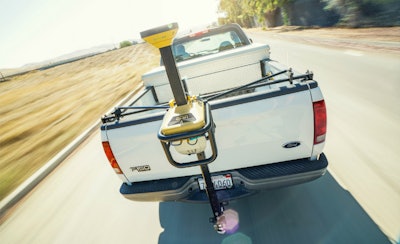
Traditional road mapping is a long process that includes manual labor over an extended amount of time with lane closures and thus traffic delays.
In an effort to streamline the lengthy process from surveying an existing road to the actual milling and/or paving of the new asphalt surface, Topcon has developed the SmoothRide system. SmoothRide is comprised of a vehicle-mounted scanner that collects data at driving speeds to map the road surface, custom software to model the data and create a smoother riding road, and patented sonic tracking technology with GPS to provide variable depth milling and paving.
“In most cases, it’s inconvenient or impossible to shut down a road and map its surface using traditional survey methods,” says Jan Mennink, product manager for paving products with Topcon Positioning Group. “Now with SmoothRide, it’s possible to eliminate the need for lane closures and map road conditions at highway speeds.”
By scanning roads instead of surveying them, you’re eliminating the need for crash trucks, escorts or any other typical road survey collection obstacles.
“With the new RD-M1 scanning unit, the system maps the existing surface elevations — with many more points captured versus what can be expected with traditional tools — which provides more accurate data needed to confidently estimate materials, as well as form the basis of the final design surface,” Mennink says.
“Using the SmoothRide solution, the contractor has tighter control over the material used at each location. Also on resurfacing jobs, material management is very important because contractors generally must stay within yield limitations,” he says. “In effect, SmoothRide provides the best of both worlds as it offers the ability to use the same amount of material and end up with a smoother road.
“The time saved from start to finish, without the need for lane closures, could be enough reason alone — but the accuracy of the system also produces a much smoother end-result than with traditional methods.”
How it works
SmoothRide is a workflow solution that touches all aspects of a milling or paving job. It requires a revolutionary combination of core Topcon technologies. The RD-M1 vehicle mounted road resurfacing scanner is required for SmoothRide. It is used for collecting surface information, processing and design software to create a design and machine control and GNSS components for the milling machine or asphalt paver.
“Whether the contractors would have to purchase all of the other components depends on various factors,” Mennink says. “For sure the machine control and GNSS components are required (display, controller, antennas and sonic trackers). The RD-M1 and processing and design software might be in the hands of a separate organization such as an engineering agency. These agencies might find the RD-M1 and the software useful for other applications.”
Once the road information is gathered, operators can use Mobile Master Office point data processing software to recreate the existing surface. MAGNET Office with Resurfacing is then used to digitally create a high-resolution model of the required finished mat. The resurfacing module allows operators to create a design using specific regulatory requirements such as minimum thickness, desired cross-slope, and overall smoothness.
That information is taken to the milling machine first resulting in a perfectly smooth surface that translates to a smoother paving job. In case of overlay paving jobs, the built-in capability to compensate for differential compaction will result in a smooth surface after compaction of the first lift, whereas currently multiple lifts would be required.
“With the SmoothRide system, contractors can maximize work hours and materials, eliminating the need for multiple lifts,” Mennink says. “The result is a much smoother road than with traditional paving concepts and is a breeze compared to conventional methods. It all adds up to faster completion times.”