machines (TBMs), service work, material removal and supplies. The shafts will be converted to light rail stations when the project is complete. JCM used a Kroll 15000 tower crane with 108,000 lbs. of lifting capacity to lift stacks of tunnel liner segments, equipment and material in and out of the 100-ft.-deep shafts.
Once shaft construction was well underway, JCM began digging the twin-bore tunnels from Northgate to the already excavated University of Washington station and existing light rail track. Crews used Hitachi Zosen (Hitz) and Robbins TBMs to simultaneously dig two parallel 21-ft.-diameter tunnels. The machines stretch about 400 ft. long and advanced an average of 30 to 50 ft. a day.
The tough soil didn’t make the job easy. The TBMs hit harder ground than anticipated, slowing down the machines as cutters and scrapers heads wore down or broke against cobbles and boulders.
A Safer Option for Cross Passages
As tunneling moved along, crews started digging 23 cross passages between the tunnels. The 16- to 20-ft.-long openings house electrical rooms and serve as safe havens and escape routes for train passengers in case of an emergency.
Cross passages are typically constructed using pneumatic tools and mini-excavators, but about five years ago, JCM began using a different approach on another section of the light rail expansion: Brokk remote-controlled demolition machines. They made the switch to limit worker exposure to harsh tunnel environments and reduce the inevitable fatigue and potential injuries that come with using handheld tools all day. The remote-controlled technology also allows workers to operate the units from a safe distance, minimizing exposure to falling debris.
JCM owned a Brokk 260 from an earlier project, but with the increased demands and tight deadlines of the Northgate project, they decided to invest in two larger Brokk 400Ds and rented another in order to maximize productivity. The equipment’s efficiency and precision sped up the excavation portion to less than three weeks, shaving off more than a week of work compared to handheld tools. In addition, the machines held up well in tough tunneling conditions.
“I tell everybody that anything that goes down into that tunnel will get broken. I can give these guys a glass of water and somehow they’ll break the water,” Wood states. “But the Brokk remote-controlled machines withstand the conditions. When we do have issues, Brokk field mechanics work with our mechanics to limit detrimental downtime by bringing in parts and fixing the unit right away.”
JCM worked on multiple cross passages at a time. Crews typically started the passages by pairing the 400D with a TEI 350 rock drill attachment drilling 4-in.-diameter holes for well points and 20-ft. steel spiles. These were installed about every foot to create a canopy to secure the ground and protect workers from falling debris.
Once the spile canopy was completed, JCM needed the maneuverability and compact size of the Brokk 260 paired with an Atlas Copco SB 302 hydraulic breaker to break through the tunnel wall. After getting through the concrete, JCM brought back the 400D to complete the passage, often alternating between an Atlas Copco SB 552 hammer to break through the ground and a Simex road header to mill the walls.
Workers used mini-excavators to remove material and load it into dump trucks, and crews coated the walls with shotcrete to keep them in place. Each passage took seven to nine weeks to complete, including waterproofing, installing rebar, pouring the invert and headwalls, and finalizing 90 to 110 yds. of fiber-reinforced concrete.
Putting a Freeze on Groundwater
Staying true to its “Rain City” nickname, Seattle gave JCM much more groundwater than expected, causing complications. The TBMs had earth pressure balance systems that pushed water away, allowing technicians to do inspections and service cutter heads, but the cross passages weren’t as easy. The water volumes that needed to be pumped at some of the cross passages was far greater than what the municipal system could handle.
Project leaders knew freezing the soil was a solution that would prevent structural issues and ensure safety during excavation. They originally planned to freeze five of the cross passages but expanded that to 10 after encountering the excess water. Crews again used the Brokk 400D, this time to drill holes for freeze pipe they installed within the haunches of the cross passages. They then pumped the pipes with a brine solution, chilling the soil to a frozen 10 degrees F and making it an easy target for a Brokk machine’s hydraulic breaker.
“The freezing technique is invaluable to keeping work going quickly and safely,” Wood says. “It is very effective. The frozen sand ends up being like concrete until it thaws. This makes it really easy to chip away at without worrying about stability issues.”
The Final Breakthrough
After three years of tunneling with the TBMs, JCM completed the final breakthrough on September 1, 2016. Once the cross passages are completed, likely by March 2017, the crews will have removed about 725,000 cu. yds. of material — enough to fill about 242 Olympic-sized swimming pools. JCM will continue follow-up work until February 2018. The next contractors will continue work on the stations, rail and electrical components in preparation for project completion in 2021.
The transit plan approved by voters in 2013 also included an 8.5-mile above-ground light rail extension from Northgate to Lynnwood. Project construction is expected to begin in 2018 with a goal of service starting in 2023. Another expansion including 62 miles of new light rail and other transit additions was approved in November 2016. The project is just one of a series of planned improvements, all part of an overall goal to relieve commuter headaches.