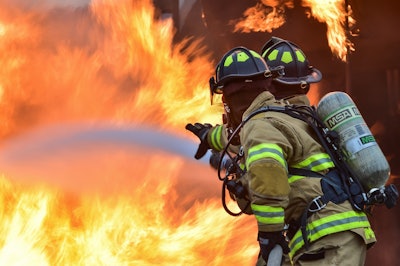
Fires are usually unexpected and can be devastating. For your asphalt plant, it is essential to have a fire safety plan in place.
A comprehensive plan not only provides information regarding the procedures to follow in case of an emergency, but also informs your employees and occupants of your commitment to their safety.
There are many ways a fire can start at your asphalt production facility. For example, bag houses, which are connected to the mixing drum, are designed to capture pollutants before they enter the atmosphere. These particles contain liquid asphalt, a combustible material. When a spark occurs an explosion in the bag house could result
Bob Petras, with the Inland Marine, Risk Control division of Travelers Insurance, recounts one example of a fire at an asphalt plant.
“There was one instance where there was an explosion in a company’s asphalt storage elevator,” Petras recalls. “Over the course of a day, during production, material built up at the base of the elevator. To be ready for the next day, the debris that accumulated needed to be cleaned out.
“The company sprayed diesel fuel at the base of the elevator to clear the material,” he continues. “This is not an uncommon practice for an asphalt plant and sounds fairly simple. But in this instance, the drum was still hot and the debris in the base of the elevator was still around 300 to 325 degrees.
“When you put diesel fuel that has a flash point of 165 degrees in an area where the temperature is 300 degrees, any ignition source present can result in an explosion.”
Fire hazards at asphalt plants
Some of the major causes of fire at asphalt plants can be: cleaning with diesel fuel; leakage around liquid AC and oil heater lines; and not properly cleaning the area around liquid AC tanks, resulting in ponding of combustible liquids within the diked area.
Any of these can result in a serious fire from heat sources like tramp metal, uncontrolled hot work, or electrical arcing.
“At no time should diesel fuel be used as a cleaning solvent near any heated work surface,” says Petras. “In fact, many states have mandated use of only noncombustible release agents. While this is done mainly for environmental concerns, it also eliminates potential fire hazards and occupational exposures to employees.”
Asphalt production facilities should have a formalized operations and maintenance plan in place that is developed based on their specific site needs. This should take into account the type and manufacturer of equipment and degree of anticipated use.
“Unfortunately, in many cases, operational instructions at asphalt plants is done informally on a basis of ‘passing the instructions on’ from one operator to another,” says Petras. “When this occurs, many safety-related tasks can be overlooked, which can have serious consequences.”
Formalizing all aspects of plant operations and security is one of the best ways to minimize risks.
Fire prevention plans
When it comes to putting a fire prevention plan in place, where should an asphalt plant start?
“It’s a good idea for plants to conduct a pre-plan assessment with their local fire department,” says Petras.
This could include evaluating key points such as:
- Where combustible materials are located
- How cleanup and maintenance are conducted
- Where the hot work occurs
- How water supplies can be accessed in case of emergency
- What are the integrity of access roads
It’s also smart to have a business continuity plan in place, says Petras.
“A highly effective plan will have four key components,” he says.
First is identifying the biggest threats or risks to the business. This entails understanding the risks that could leave employees, property and operations vulnerable. Companies can identify the risks most likely to occur based on historical, geographical, organizational and other factors.
Second is conducting a business impact analysis, which includes identifying the people, places, providers, processes and programs critical to the survival of the business. Consider who and what are absolutely necessary to restore critical operations. Then prioritize the need to restore each item after the event.
The third is prevention and mitigation planning and activities to help prevent an event (such as a fire or explosion) from happening in the first place. Consider emergency response, public relations, resource management and employee communications.
In the case of fire prevention, make sure there is an available on-site water supply for firefighting, adequate portable extinguishers, master fuel cut-off controls, master electrical cut-off controls, and adequate cleared space for exits and firefighting, if needed.
There should be a formalized maintenance and housekeeping program, a formal hot-work program in accordance with NFPA 51B “Standard for Fire Prevention During Welding, Cutting, and Other Hot Work,” and clearly defined and enforced safe work practices when using diesel to clean asphalt from the various components.
Lastly, it cannot be overstated how important it is to routinely test, exercise and improve the plan.
“A business continuity plan is an evolving strategy that needs to adapt to the changes in the business,” says Petras. “To test the plan, businesses can have discussions or hypothetical walk-throughs of scenarios, live drills or simulations.”