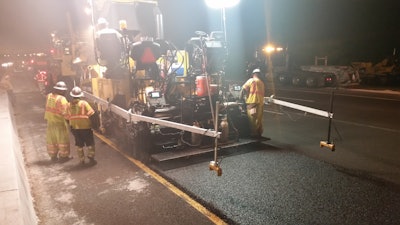
The Lane Construction Corp., a leading contractor specializing in highways, bridges, mass transit and airport systems headquartered in Cheshire, CT, completed a design-build project on I-64/I-264 for the Virginia DOT (VDOT) in November.
The project included major restoration work designed to increase pavement life by 15 years or more for distressed eastbound and westbound segments of I-64 and I-264 in Norfolk and Virginia Beach.
“There were two separate intersecting Interstates involved in this design build,” says Mark Range, assistant plant manager with Virginia Paving Company, a division of The Lane Construction Corp.
The first section is a 3-mile stretch of I-264 with four lanes in each direction that is the main artery connecting Norfolk to Virginia Beach. This segment of road also takes you to Portsmouth going west and heading east toward the main oceanfront area.
The second section is a 7-mile stretch of 1-64 with three lanes in each direction and the main interstate connecting I-264 to the Norfolk Naval Station on I-564. It also takes you west toward Williamsburg and Richmond and east to Chesapeake.
“Both of these highways carry in excess of 50,000 vehicles per day,” says Range. “With the summer tourist traffic and the always present Norfolk Naval Station commuter traffic, they’re very busy roadways. Therefore, all of this work had to be done at night.”
Prior pavement condition
These highways were originally concrete pavement that over the years had deteriorated to the point that the state could not keep up with the maintenance and repairing of potholes, says Range.
VDOT let the first contract to patch all the concrete pavement and repair/hot seal open joints. Next came the second contract to mill and repave the existing asphalt shoulders and overlay all of the concrete patching with a ¾-in. lift of THMACO (thin hot mix asphalt concrete overlay).
The THMACO contract was performed by Virginia Paving Company, a division of The Lane Construction Corp. This was followed by the leveling course, a 2-in. lift of 19MM SMA (stone matrix asphalt) and a 1.75-in. lift of 12.5MM SMA, along with raising the median barrier, drainage structures and guide rail.
“Since the roadway was going to be raised 3.75-in. with new asphalt, we had to raise all the concrete median barriers separating the eastbound and westbound lanes, all the drainage structures, all of the guide rail, as well as all new asphalt curb and back-up material under the new guide rail,” says Range.
Preparing the pavement
The first step to properly prepare the pavement was to survey the entire job and identify areas that did not drain properly or had under-spec or less-than-desired cross slopes.
“Once these areas were identified and marked out, we needed to cut tie-in and tie-down joints longitudinally and transversely so the level course would blend in with adjacent lanes,” says Range. “This also helped to prevent raveling of the edges when we opened to traffic.”
The joints were cut in by a milling machine. Then it was time for the paving crew to pave a leveling course to increase the cross slopes to ensure water would drain from the roadway properly.
“This was a challenge because the required leveling had variable depths,” says Range. “In many instances, this work was being done across two or three – and in some cases four – lanes of traffic with vehicles traveling 55 mph two feet away from the milling and paving crews. We all know most of those cars and tractor trailers were not obeying the legal speed limit.”
Joint cutting also needed to be done through exit and entrance ramp areas as well. Once this step accomplished, the main paving began.
The paving process
With the ¾-inch THMACO layer already installed over the concrete, the next step called for two, and in some areas three, additional lifts of asphalt. A variable depth lift of mix (SM-9.5A) for cross slope adjustments, then a 2-inch lift of 19MM SMA and then a final 1.75-inch lift of 12.5MM SMA would be installed for the final riding surface.
“Out in front of the paving crew, the milling crew cut tie-in joints before and after every bridge, at all of the exit and on ramps and interchanges, and at the beginning and end of the project, so the new asphalt layers would blend in to the existing grades,” says Range. “This entire process had to be done prior to the paving of each new lift of asphalt.”
This was a huge task. There are 22 bridges on this project to tie into, 12 major interchanges to pave through, and 32 exit and entrance ramps to pave and tie into. In all there were over 200 tie-in joints required.
With all of the bridges, ramps, interchanges and tie-down points, the average length of a paved section without stopping and picking up was approximately 2,300 LF. “Despite the numerous short sections, the average IRI numbers on I-64 were less than 50,” says Range.
The mix designs for the project included 19MM SMA and 12.5MM SMA mixes with PG76-22 asphalt cement used on the mainline while conventional IM-19.0A and SM-12.5A Superpave mixes were used on the shoulders.
“The SMA mixes, even though they are more costly, were good choices for the mainline due to the stiff binder in these mixes that prevent cracking and rutting while holding up to the high traffic volumes and also giving the owner a longer service life,” says Range. “You get what you pay for with SMA. Very expensive but better performance. Conventional Superpave mixes cut costs on the shoulders as they were not subject to the same traffic volumes and stresses as the mainline.”
The combination of 19MM SMA, 12.5MM SMA and conventional Superpave mixes for the leveling and shoulder work added up to over 100,000 tons of asphalt placed by Lane Construction crews.
Challenges
For Lane Construction, there were many nightly challenges, says Range.
“One challenge was the lane closure times and restrictions we had to adhere to,” he says. “When working on the left lanes, we were only able to close one lane at the beginning of each shift. With only a 6-foot left shoulder and a 12-foot lane closed, we barely had enough room to unload our equipment from the trailers and get started, especially the MTV and paver, which is a safety concern for us.”
Crews also had to be totally off the road by 5 a.m. or face heavy fines compounded every 15 minutes. Thinking and planning ahead was key. And keeping one eye on the weather at all times was important as well.
In order to make it safer in the tight quarters on the left lanes and allow an on-time start, crews had to use a rolling road block with the help of a state trooper. This allowed equipment that was just unloaded the ability to get in front of the tractor, then the tractor could hook back up to the trailer and get out of the way. “When on the left side, this was the only way we could unload our equipment safely,” says Range.
Another challenging aspect of this project was the I-64 and I-264 corridor had three separate contracts going on all at the same time. This presented many lane closure conflicts throughout the project that had to be worked out amongst all the contractors and subcontractors.
“Virginia Paving was fortunate enough to be doing the paving work on three of the four ongoing contracts, so that helped some, but this scheduling was a nightmare,” says Range. “Many changes were made to accommodate all the activity while still trying to maintain the production we were shooting for. Communication and many meetings were the keys to making this work.
“At the end of the day, this turned out to be a very safe and productive project,” he continues. “Looking back now at all this organized chaos, you really get a sense of pride and satisfaction knowing we pulled it off under less than ideal circumstances.”
Relentless perseverance, planning and teamwork will lead you down the road to success no matter how big the challenge, says Range.
“I’ve worked for The Lane Construction Corp. and Virginia Paving Company almost 40 years now, and the level of coordination and cooperation that was required between all involved rivals anything I’ve seen so far,” he says. “Look up the word ‘teamwork’ in the dictionary and this project will be listed there.
“Look up the words ‘working safe’ and it will be defined there as well,” he concludes. “This mentality and culture is what The Lane Construction Corp. and their division Virginia Paving Company has lived by for the past 125 years. Our people are our biggest asset.”