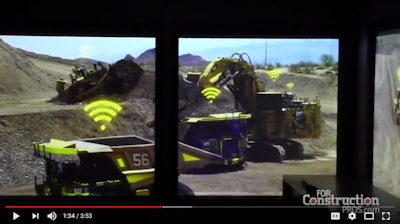
They’ll use the phrase “distributed computing” referring to the computers on-board mining haul trucks, and their contribution to the success of the Cat autonomous haul systems. Command reduces its dependence on the wireless data network supporting the autonomous mine site by allowing these computers to make decisions – avoiding rocks on haul roads, finding the berm on dump sites, avoiding collisions with people and other vehicles – even as the trucks carry out their larger directives in support of mine operations plans.
This isn’t some Buck Rogers concept. Caterpillar has installed two autonomous mine systems on two customers’ mine sites. By the end of 2017, 100 Cat autonomous trucks will be operating on three continents and in three different mining applications. The total includes one site where 56 Cat 793F trucks – the world’s largest fleet of autonomous trucks – which have achieved 20% greater production than manned trucks operating in the same mining complex. This fleet of autonomous trucks operates in a space with more than 150 manned vehicles – graders, loaders, water carts, light vehicles, dozers – all managed through the Cat MineStar System.
In the 4.5 years since operations began, the autonomous trucks have hauled more than 400 million metric tons of material, and there have been no lost time injuries.
It’s a compelling story for mines. They can take advantage of consistent, controlled environments to move material at the limits of the equipment’s capabilities all the time.
The fixed costs are intractable, as you would expect from a technology installed in fewer than 100 vehicles working in systems set up by Peoria’s own experts at three mines. “Substantial,” is a likely descriptor. Of course the kind of revenue these mines turn in an hour delivers a lot of substance.
Caterpillar claims that Command could be scaled down to 777-sized trucks and operations with ten, or even fewer, of them. Quarries could be good candidates, perhaps, but they make no pretense that this is a construction technology.
“Autonomy likes consistency,” they say. And there are few workplaces as inconsistent as a construction site. Or as transient.
It does appear that the groundwork is being laid for autonomous construction machinery, though.
The autonomous trucks carry LIDAR – total station technology – backed up by radar and all manner of sensory array. Their computers know what’s around them.
Their on-board computers are smart enough to identify things that must be avoided, and make sure the 300-ton vehicle avoids them.
And Caterpillar’s semi-autonomous Command for rock drills and dozers allows a remote operator to set up the machine in the right spot, get it started on a repetitive task, and then release it to complete the job on its own. While they start another machine on another task.
Given those building blocks, the relative complexity of a construction environment, compared to a mine, starts to sound like a computing-power and algorithm challenge – something today’s tech industry specializes in overcoming. It took a roomful of hardware to add and subtract 50 years ago. And we’ve got 50 years of accelerating digital innovation under our belts at this point.
I’m not suggesting we should expect to see autonomous backhoe loaders at CONEXPO in 2020. I’m almost certainly underestimating the technical challenges, and mostly neglecting the cost barrier.
But the only nearly universal problem the construction industry shares is finding people who can work effectively on job sites. And now we know for sure that computers can run machines safely and productively. It will be interesting to see how long it takes for an equipment manufacturer to offer an autonomous machine for construction.
Caterpillar press release: Cat Surface Mining Equipment Automation Grows
Caterpillar continues to grow automation technology for surface mining equipment at an accelerating pace. Cat technology applied to large mining trucks, blasthole drills and dozers has demonstrated its value in mines around the world, and it continues to evolve as mining companies seek means to lower costs and enhance safety.
By the end of 2017, 100 Cat autonomous trucks will be operating on three continents and in three different mining applications. The total includes 56 Cat 793F trucks that constitute the largest single fleet of autonomous trucks, which have achieved 20% greater production than manned trucks operating in the same mining complex. This fleet of autonomous trucks operates in a space with more than 150 manned vehicles—graders, loaders, water carts, light vehicles, dozers—and all managed through Cat MineStar System.
In the 4.5 years since operations began, the autonomous trucks have hauled more than 400 million metric tons of material, and there have been no lost time injuries. The Cat Command for hauling system reduces the number of people working in the active mining area, which reduces exposure to risk. The system also offers a minimum of 2+1 layers of protection to help ensure safe operation, and additional reporting capabilities available with the autonomous system help drive a robust safety culture and process improvements.
The autonomous trucks system has also proven reliable—with greater than 99.95% system availability.
Working longer and faster
Autonomous trucks achieve performance advantages over manned operations by working more hours each day and by working faster. Higher utilization of 2.5 hours a day on average results from no shift change, no breaks and no lunch. Refueling and inspection is the only stop on most days.
The Cat autonomous trucks system ensures that the trucks operate consistently—with no difference in operator skill level slowing down truck cycles. All trucks react the same way to environmental variables and drive to the design capability of the truck at all times. The system is fully dynamic and reacts in real-time to changing variables, which leads to continuously optimized assignment and management.
The rate of production is aided by consistently better operation than manned. Exchange times at the loading tool are 35 seconds or less, and in good dump areas, autonomous trucks reduce total dump time by 10 seconds compared to manned operation. In crusher operations, data shows throughput improvements of more than 10% within a week of implementing autonomous haulage. All of this has been achieved without major mining process changes.
To meet customers’ needs, Caterpillar is designing retrofit kits for Cat and other brands of trucks. In addition to retrofit, Caterpillar is expanding the number of autonomous models available from the factory.
Automating blasthole drills
Caterpillar is trialing an autonomous blasthole drill this year in preparation for commercial launch of the Cat autonomous drilling system in early 2018. The autonomous system will be available for Cat and other brands of drills. The system is designed for easy integration with other brands of drills and is configured so that the manual controls remain functional and ready for use when needed.
The autonomous drilling system builds on automated functions—Auto Mast, Auto Level and Auto Drill—offered on Cat drills and designed to reduce drilling variability between operators and to provide more drilling consistency. For drill guidance, the system builds on Cat Terrain for drilling, which incorporates satellite positioning technology to show the operator the locations of the holes to be drilled. Terrain helps the operator drill a precise pattern as a result of precise positioning.
The next step up in drill automation is the semi-autonomous system. This system allows the operator to position the drill at the beginning of a row of holes and then to set up the machine to drill the entire row autonomously. While the drill works autonomously, the operator can tend to other tasks or set up another drill to drill a row autonomously.
An optional arrangement includes a remote operator station that can be located near the bench or in a remote location. This allows a remote operator to position the drill at the beginning of the next row and start a new cycle again, or to manually drill holes from a remote location.
Going forward, the autonomous technology offerings will grow to reach a broad range of drill models. Also, the technology will evolve to feature Auto-Multi-Pass drilling, multiple row autonomy and obstacle detection.
Semi-autonomous dozer operation
Caterpillar is developing a semi-autonomous dozer system that leverages automated functions built into Cat large dozers and remote-control technologies, which are part of the proven Cat Command for dozing capability set. Caterpillar is first to develop such a system for mining dozers and, by the end of 2017, will have 19 Cat D11T dozers working semi-autonomously in validation trials at four customer sites.
The system is currently designed for a remotely located operator to manage four machines doing production dozing. Development work is progressing on push-to-edge applications, and this capability will be offered in 2018. Pivot-push capability is also being developed.
Through the use of Cat Terrain with Blade Control, Automatic Blade Assist and Auto Carry, the dozer cuts to plan using best practices. When operating autonomously, the dozer optimizes reverse speed. Consistency in operation pays dividends in lower operating costs.
With the operator/controller working from a comfortable, remote station, and fewer operators required, human exposure to health and safety risks is significantly reduced, and fatigue for the single operator is diminished. Another benefit of remote operation is reduced need to stop for shift change, breaks and meals—which translates into higher utilization of each dozer.
The Command for dozing technology has evolved rapidly since Caterpillar’s introduction of line-of-sight remote control in 2011. The semi-autonomous dozing system now brings together proven long-range remote control and onboard automated functions to tackle increasingly complex tasks safely and efficiently.
For more information about Cat MineStar System, go to: www.cat.com/minestar