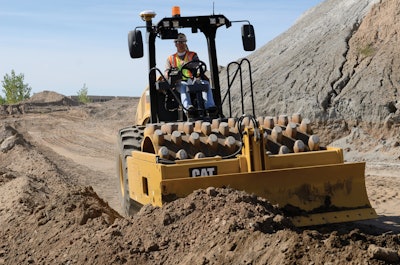
Regardless of how much experience an equipment operator has, it is difficult to achieve uniform compaction over a sizable area without the help of technology. Without technology, equipment operators are rolling blindly, so to speak. They make pass after pass, hoping that the desired density level is achieved throughout the area. Operators rely on their own intuition, as well as guidance from a QC (quality control) technician on site. This opens the door to quality issues, not to mention a fair amount of inefficiency.
“The main challenges road construction crews face relate to working with outdated equipment and methods,” says Vijay Palanisamy, senior product marketing manager for Dynapac North America. “Modern machines add sensory power and artificial intelligence, automating most of the functions and eliminating guesswork. A modern machine also delivers compaction results more efficiently without wasting fuel.”
That’s not to say that traditional, bare-bones soil compaction equipment has fallen short. The equipment itself does the job it is intended to do: compact soil. Without the help of technology, however, solving the inherent challenges with soil compaction is out of reach for both the equipment and the operator.
“The material is often inconsistent,” says Tim Kowalski, application support manager for Hamm. “Sometimes the contractor is moving soil around the site, or maybe even borrowing it from a different site. The consistency of that material is much different than when using a manufactured material. As a result, equipment operators often don’t know enough about the material they are tasked with compacting.”
Getting a uniform amount of moisture into the soil is a challenge. “This is simply due to the volume of material being used on a job, as well as the variability Mother Nature has put before us,” says Todd Mansell, product applications specialist for Caterpillar Paving Products. Additionally, larger jobsites often have three or four different types of material.
“Variable moisture content on a jobsite makes it difficult for equipment operators to get to the density they need,” Mansell says. “Even if 90-95% compaction is needed across a site, the operator may not know enough about the material’s sensitivity to moisture to know how many passes they will have to make. More experienced operators have a ‘feel’ for moisture content, but it is still difficult to pinpoint.”
Another big challenge operators face is identifying problem areas in the subgrade. “A roller operator may complete the prescribed number of passes, but it’s no guarantee that all areas are compacted full-depth to density,” says Bert Erdmann, heavy compaction product manager for BOMAG Americas Inc. “Several factors can cause variations in subgrade density such as base material changes, moisture content changes or a collapsed pipe.”
Regardless of the cause, soft spots must be identified and corrected prior to paving with asphalt. Again, this is difficult to do efficiently without the help of technology.
“Load-bearing tests performed on the subgrade only give a contractor an indication of compaction density for that specific location tested,” Erdmann points out. “Assumptions are made that the entire area is homogenously compacted similar to the tested area, but in many instances, this is not the case.”
Operators must understand their options
Technology is helping operators compact soil more efficiently—even when little is known about the material they are compacting. The challenge today, Kowalski says, is operator training. Many operators don’t understand the various settings on a compactor that can provide advantages in different scenarios. Examples include high/low amplitude and variable frequency.
Oscillation is another option that can improve the soil compaction process. Kowalski says oscillating rollers have been around a while, but are not commonly available on soil compactors. Hamm, however, does offer oscillation by way of a unique three-in-one drum.
Hamm’s VIO drum is a static, vibration and oscillation roller all in one. “Oscillation mode is useful in sensitive areas where you can’t have vibration,” Kowalski says. “In oscillation mode, the drum never leaves the ground; it’s a constant forward/backward motion. So you don’t get that seismic activity like you would with vibration.”
With Hamm’s VIO drum, switching modes is as easy as flipping a switch. But as pointed out earlier, the challenge is making sure operators understand how to take advantage of that option. Some amount of pre-compaction in either static or vibration mode will be needed first. Oscillation can be used toward the end of the compaction process to finish achieving the desired level of stiffness.
“Oscillation really works well when you have a heavier moisture content in the soil,” Kowalski points out. That is because oscillation reduces the amount of moisture that comes to the surface during compaction. “You get better compaction a lot faster,” Kowalski says.
Technology making compaction more intelligent
Intelligent Compaction (IC) has been around for a long time. But like with any technology, not all contractors have been eager to adopt it.
“Some contractors don’t see the value in IC unless it’s mandated by the state they are operating in,” Kowalski says. “But I’ve always said that contractor’s shouldn’t just use it when it’s required. Contractors should use IC all of the time so they get used to it. They can make IC a quality control tool for every job they do.”
Generally speaking, IC uses accelerometers to measure drum movement and provide an indication of soil stiffness. IC alerts operators when a section of subgrade is compacted to desired density. This helps boost efficiency and avoid over-compaction. “More importantly, this technology will allow the operator to identify soft spots in the soil and compact those areas to meet density specs,” Erdmann says.
Mansell points to another reason why more contractors haven’t invested in IC technology. A contractor ultimately needs to know the moisture content and meet a density specification of 90-95% Proctor Density. Technology such as accelerometers does not measure density. “IC doesn’t completely close the loop,” Mansell says.
However, IC helps contractors get much closer to closing that loop—and significant quality improvements and cost savings can be realized along the way. With recent advances in IC technology, the cost-benefit analysis is becoming easier for contractors to understand. Aside from being a quality control tool, IC also helps crews improve production since operators tend to make fewer passes. Fewer passes also results in reduced fuel usage.
IC can also assist with operator training. “When operators can see what they are doing on the tablet (display), they can start to feel what they are doing a lot better,” Kowalski says. This helps operators develop their skills much faster.
How IC helps solve soil compaction challenges
IC technology presents itself in different forms. On one end of the spectrum is a system that alerts the operator when desired compaction has been achieved. At the other end is a system that actually alters drum operation.
In the case of BOMAG, ECONOMIZER technology uses a single accelerometer to measure soil stiffness. An intuitive indicator light scale communicates those measurements on a display at the operator station. As compaction increases, more lights illuminate. Once all 10 lights are illuminated, operators know they can move onto the next area.
BOMAG’s TERRAMETER technology uses two accelerometers to show the operator an Evib value on the display, which directly correlates to soil stiffness. “This indicates when no further compaction is possible, and locates and documents soft spots and non-uniform areas,” Erdmann says.
Hamm’s IC solution, Hamm Compaction Quality (HCQ), has two main modules: Hamm Compaction Meter (HCM) and HCQ Navigator. With HCM, an accelerometer is mounted to the side of the drum and inside rubber buffers. Kowalski says this allows the accelerometer to capture the full movement of the drum. The further the drum moves, the softer the material is. As the drum begins to move less but faster, operators know the material is getting stiffer.
Caterpillar’s Cat Compaction Control system expands upon its existing CMV (Compaction Meter Value) technology. CMV is an accelerometer-based system that measures the rebound of the vibratory drum off the surface. Caterpillar’s proprietary MDP (Machine Drive Power) technology, on the other hand, measures rolling resistance.
“MDP helps fill some of the void left by traditional CMV technology,” Mansell says. “CMV is great for more granular materials, but doesn’t work well in cohesive soils where a dampening effect exists due to the plasticity of cohesive soils. Because MDP measures rolling resistance, it works well with a padfoot drum in more cohesive materials such as clay and clay-like materials.”
With Cat MDP, sensors are installed on both the drum and rear tires. “At the start of a project, the operator will typically have a QC technician perform a compaction test with a nuclear density gauge after each pass,” Mansell explains. “This helps determine how many passes are needed to meet the density requirement. Then a correlation can be established between density, the number of passes and the MDP value.”
Some asphalt contractors might see this lingering need for manual density tests as a deterrent to investing in IC technology. But as Mansell points out, the benefits are still there to provide a great return on investment.
“By establishing a correlation between MDP (or CMV) and the number of roller passes, crews can reduce the number of testing locations,” Mansell points out. “A big advantage is that the operator has an increased level of confidence in meeting the density specification. The operator can finish an area. Rather than wait for the QC technician to come and perform the acceptance test, the operator can move onto the next area.” That alone increases jobsite productivity.
VARIOCONTROL is an IC technology from BOMAG that actually alters equipment performance. It measures soil stiffness multiple times per second. As stiffness increases, the direction of the vibrating drum is automatically adjusted. “Compaction energy is adjusted by a specially designed excitor system, which changes the direction of the vibrating drum from true vertical for maximum depth penetration to purely horizontal as stiffness increases,” Erdmann explains.
Dynapac’s Seismic technology, which will make its North American debut at CONEXPO-CON/AGG 2020, considers that the soil and drum work together as one system. Seismic detects soil characteristics and automatically applies the correct amount of vibration energy when required. “This innovation leads to faster compaction results, as well as reduced power and energy consumption up to 30%,” Palanisamy says.
With the introduction of Seismic technology, Dynapac is upgrading its advanced technology package to Dynapac Active Bouncing Control (ABC) and Compaction Meter as standard on CA1500-6500 soil rollers. Speaking of Dynapac’s ABC, this technology also helps prevent over-compaction. “ABC detects double-jumping of the drum and disables the vibration function, saving both the surface and machine,” Palanisamy says.
Helping map compaction density
Asphalt contractors who see the benefits in IC technology can take it to an even higher level with mapping technology. Leveraging accelerometer and/or rolling-resistance data—in combination with satellite mapping—operators can see their progress in real-time.
In the case of Cat Compaction Control, a satellite (GNSS) receiver is placed on the roof of the compactor, enabling the compactor’s movements to be tracked. At the same time, the accelerometer and/or rolling-resistance sensors are measuring material stiffness. As the compactor works an area, a color-coded map is created showing each pass the machine makes, along with the correlating stiffness level (denoted by a certain color). That map is shown on a display at the operator station. Thus, operators have a real-time visual cue when a certain area has reached desired density.
This type of information is very valuable on the jobsite. It can also be helpful for contractors managing multiple sites at once. “Wireless data transfer allows all of this data to be uploaded to the cloud and accessed anytime on a mobile device,” Mansell says. “If a problem is ever found on a jobsite, a QC technician at another jobsite could pull up the map and start troubleshooting from there.”
Dynapac’s Dyn@lyzer solution includes the same components from Seismic technology with the addition of GPS and larger displays for tracking the position of the roller and pass counts. “Dyn@lyzer transfers required jobsite data back to the office real-time for faster decision-making and quality control,” Palanisamy says.
Hamm’s HCQ Navigator technology also has a satellite (GPS) receiver mounted on the roof of the compactor, enabling software to create a map of the machine’s movements and correlating soil stiffness. Hamm refers to that stiffness measurement as the HMV. Operators view this map and HMV data in real-time on a tablet at the operator station. Operators are then alerted when the HMV has been achieved.
With IC mapping technology in general, there are different setups and methods of installation. Kowalski says Hamm’s HCQ Navigator offers a “plug and play” receiver called OmniStar. With OmniStar, contractors do not need a land base in the field to provide the corrective signal.
“The corrective signal comes from a satellite,” Kowalski explains. “That’s why this system is subscription-based. The benefit is that you can move the receiver from job to job without having to worry about setting up a land base at each job and checking it with a rover. Not all asphalt contractors have people who know how to do this.”
New from BOMAG is BOMAP, a free downloadable app for Android phones. BOMAP can be used with all types of soil and asphalt compactors, regardless of brand. The free base level offers mapping and pass count control and runs off the mobile device’s GPS. Other levels with additional functionality are also available, such as Bluetooth GPS for increased accuracy, and incorporation of compaction results.
More states are beginning to require IC technology for on-highway jobs. As a result, Erdmann says more rollers will continue to be built with some sort of compaction measurement system as standard equipment. This will help asphalt contractors build better subgrades and prevent future failures in the asphalt mat.
Going forward, the future of soil compaction could very well be autonomous compactors. Satellite-based tracking systems are already in place. IC technology that measures pass count and material stiffness is already in place. Next up is machine guidance—and eventually full autonomy. Whether that happens over the next 10 years, 5 years or maybe even sooner, who knows. But make no mistake, that is the technological path manufacturers are on.