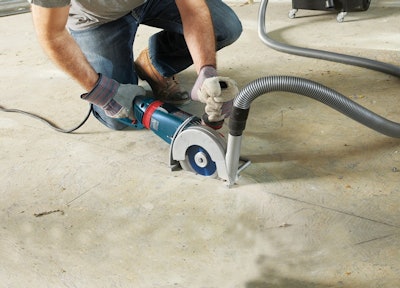
When it comes to cutting concrete, not all blades are created equal. Blades vary in the number of diamonds, size, shape, cost and performance, but it’s the application that’s the true differentiator. The questions can be numerous: Which blade will work best on what kind of concrete? How large should the blade be? Will the same blade used on a basement floor work well to cut two inches into a driveway? Are there new technologies I should know about and how do I keep up?
Basically, the answers fall into these categories: the hardness and abrasiveness of the material to be cut; speed, efficiency, longevity, size and affordability of the blade needed; and the quality of cut desired. Understanding the science behind the making of diamond blades, how they work and the kinds of blades available will help you choose an option with the right characteristics for your application.
The Science of Blade Making and How Blades Work
Concrete cutting blades are made with four basic components:
- The metal core: a precision-engineered steel disk with a rim that holds the diamonds
- Synthetic diamonds: the sharp cutting teeth that slice through the concrete
- The matrix: a metal bond that holds the diamonds in place until they wear away with use
- The weld: attaches the cutting segments (matrix and diamonds) to the core
It’s the exposed diamonds on the surface of the blade’s perimeter and in the radius that do the cutting, using a high-speed abrasive action. As the blade cuts, the matrix begins to wear away, releasing the worn diamonds and exposing new ones embedded within the matrix, which continue the cutting. Larger diamonds favor speed and smaller fine diamonds favor longer blade life.
The efficiency of the blade depends on the hardness of both the matrix and the concrete, and the number of diamonds embedded into the radius. The relationships work this way: When cutting soft concrete, a hard metal bond is needed so the diamonds can be fully used before being shed. When cutting hard concrete, which will wear down the diamonds more quickly, the bond should be soft to enable easier erosion of the matrix ensuring exposure of new diamonds.
Blade making is a science. There are a handful of companies that manufacture quality diamond blades. Part of the research process is experimentation with mixtures of diamonds and binder in a variety of concrete and masonry types.
Bosch is a leader in diamond blade development for concrete and masonry applications. By working with concrete and masonry contractors in the field, the Bosch team of engineers has been able to develop new diamond formulations. Through extensive testing, these chemical formulations and design changes have improved durability by reducing excessive blade wear and preventing segment cracking.
Types of Blades
Concrete cutting blades come in three variations: segmented, continuous and turbo. In addition, there are a variety of options for size and shape within these categories.
Segmented Blades, the most common option, are used for fast cutting in concrete. With segments of varying sizes around the perimeter, the gullets (gaps) between the segments disperse the dust, allowing the user to efficiently cut the concrete. The gullets also help to keep the blade cool. These blades are best for high production jobs where speed is paramount.
Continuous Rim Blades provide fast and clean cutting with minimum chipping at a reasonable cost and can be used on small- and large-diameter angle grinders. These blades cut more slowly and are used when precision is needed.
Turbo Blades combine the advantage of both continuous rim and segmented blades and can be used wet or dry. This type of blade can simulate the precision of continuous rim blades. They provide a good-quality cut at high speed and are used in many applications, such as cutting for repair work.
Criteria for Selecting the Right Blade: Longevity vs. Cost
Manufacturers offer diamond blades in a variety of quality and cost levels ranging from basic economy to premium. One difference is in the diamond content. While a user will notice the longevity between the various blade options. Upgrading may raise the cost 20 percent or more, but there will be significantly longer blade life. For small cutting jobs where the blade isn’t used to full capacity there’s more opportunity to use an economy blade.
But frequent-use users actually save money on a cost-per-cut basis with a premium blade. When cutting concrete it’s all about maximizing the cost of cut per inch or per foot. A little math can help you calculate the ROI on the blade. Just calculate the cost of the blade divided by the (length times width) of the cuts made.
Cutting hard concrete can shorten blade life and can reduce cutting speed. For a heavy job with an economy blade, a tradesman may have to change the blade daily. A premium blade could conceivably go a week on the same job. And fewer blade changes means a faster job, greater efficiency and better profit margin.
Concrete composition (aggregate): The content of concrete can be crushed (limestone, granite, sandstone) or uncrushed; fine (passes through a #4 sieve, .187" square opening) or coarse (what’s left). The amount of sand in the aggregate also affects the hardness and abrasiveness of the concrete.
Aggregates are geographically similar, with some variation. Florida has softer concrete while St. Louis’ is flint-based river gravel. Find an aggregate map of the United States to use as a general guide and select blades accordingly. Large and/or hard aggregates tend to cause blades to cut more slowly and are harder to cut, requiring a softer bond; small and/or soft aggregates cut faster and are easier to cut, i.e. require a harder metal bond.
Depth: The deeper the cut needed the bigger the blade required. Not all angle grinders can take all sizes, so consider the tool as well.
Age: Green concrete (0-8 hours old) requires a harder-bonded diamond blade than cured concrete (anything over eight hours), which requires a softer bond.
Compressive strength: Hardness of concrete is measured in pounds per square inch (PSI). Roads, sidewalks patios, parking lots and indoor concrete tend to range from soft to medium. Bridges, piers and nuclear power plants are some of the applications that are hard or very hard. The higher the compressive strength, the harder the material and the softer the bond required for cutting.
Steel content: Rebar or wire mesh in concrete will cause slower cutting rates, reducing the blade life.
Speed: Consider the horsepower and operation speed of the angle grinder being used. Blade manufacturers provide charts with recommended operation speeds and maximum safety speeds for their blades, which is often laser etched right on the blade.
Wet or dry: Make sure the blade can be used for the application needed. As a general rule, wet cutting is essentially an outdoor job due to the wetness around the saw; dry cutting is usually reserved for indoor jobs. So appropriate blade selection may require wet use, dry use or both. Never use a wet-use blade without cooling water or its life will be considerably shortened.
As a rule of thumb, rely on the product packaging from the manufacturer when buying a blade for a specific application. The best manufacturers of diamond blades help identify the right blade for the job with easy to-read size and color application photos on the package.
Meeting New Regulations
Every jobsite in America where concrete is cut, drilled or requires grinding changed on Mar. 24, 2016. That’s when the U.S. Department of Labor’s Occupational Safety and Health Administration (OSHA) ruling was announced that reduces worker exposure to respirable silica dust in an eight-hour period from 250 micrograms per cubic meter of air to 50 micrograms. After June 23, 2017, employers will be subject to OSHA review and penalty for non-compliance.
To meet the guidelines, every jobsite will require a dust management solution or provisions for wet cutting of concrete.