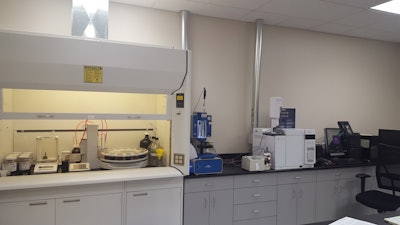
CW Matthews has 26 asphalt plants in the state of Georgia, and each one has a hot-oil heater to keep the plant and the asphalt cement hot.
The company began in 1946 with one tractor and two dump trucks, when C.W. Matthews and two local businessmen formed it after returning from the World War II Pacific Theater. 1954, Matthews formed C.W. Matthews Contracting Co. Inc., and three years later made the pivotal decision to enter the plant-mixed asphalt business.
The company continued to grow and expand over the next decades, and was involved in some of Georgia’s biggest infrastructure projects, including the $1 billion expansion of Atlanta’s freeway system, readying Atlanta for the 1996 Olympic games with the addition of high occupancy vehicle lanes on I-75, and serving as part of a three-company consortium for the construction of the 5h Runway at Harstfield-Jackson Atlanta International Airport, the largest public works project to date undertaken by Georgia.
Today, the company has placed more tons of asphalt paving in Georgia than any other privately owned company, has received numerous awards for quality riding surfaces and is consistently among the highest producing asphalt operations in Georgia. It also has the capacity to manufacture more than 5.5 million tons of asphalt each year.
“There are other construction companies in Georgia, but with our 26 locations, we may be the most diverse and serve more of the state in its entirety,” says Joe Hines, superintendent of plants with CW Matthews.
Heat transfer issues
Last year, Hines notes, CW Matthews was experiencing heat transfer issues at one of its locations. The company was having trouble transferring heat, so it reached out to Heatec, the manufacturer of the hot-oil heaters and AC tanks at that location.
“We have a strong relationship with Heatec,” says Hines. “We get our equipment from them, and when we have issues we're not familiar with, we trust them and the quality of their equipment and their support.
“At their annual service school, our general superintendents met Steve Beward and Jim Oetinger of Paratherm giving a troubleshooting presentation on heat transfer fluids as part of the training agenda in Chattanooga.”
After the meeting in Chattanooga, CW Matthews sent hot oil samples from its HMA plants to Paratherm for fluid analysis.
“We sent samples from plants that we thought were having issues as well as from plants where we thought the systems were running well,” says Hines.
Jim Oetinger, Paratherm's director of technology, who runs the testing, used the analyses to help with predictions, to identify issues, and to recommend which systems could use a fluid replacement, and which systems could be checked again in a year without further intervention.
“We took those recommendations back to Heatec, particularly for the unit where we had some heat transfer issues, and they came to the plant to help isolate individual parts of the circuit,” says Hines. “In some cases, they identified spots to put in new valves to help with isolating and cleaning specific parts of the hot oil circuit, for flushing right then as well as for future continuing maintenance.”
Hines says Heatec was a great asset when it came to the physical maintenance too.
“We elected not to use a chemical system cleaner because we have some jacketed lines that can be difficult to drain completely,” says Hines. “Heatec helped with the physical cleaning and draining, isolating each section, and using a vacuum truck to completely drain the old fluid.”
Detailed tests for decision making
Hines says working with Paratherm has helped CW Matthews improve its overall maintenance planning and execution.
“The biggest thing we gained from Paratherm was information and instruction on preventive maintenance, knowledge about the heat transfer fluid and its changing characteristics with use, and how to use the information to reduce reactive maintenance,” he says.
“We'd done lube-oil type sampling before, but that didn't give us the same detail,” he continues. “Those specialized hot-oil tests provide the characteristics and information to make decisions affecting our equipment going forward.”
Hines says the company has been testing their heat transfer fluids for over a year, and now they can begin to compare results to see how things are changing.
“We're now getting into year two of an annual testing routine for each of our 26 plants,” he says. “Now we can begin to study, with Paratherm and Heatec, the ongoing changes in the fluid, and the equipment, based on the fluid-analysis history.
“Now we can begin to compare how things are changing over time,” he continues. “That's preventive maintenance based on a running history, to keep the heaters and systems operating well on an ongoing basis.”