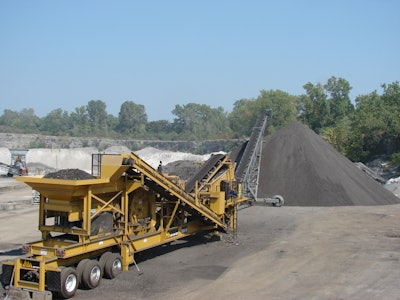
Self-diagnosing a health issue can lead to incorrect treatments, prolonged recovery and perhaps an even more costly outcome. The same applies in the asphalt recycling industry. Operators shouldn’t select an asphalt recycling plant before carefully sorting through the options and thoroughly evaluating what they need.
A short visit with the manufacturer, a couple of questions and a thorough evaluation of an operation saves an operator from the turmoil that comes with selecting the wrong plant. Not only that, but the right machine sets an operator up for achieving a fast return on investment. Here are a few things to consider to ensure you select the equipment that’s right for your operation and ROI goals.
1. Profit from portability
The obvious appeal of mobile crushers is the ability to move the unit closer to where it’s needed. Even with this advantage, it’s important to inspect a mobile crusher to see just how portable it is.
Ask the manufacturer how long it typically takes to set up the machine. Some models are designed to only take an hour or so, but other models take days to set up because they require extended use of a crane to move the equipment in place. Not only does this require the extra costs of renting the crane, but also labor costs to have someone operating that crane.
In addition to setup time, consider transportation. Often, operators have to transport the hopper feeder separately and break the plant into multiple pieces to meet Department of Transportation weight regulations. Unfortunately, this means more workers are needed to transport and lift the equipment, which results in greater labor costs as well as higher fuel expenses. Look for a plant with a lightweight, easy-to-remove hopper that one operator can install within minutes. Or, look for a plant that is compact and light enough to be transported without removing the hopper. You’ll save time and labor costs.
2. Follow your production prescription
Properly sizing your equipment to expected production capacities is critical to the success of a business. Think of it like a patient following his or her doctor’s prescription. To achieve a full recovery, the patient listens to the doctor’s orders. In the same way, asphalt recycling plant managers must take certain steps to meet their production goals, the first being to determine those goals before making a purchasing decision. A crusher that is too small fails to produce the desired tonnages, which limits profits and caps the organization’s growth potential. On the other hand, a machine that’s too large costs more to maintain and doesn’t add value to the operation.
Before buying a machine, calculate the desired output. For example, if an operation can sell 450,000 tons of material per year, its plant needs to produce 37,500 tons each month.
If the crusher is set up to run two days per week for nine hours per day, the operation will require a machine capable of processing just over 400 tph.
3. Compare apples to apples
It’s easy to get caught up in price. While saving money on the initial purchase price is important, so are the extras that will save time and money in the future. Understanding how certain features can impact operating costs is critical before buying a unit.
See if the unit has an on-board power source as well as auxiliary outlets. These allow you to run a complete crushing operation from one source, eliminating the need for separate generators to power multiple pieces of equipment, such as individual crushers and screeners.
Consider a machine that can recirculate material. For example, a double-deck screen and conveyor automatically sends oversized material from both screens back to the crusher for sizing. This eliminates an extra person and an additional loader or excavator to pick up the material and manually re-feed the crusher, which reduces expenses and can increase production by as much as 20 percent.
In addition, some double-deck screens also enable contractors to crush and classify as many as three different sizes of material. This offers contractors the versatility to size their products for the best sale potential and appeal to multiple customers.
4. Defensives up
Immune systems are at constant work defending the body from sickness. Much like immune systems, crushers need to withstand daily abuse. That’s why investing in quality equipment and components up front will save money in the long run.
Take, for example, a crusher’s discharge point. This area of the machine is under a lot of stress for the majority of the machine’s run time, and as a result it requires regular maintenance, such as wear-liner replacements. Some machines, however, have a specially designed discharge Rock Box that eliminates wear-liner replacements. The specialized design uses a shelf system with an abrasion-resistant wear bar that allows crushed material to build up and act as a wear liner. The result is dramatic cost savings on labor and wear part
Be sure other components, such as conveyors, bearings, rollers, shafts and drives, are robust and built for high wear. For example, some manufacturers design blow bars that are better in different applications and will last longer than other types of bars.
To reduce cleaning and maintenance requirements, some units will even feature a dust suppression system.
Catwalks are also a good feature to consider. These make it easier to change out screens and provide convenient access to crucial maintenance and cleaning points, which saves time and enhances safety.
A fast recovery is part of every patient’s goals, but it’s more important to have a lasting recovery. In the same way, stop and consider all elements of the crusher and the operation’s needs, as these can have a huge impact on long-term costs. After all, the right machine will make every job easier and more profitable today and beyond — just what the doctor ordered.
Sean Donaghy is the national sales manager at IROCK Crushers. He has more than 25 years of experience in the crushing business and has been with IROCK for more than 10 years.