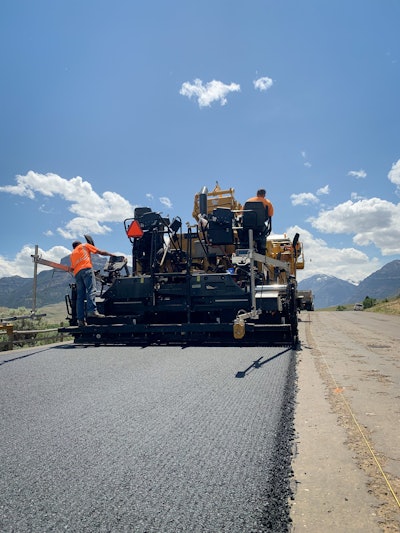
Many paving companies know the importance of achieving density right behind the paver when the mix is still at its hottest temperatures. This is why articles on compaction and achieving optimal rolling patterns are consistently some of the top viewed content on our website. Obtaining compaction right behind the paver is also why manufacturers are working on developing higher density screeds that help achieve density levels before the roller even hits the mat.
A new type of screed plate has recently been introduced to the market that also helps aid in compaction behind the asphalt paver, but it's not like anything we've seen in the industry before.
Speed Matters
Stuart and Michael Frost spent hours building roads and acquiring their first equipment fleet of Tonka Toys as young boys. They joined the family construction business at an early age and in 1999 they created Mountain Construction Company where you will still see them working on the crew today. This has led to years of firsthand industry experience, knowledge and a yearning to make the job more efficient and cost effective. This has also made them efficient in knowledge of what works and doesn't work so well in our industry.
Their idea for a new type of screed came after spending hours underneath a paver trying to change a worn out screed plate in the middle of the night. In between probably many frustrated moments, the thought came to them that there had to be a better way. That is when they decided to try and solve the challenge of quickly changing a screed plate and getting better densities behind the screed.
This patented system allows the contractor to remove and replace a screed in about two hours rather than two days. With the new patented AXENOX Screed System, there is no more chiseling out hard bituminous material or screwing off the nuts and working around the electric heating elements to change the plate. Once the aluminum conductor plate is installed, it does not need to be replaced for the life of the paver.
The AXENOX patented screed plate systems provide a 3-Dimensional progressive textured wave, eliminating the stereo type that all screed plates must be smooth. For the first time, there is a 3rd dimensional component applying multiple force vectors which allows the mix to roll and interlock more efficiently than the traditional flat screed plate. The result is higher densities on your uncompacted mat.
Density Matters More
The brothers didn't stop there they wanted to find a solution to get better density behind the screed. That thinking led to a patterned screed plate to aid in compaction and ride.
The AXENOX patented screed plate systems provide a 3-Dimensional progressive textured wave through the OXCLAW, eliminating the stereo type that all screed plates must be smooth. For the first time, there is a 3rd dimensional component applying multiple force vectors which allows the mix to roll and interlock more efficiently than the traditional flat screed plate. The result is higher densities on your uncompacted mat.
Currently there are four OXCLAW equipped pavers laying asphalt across the US. Each are showing the same results, no matter the depth laid, mix type, aggregate makeup or A/C polymer used the densities behind the screed are coming out anywhere from 85% to in some cases 89%!
“You can walk across the uncompacted mat, and you can feel how dense it is," Brent Carron, owner of Valley Paving, Inc. says. "The roller operators immediately notice it as well, they are not getting the squish out or leaving the marks and bumps they are used to.”
This is because the aggregate isn’t having to swim around to find its place in the more compacted mat.
Thermal profiles and mix segregation, both in heat and gradation along with longitudinal joint density, have been a hot topic for the asphalt industry. The texture of this screed plate adds a lateral component as well as a longitudinal and vertical component. As the mix enters the OXCLAW multiple forces are immediately applied to the aggregate. At multiple depths, along with the vertical and longitudinal forces, the mix is moved side to side laterally which kneads the aggregate in place until it finds its final resting spot. This movement aids in remixing your asphalt, helping with any possible segregation you may have.
Owners have been pushing the industry to find ways to increase mat density, reduce aggregate segregation, provide even consistent thermal temperatures and reduce longitudinal joint failures. Compacting an unconfined edge with the OXCLAW, you will see little to no “squish out” at the edges as its more stable. This lends itself to better more consistent densities on both sides of the longitudinal joint.
"There is nothing else like this in the asphalt industry," Carron says. "The idea that a non-smooth screed can produce an even, flat surface is crazy enough, yet this screed does so much more. The compaction is amazing from what we have seen so far. Our crew is getting 87% to 89% density before the knock down roller even hits it. And once the knock down roller does hit the mat, it barely compresses. No squish out on the edges, no cut marks from turning, it's like it's already stiff, yet still 280º F."
With 3D angles of attack, the OXCLAW is able to produce a higher density as well as a more uniform and smooth surface.
AXENOX has been putting this screed system to the test in Minnesota, Wyoming and Kansas with three different companies all experiencing the same results, higher compaction and smoothness.
"We're still finding out new advantages of owning this screed and what it can do for this industry. To date, we don’t have any complaints and the owners of the roadways we are paving are in awe and baffled at the same time, and can't believe the results we're getting," Carron says.
"We have a lot more tons of asphalt to lay with this screed, but so far, it's made a believer out of many. I’ve been in this industry since I was in diapers, and I don’t know of another advancement with the asphalt paver that compares to this."
AXENOX aims to push the limits of this old-fashioned way of thinking - “Let the screed do the work for you."