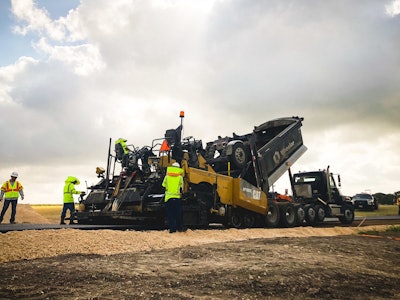
Since 1916 some form of federal DOT has been offering funding for states to expand highway infrastructures through the Federal Aid Road Act. Fast forward to 2019 and we have a Federal Budget of over $76B to maintain and improve our highways and interstates, that’s just the Federal spend and doesn’t include State budgets.
If I were allocating over $76,000,000,000 I’d be interested in keeping tabs on how the money is spent, wouldn’t you? Well, to get visibility that helps DOTs set budgets, the Federal Highway Administration and State DOTs end up requiring each state to provide their own independent verification record, to show a “paper trail” of materials purchased and materials delivered.
For nearly 100 years DOTs have been tracking these funds by staffing some unfortunate employee to stand onsite nagging drivers and crew members to collect paper tickets every time a load is delivered to the paver. Then that person would bring stacks of paper tickets back to the office for archiving and in more recent history would spend days manually entering that data into spreadsheets. It wasn’t until the last 5-10 years that DOTs have started taking advantage of the digital age and using technology (that’s been around for 20 years) to help utilize their staff more efficiently. Rather than flagging down trucks at a jobsite, collecting towers of paper tickets, and handling massive loads of manual data entry.
Tech Improves Productivity
Now mobile devices and phones have reliable and accurate GPS data, high resolution camera, and widely available cellular data. This means technology like Optical Character Recognition (OCR for short) and digital archiving from the field can be utilized to spend their employee-hours in better ways. Rather than staffing someone to be in the field on the DOT’s behalf they can put this technology in the hands of the asphalt contractors that also helps their business save costs and provides the visibility that DOTs want.
To summarize that lengthy sentence: new tech is making digital tickets, gps stamped deliveries, route tracking and more, available with just a smartphone. According to Rebecca Embacher at the Minnesota Department of Transportation, they are testing this out with a few projects currently by requiring digital ticketing. This allows them to track each load delivered and cut down on the amount of manual data entry required on their end to archive these tickets since the tickets are automatically uploaded, organized and sorted for each job. Embacher says she wouldn’t be surprised if DOTs are requiring this basic tech nationwide within the next five years, especially since the social world of DOTs is small and word travels fast.
While digital ticketing is a big step forward, there’s so many more data points that are important to DOTs being able to track progress and budget usage on these projects. They’ve expressed that tracking truck routes, thermal segregation and asphalt composition/quality are all important to monitor through a DOT Portal. For example, there are often cases when MnDOT will provide the contractor with dedicated routes they want trucks to use. In efforts to cut down on traffic through a specific neighborhood, easing the wear and tear on local roads, or even to cut down on fraud. There have been reported cases of a driver delivering part of a load to another “buyer” before delivering the remaining load to a jobsite while the DOT has paid for the full load.
Tech Increases Quality
Another and even more important example is that by using smart data-driven dispatching and route planning, thermal segregation can be significantly decreased since wait times are reduced for trucks to unload. Pavers have been using infrared technology for years to monitor thermal segregation but the trouble with this solution is that the defects are found after the asphalt has been laid.
Crews are constantly reacting to temperatures coming out of the paver and making reactive adjustments and we all know that proactive solutions are often better than reactive solutions. Studies show that the longer HMA sits in the bed of a truck during transport, the more thermal segregation progresses. So arguably the best way to fight it is to accurately schedule the correct number of trucks for a job and stagger their start times to minimize waiting times at unloading, an easy task using digital tools made just for asphalt contractors. Ultimately creating more reliable, longer lasting, and safer roadways for motorists.
As an asphalt supplier and contractor you’re probably thinking, “Yes that all sounds great, and I’d love this technology for my business, but that costs money.” Luckily DOTs know this and they’re ready to make the commitment along with you. There are many projects that DOTs are including the tracking software as a line item they’ll pay for, an item that the contractor can charge for.
There are many details that State DOTs and the Federal Highway Administration want to track and monitor, like delivery verification, route tracking, thermal segregation and fraud prevention. Luckily the right technology is here today, and it’s mutually beneficial for both parties providing cost savings for asphalt companies and the visibility that DOTs want.
--
Tarun Nimmagadda is chief executive officer at Ruckit