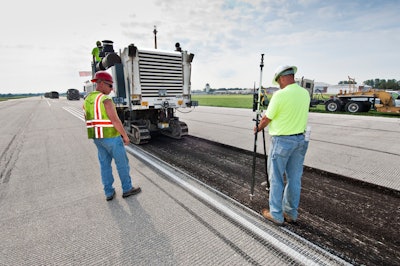
The advent of 3D milling is not new. The technology has been around since about 2009, and while 3D milling may be more prevalent on airport runway jobs than mainline highway paving jobs here in the U.S., its popularity is increasing.
“We sold more 3D units in 2016 than in 2013 and 2014 combined,” says Kevin Garcia, business area manager for paving and specialty construction in Trimble’s Civil Engineering and Construction Division. “We’re starting to see some states leaning toward including it in specs.”
For example, Oregon’s DOT is implementing 3D milling throughout the state. The agency will provide contractors the data necessary for 3D milling in order to benefit projects with tight constraints or high material costs.
Also known as Automated Machine Guidance (AMG), 3D milling is a system where milling machines are equipped with computer technology that controls the vertical position of the milling rotors. 3D milling equipment can adjust elevation and slope based upon data sent from a total station, removing the need for extensive labor associated with surveyors placing stakes and equipment operators continually adjusting for variable mill depths.
Garcia says early adopters of the technology in California, Texas, and North Carolina are seeing tangible benefits to smoothness and material management.
Advantages
3D milling systems allow operators to produce the correct profile for a road without using external, on-site grade references, such as stringline, which can be flawed. A stringline system is only as accurate as the surveyor who sets each pin. It can get hit. It can blow in the wind. Workers will try to step over it and kick it by accident, and then walk away without telling anybody.
With 3D milling, the machine will follow the design rather than a potentially flawed reference.
Stringline also limits use of multiple milling machines. "If you’re running one milling machine, you could set up stringline," says Garcia. "But if you’re running three milling machines on a project, you can't do it. It makes logistics very difficult. Anytime you work in echelon it makes string hard to maneuver and navigate trucks around."
Multiple milling machines can work at the same time using AMG, however.
3D systems are also capable of reproducing roadway grades and slopes within millimeters of an engineer’s specified tolerances, which goes a long way toward improving smoothness.
“It’s actually much easier to create that smooth surface with the mill, and go out with the paver and lay a fixed thickness of asphalt,” says Garcia. “It’s very easy on that surface to create a nice, smooth lift of asphalt."
Trying to smooth out a waved surface with a paver is difficult. You may lay a smooth surface with the paver, but when you start rolling it, the asphalt will actually compact more above the low spots. Milling it smooth first prevents this problem and saves material.
3D milling can also help you mill more complex designs such as transitions and elevated curves. Imperfections in the existing surface do not affect the final product.
Using 3D technology does not copy existing topography. Because you’re using planned data that is optimized by engineers, any sort of waves or other uneven areas will be corrected regardless what the actual surface looks like.
“The technology allows precise redesign of roads, save material being placed and ensures design thickness, which is fundamental for long-term quality,” says Garcia.
Maximizing your yield is yet another advantage of using a 3D system. The surface prepared by a 3D-equipped milling machine is very accurate. With tight specs to meet, wasted material just takes away from the bottom line. Milling accurately helps you to pave accurately.
Limits
As with any technology, there are limitations. Typical limitations are machine speed, line of sight to the instrument or satellites, radio communication and the availability of design data. Also, if the milling machine is worn out or not maintained very well, or the material it’s supposed to cut is not good, even the best calibrated 3D system will not fix it.
Purchase price can be a hurdle. Typically, the biggest objection relates to the initial cost of the 3D system. Multiple machines on site can increase that initial cost.
Of course, the quality of the design data is critical. 3D control systems can place more emphasis on the engineers and surveyors when they do their jobs in the first place. The 'control points' on a jobsite are absolutely key to getting a good final result. If the surveyors are careless when they set out control points, accuracy of the machine control can suffer.
Also, it’s imperative for the engineer who is taking the digital design file and developing the machine control file to be used on the equipment to be accurate in the steps that he is taking. The milling machines are going to build exactly what the design file tells them to build, so if there are problems built into the design file, there will also be problems in the final results.