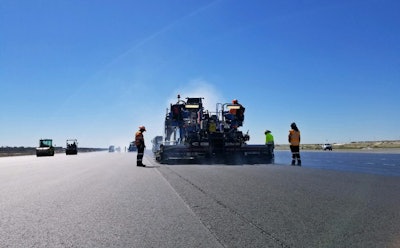
The history of asphalt mix design has changed significantly over the years with the goal always to create stable and durable pavements.
Today, asphalt mixtures are primarily designed under the Superpave system however since its implementation many state DOTs have indicated that distresses such as cracking and raveling have become the primary factor controlling the service lives of asphalt pavements. Mixtures designed with too much asphalt may be susceptible to rutting, while those with too little asphalt are prone to cracking, raveling and other durability related pavement distresses.
Consequently, DOTs adjust their mix design requirements from the AASHTO Superpave mix design standards to improve the durability of their mixes. However, a growing awareness of the shortcomings of the Superpave mix design system has led to many people from all parts of the asphalt pavement community to seek a new approach to asphalt mix design.
As a result, there has been more of a shift to using a balanced mix design (BMD) approach that focuses on designing asphalt for performance and not just meeting the specified volumetric recipe. And because achieving balanced mixture performance is key to a long-lasting pavement, it’s crucial to know what these mixes are and how they will benefit the industry moving forward.
Why Does BMD Matter?
This new era of mix design promises to result in longer lasting asphalt pavements, something all asset owners can agree is needed. The catalyst for change started with the recognition that some asphalt pavements have not performed to expectations even though they met the project’s specifications.
The word “balanced” in balanced mix design infers that the mixture will have good resistance to rutting and cracking. The end goal is to produce a mix performance test simple enough so that every asphalt lab can perform them, but also one where the results are demonstrably related to the mixture’s resistance to the distress. Just because we can measure a mix characteristic does not mean that characteristic is a good indication of performance.
Explore: Take a 360° Tour of an Asphalt Plant
Momentum for BMD is evident by the number of workshops, webinars, training classes, research projects and pilot projects that now have a focus on BMD. Day to day conversations among asphalt technologists in labs and offices across the country now center on how to implement BMD tests in mix design and quality control and quality assurance testing.
BMD Defined
To move the BMD conversation forward, the National Cooperative Highway Research Program (NCHRP) initiated Project NCHRP 20-07/Task 406 to assist in the Development of a Framework for Balanced Mix Design. According to the report, the objective of this research was to develop a framework that addresses alternate approaches to devise and implement balanced mix design procedures incorporating performance testing and criteria. The framework was to be presented in the format of an AASHTO specification and recommended practice and shall encompass a wide variety of testing procedures and criteria.
Over the past few decades, numerous performance tests have been developed by different researchers to evaluate the rutting resistance, cracking resistance and moisture susceptibility of asphalt mixtures. From all this data, the Task Force identified three potential approaches to the use of BMD:
1. Volumetric Design with Performance Verification: This approach starts with the current Superpave mix design method for determining the optimum asphalt binder content. In this method, the mixture is sometimes tested using selected performance tests to assess its resistance to rutting, cracking and moisture damage. If the mix design meets the performance test criteria, the job mix formula (JMF) is established and production begins; otherwise, the entire mix design process is repeated using different materials (e.g., aggregate or asphalt binder) or mix proportions until all of the performance criteria are satisfied. This is the most common approach currently in use by state highway agencies (SHAs).
2. Performance-Modified Volumetric Mix Design: This approach begins with the Superpave mix design method to establish a preliminary aggregate structure and binder content. The performance test results are then used to adjust either the binder content or mix component properties and proportions (e.g., aggregates, asphalt binders, recycled materials and additives) until the performance criteria are satisfied. For this approach, the final design is primarily focused on meeting performance test criteria and may not be required to meet all of the Superpave volumetric criteria.
3. Performance Design: This approach establishes and adjusts mixture components and proportions based on performance analysis of cracking and rutting tests, with limited or no requirements for volumetric properties. Minimum requirements may be set for asphalt binder and aggregate properties. Once the laboratory test results meet the performance criteria, the mixture volumetrics maybe checked for use in production. This approach is not used by SHAs at this time but could be a viable option.
In short, a BMD will incorporate two or more performance tests such a rutting test and a cracking test to assess how well the mixture resists common forms of distress and makes sure the right mix is used for each job, every time.
Based on the survey results and a literature review, NCAT developed a framework for BMD in the form of a draft AASHTO standard practice and standard specification. Agencies may select the performance tests of their choice for rutting resistance, cracking resistance and moisture susceptibility.
How are States Implementing BMD?
As a result of this research, a number of highway agencies have started to either explore or adopt approaches to BMD and others are investigating cracking tests for integration into their mix design requirements. Some of the states that have significant experience with BMD are Louisiana, New Jersey, California and Texas. These locations are moving from a volumetric mix design methodology to a BMD.
Over the past few years, the Louisiana DOT has worked to improve conventional asphalt mixtures with the development of a BMD specification. Louisiana asphalt mixtures are typically rut resistant and the balanced approach commonly results in increased asphalt contents.
Research found that mixes that were designed and tested using the Hamburg Rutting Test (HWTT) based on 2013 BMD specs showed equivalent or better HWTT results compared to previous mix designs, indicating that the modification did not appear to affect the rutting resistance of the mixtures. In addition, mixtures that contained polymer-modified binders showed better results as compared to those with unmodified binders.
As a part of this testing, 11 mixtures were evaluated for rutting performance using HWTT per AASHTO T 324. Tests were conducted at 50°C for a total of 20,000 passes. Fracture resistance potential was assessed with the SCB-Jc test at 25°C. The researchers indicated that most mixtures designed according to the 2006 and 2013 specifications performed well in the HWTT. A 10 mm HWTT criterion at 20,000 passes was used for mixtures containing unmodified PG 64-22 binder, while a 6 mm criterion was used for modified binders. The 11 mixtures designed according to the 2013 specification showed equivalent or better HWTT results, indicating that the modification did not appear to affect the rutting resistance of the mixtures. In addition, mixtures that contained polymer-modified binders showed better results as compared to those with unmodified binders.
Read Next: What are Pavement Rejuvenators & Why are they Important?
New Jersey, faced with a deteriorating transportation infrastructure, decreasing transportation funding and increasing traffic conditions began to implement a performance-based asphalt mixture design system for their “special asphalt mixtures” in 2006. Each of these performance-based mixtures is required to undergo performance testing during mix design, test strip and project construction phase to ensure the produced mixture achieves the desired performance for the specific pavement structure.
Three asphalt mixture performance test methods were utilized to test the New Jersey performance-based specification:
- Asphalt Pavement Analyzer, AASHTO T 340: Determining Rutting Susceptibility of Hot-Mix Asphalt Using the Asphalt Pavement Analyzer;
- Flexural Beam Fatigue, AASHTO T 321: Determining the Fatigue Life of Compacted Hot-Mix Asphalt Subjected to Repeated Flexural Bending; and
- Overlay Tester, Tex-248-F: Test Method for the Overlay Test.
Field performance data since then indicates that all mixtures performed exceptionally well, and in some cases performed better than conventional NJDOT asphalt mixtures. As the performance-based mixtures have become more widely accepted and the methodology of design and production becomes more efficient, NJDOT plans to implement some form of performance-based specifications for all asphalt mixtures.
The Future of BMD Looks Bright
With research leaning towards the use of BMD growing by the day, the industry should look to implement this mix approach in the near future. Contractors need options to innovate and remain competitive and a BMD approach gives them that. By removing volumetric limitations and allowing for innovation instead of sticking to outdated specs, pavement can be designed to last longer, be more sustainable and even cost less. BMD allows for the agency and contractor to partner in pavement design innovations to further the life of asphalt pavements and extend our infrastructure funding throughout the country.
Recognizing this, many DOTs and contractors are realizing the benefits of BMD and are working toward implementation. Contractors who are stakeholders in the world of asphalt pavements should be involved in process to fill in the gaps of the BMD framework and continue the work to make our roads more durable and sustainable.