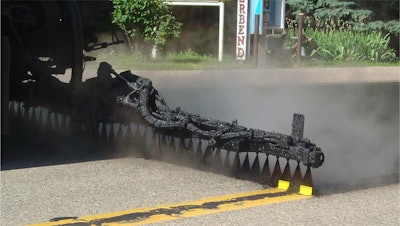
As new evidence of their usefulness unfolds, fresh attention is being paid to use of emulsified asphalt tack or bond coats in bituminous paving.
They’re commonly called “tack” coats, but as their purpose is to bond one layer of asphalt to another layer of pavement, industry is beginning to dub them “bond” coats. The same way that fragile, thin veneers of wood are glued to each other to form a robust sheet of plywood, research shows layers of asphalt pavement perform better when bonded to each other.
“An emulsified asphalt tack coat produces a strong adhesive bond without slippage between an existing pavement and a new overlay,” reports the Colorado Asphalt Pavement Association in its 2013 report, Best Practices for Applying Undiluted Emulsified Asphalt Tack Coats. But the performance of this adhesive bond can be endangered by poor placements.
- Underscoring this new attention to emulsified tack or bond coats was the recent release of National Cooperative Highway Research Council (NCHRP) Report 712, Optimization of Tack Coat for HMA Placement (for your copy, search “NCHRP Report 712”).
- In cooperation with the Federal Highway Administration, since January 2015, the Asphalt Institute has been presenting workshops on the rationale for and proper placement of bond coats. They’ve been conducted for state DOTs from coast to coast, and a summary presentation was conducted at the October Pavement Preservation & Recycling Alliance conference in Niagara Falls, Ont.
- In a widely distributed spring 2015 report, the National Center for Asphalt Technology (NCAT) reiterated the importance of bond coats, and the need for correct placement.
- New value-added bond coat products have come into the market which enhance performance, and reduce undesirable tracking of emulsion onto adjacent roadways, curb cuts, parking lots and sidewalks.
- Computerized distributor trucks – replacing the old driver-controlled tachometer-based systems – are taking the guesswork out of on-the-job emulsion placement. In the meantime, “spray pavers” – which apply bond coats immediately in front of the screed – are getting new attention for use for thin and ultrathin bonded overlays.
NCHRP sets stage
NCHRP 712 set the stage for the current excitement in emulsified asphalt tack or bond coats. This practical study – developed by the Louisiana Transportation Research Council (LTRC) of Louisiana State University for the Transportation Research Board – looks at the existing state of bond coat application, and sets out guidelines for best practice.
The study was developed by LTRC researchers Louay N. Mohammad, Mostafa A. Elseifi, Abraham Bae, and Nachiketa Patel; Joe Button of Texas A&M University; and consulting engineer Jim Scherocman. In the past, application of tack or bond coats mostly has been a “seat of the pants” operation, but this is changing, the report says.
“Selection of an optimum tack coat material and application rate are crucial in the development of proper bond strength between pavement layers, says NCHRP 712. “In general, selection of tack coats has been mainly based on experience, convenience, and empirical judgment. In addition, quality-control and quality-assurance testing of the tack coat construction process is rarely conducted, resulting in the possibility of unacceptable performance at the interface and even premature pavement failure.”
To this end, the report articulates optimum application methods, equipment type and calibration procedures, application rates, and asphalt binder materials for the application of bond coats, and recommends revisions to AASHTO methods and practices. A significant driver in this report is the development of two new devices for testing of bond coats, the Louisiana Tack Coat Quality Tester (LTCQT) and the Louisiana Interlayer Shear Strength Tester (LISST), the former for field use, and the latter for lab use.
The LTCQT evaluates the quality of the adhesive strength of bond coat on the job site, and adds a new dimension of quantification of field testing of bond coat applications. To complement this device, the LISST was developed for the characterization of interface shear strength of cylindrical specimens in the laboratory
“The LTCQT is a small test unit that can measure the bond strength of a tack coat in the field,” said Edward Harrigan, TRB staff officer. “The LISST is a test fixture fitted into a universal testing machine to measure the interface shear strength of a tack coat in a field or laboratory specimen. With the LISST, the effects of pavement surface types and conditions, tack coat material types, and tack coat application rates and methods on tack coat performance can be assessed.”
LTRC’s research for this project also resulted in the development of a training manual, presented as an appendix in the report. The training manual provides a comprehensive presentation of the recommended construction and testing procedures for tack coat materials.
Need for bond coats
The need for bond coats is clear, but their application is inconsistent and varies widely among both contractors and road agencies.
Some local road agencies don't provide detailed bond coat specs. In its own way, at least one DOT doesn’t require them on milled surfaces. If tack coats are not a contract pay item, their application may be at the mercy of the contractor, who might consider bond coats an additional expense that is not specified.
Nonetheless, best practices are established. For example, for maximum service, bond coats should be evenly distributed across the full width of clean pavement, not just as the commonly seen narrow spritzes on the substrate. Spray bar nozzles must overlap, ideally in multiples of three; triple overlap is recommended for higher application rates such as chip seal, but may not be achievable for lower rates of bond coats.
The emulsion must be dispersed with the right spray pattern, at the right temperature and volume. Long after the paving is completed, inadequate adhesion between two layers of bituminous mix may cause problems in the mat above.
“For the effect of tack coat coverage, the use of 50 percent coverage significantly reduced the interface shear strength by a factor ranging from 50 to 70 percent,” says NCHRP 712. “In addition, the use of 50 percent tack coat coverage resulted in inconsistent and non-uniform interface bonding behavior for tacked surfaces.”
“If [the overlay] can’t stick it’s not going to bond,” said consulting engineer Dale Decker, P.E., at a seminar on tack coats during World of Asphalt 2015 in Baltimore. “And if we don’t get the bond, we’re wasting our money.”
Moreover, from the owner and contractor point of view, this bonding of layers via asphalt emulsions comes at a relatively small price.
“An analysis of bid tabs using 2013 data shows that the cost of tack coat is relatively minor compared to other components of a typical paving project,” Decker said. “Therefore, the risk of a poor or a compromised bond from not applying tack should be deemed too great when one considers the ramifications of the loss of fatigue life from this condition. Tack is such a cheap component that it makes little sense to shortchange this critical step and introduce so much risk.”
As indicated, the possibility of skipping the bond coat arises with milled surfaces. “While some research indicates the skipping of tack on a milled surface will still result in adequate bonding of layers,” Decker said, “the weight of research indicates that the use of tack improves the bond of a milled surface that has been properly cleaned. As with the first scenario, the cost of tack is so small relative to the cost of premature pavement failure, it is foolhardy to skip applying tack.”
Do new pavements need tack coats? “NCHRP recommends applying tack coat always,” Decker said. “I don’t disagree with that. Tack coat is the cheapest insurance you can possibly buy as a contractor. It just makes a lot of sense.” The Asphalt Institute also recommends tacking between all lifts.
Types of bond coats
Bond coats utilize either straight liquid asphalt, cutback asphalt, or asphalt emulsions, but for a number of reasons, asphalt emulsions constitute the lion’s share of bond coat applications by far.
“The most widely used tack coat material in the world is emulsified asphalt,” NCHRP reports, adding emulsified asphalt, or asphalt emulsion, is a nonflammable liquid substance that is produced by combining asphalt and water with an emulsifying agent. A survey in the report indicated that worldwide, approximately 92 percent of tack coat applications utilized asphalt emulsions.
It’s easy to see why asphalt emulsions are preferred for bond coats. Straight or “neat” liquid asphalt must be kept heated to stay liquefied, and that poses burn hazards and other safety problems as the distributor moves around on the site.
Asphalt – what remains after lighter hydrocarbons have been distilled from the crude oil at a refinery – also may be liquefied by reintroducing some of those lighter hydrocarbons, such as kerosene or diesel, as a solvent. These “cutback” asphalts have been widely used in the past for tack coats, but today are discouraged because as the solvents evaporate, volatile organic hydrocarbons are released which contribute to smog and other environmental ills.
An asphalt emulsion is a homogeneous mixture of two insoluble substances, oil and water. In it particles of liquid asphalt (the dispersed phase) are surrounded by molecules of water (the continuous phase). Compared to hot liquid asphalt, asphalt emulsions have greatly reduced viscosity, are safe to use at lower temperatures, and allow liquid asphalt to be spread more evenly and thinly.
Emulsified asphalt is produced by dispersing tiny globules of asphalt cement into water treated with a small quantity of emulsifying agent. The dispersion takes place in a powerful blender, called a colloid mill, where spinning blades break or shear the liquid asphalt into suspended microscopic particles. The water, or soap solution, is immediately introduced to form the emulsion.
The emulsifier – an engineered surfactant (detergent) or surface-active agent – maintains the microscopic asphalt droplets in a stable suspension, keeping them from recombining. The amount and type of surfactant used, along with other variables, controls properties of the emulsion critical to performance in the field application.
For example, emulsifiers affect the “break” time following placement on a road, in which the water evaporates, leaving the residual asphalt behind. Asphalt emulsions partially are categorized as rapid setting (RS), medium setting (MS), slow setting (SS) and quick setting (QS) emulsions.
Today, the most common types of emulsions used for bond coats include slow-setting grades of emulsion such as SS-1, SS-1h, CSS-1, and CSS-1h and the rapid-setting grades of emulsion such as RS-1, RS-2 and CRS-1.
Tips for successful bonding
The correct placement of asphalt emulsion as a bond coat is important for long-lived asphalt pavements. Here are some tips for a successful bond coat.
- The correct application depends on four variables, according to manufacturer E.D. Etnyre & Co. They are the desired application rate, in fractions of a gallon per square yard; the forward ground speed, in feet per minute; the asphalt pump output, in gallons per minute; and the width of the spray in feet. The onboard metering system gives the operator precise control of the application of asphalt, with either manual or computer control.
- The spray temperature of the emulsion is important. If it’s too cold the asphalt emulsion may not flow properly and can cause issues with the distributor pumps. If it’s too hot, the emulsion may separate or “break” in the tank. The temperature depends on the particular emulsion used, consult with the emulsion manufacturer for specific reccommendations. Document the details in case you have to reconstruct what you did.
- Keep the storage and distributor tanks clean, especially when changing from one emulsion to another, for example, emulsion for a bond coat to emulsion for a chip seal. “Empty that tank and clean it,” Decker urges.
- Nozzle alignment is an important part of the process; get all nozzles at the same angle. If not, a non-uniform spray pattern will result. “Try to achieve a triple overlap,” Decker said. “A double overlap can work too, but triple is the most common and a little more forgiving. A triple overlap ensures uniform placement of material, and that’s what we want.”
- Not only do the nozzles have to be aligned the same way, all nozzles need to be the same size and type. Understand what kind of nozzle you have, and make sure they are designed for the intended application rate. Nozzles used for chip seal operations typically will not perform well in a bond coat application.
- Height of the spray bar is important. In the old tachometer-based system, as the amount and weight of emulsion in the tank decreased, the spray bar rose. The operator had to account for the rising height of the spray bar, but today’s computer-driven systems do that automatically, Decker said.
- Calibrate your distributor to confirm what’s being put down. “This is not rocket science,” Decker said. “Before you spray, weigh some pads that are flat and absorbent. Cotton diapers are a good option. Lay them down flat on the roadway, drive over them with the distributor, and pick them up and weigh them again. That will indicate whether the distributor is working at the right distribution rate.” ASTM D2995-14: Standard Practice for Estimating Application Rate and Residual Application Rate of Bituminous Distributors is a test standard that describes this process.
- Clean or sweep the pavement before applicaetion. Adjust the application rate as you need to, depending on the age and condition of the pavement.
- The amount of the bond coat material applied is important. “If we don’t use enough tack, we will get sliding between layers,” Decker said. “If we use too much tack, we can get a slip plane that will cause the same problem.”
- If a fine milled surface texture is present, less tack will be required than a standard texture. A really rugged surface will use more tack coat to cover as it presents more surface area. Don’t use tack coats over open graded mixes.
For more information about bond or tack coats, or about asphalt emulsions, visit the Asphalt Emulsion Manufacturers Association at www.aema.org.