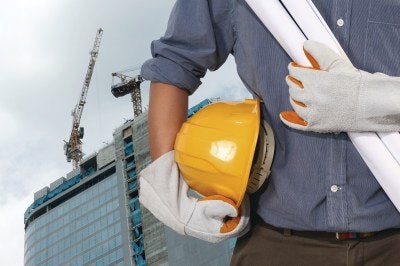
I am a general contractor and developer of commercial and industrial projects. On every project we select from our database of over 3,000 companies to eventually hire at least 35 subcontractors and buy from five to 10 suppliers. The bottom-line when choosing subcontractors and suppliers is all of them are almost the same except for price. Very few contracting companies do anything different than the others. They give you what you pay for - the minimum - no more and no less.
The problem with the construction business is every party wants to make more money by providing the minimum. Scope of work is clearly defined and most contracts are awarded to the lowest qualified bidder based on price. The bidder who offers better service for more money rarely gets the contract. This causes every general contractor, subcontractor and supplier to balance providing great service and exceptional quality while making a fair profit.
The 'WOW' Factor
I have asked hundreds of companies the following question: Why should customers pay more for you than your competition?
Everyone says they're better but can't point to anything specific they actually do different than their competitors.
How To WOW
1. Man the job
When bidding, be prepared to properly man projects with enough qualified trained workers. A larger job may take 15 men to maintain the schedule. If you only have 20 men on your entire crew, don't bid it and hope you can find enough help when you need them. I want trained crews led by jobsite foreman who:
- Have ongoing training
- Speak English
- Can make decisions
- Can read the plans
- Understand codes
- Know the contract
- Run a safe job
2. Be well financed
All general contracts and subcontracts include payment procedures for every project. Subcontractors and suppliers who are undercapitalized usually don't have enough working capital or an adequate bank line of credit to handle the work they can get. This causes a cash-flow crunch which doesn't allow them to hire enough help to get their jobs done on time. This creates stress and causes their businesses to run inefficiently. This makes everyone upset including the general contractor, construction manager and project developer. It also hurts the other subcontractors on the job. The underfinanced subcontractor then makes their problem become their customer's problem, which ends up in lost profits and no repeat work.
To run a successful subcontracting business, I recommend at least 20 percent of your annual sales volume in working capital plus a bank line of credit of at least 15 percent of your annual sales as a backup.
3. Manage the contract
Step one: Read the contract. Most subcontractors never read their subcontracts. I take care in writing specific and complete subcontracts to clearly lay out how I want the project managed. Most subcontracts include clauses which clearly define how to:
- Provide proper notice
- Get paid for extras
- Proceed on changes
- Present a change order
- Delay the project
- Keep the schedule
- Communicate
- Attend meetings
- Submit items for approval
- Get paid
- Proceed when not paid
- Handle disputes
What makes me really upset are subcontractors who ask for change orders 13 weeks after the extra work was completed. I want subcontractors and suppliers to mange per the contract and follow it to the letter.
4. Be proactive
Typical subcontractors wait for the general contractor's field superintendent to call and inform them to start work on the project. A proactive subcontractor is on top of every job they have a contract to build. They don't wait for customers to call. They take responsibility for monitoring all their projects by visiting jobsites early and staying in touch with project superintendents on a regular basis. When they get the call to start they're ready, the materials are approved and available, the foreman is familiar with the project, and they are ready to man the job as required to maintain the schedule.
Be proactive rather than reactive. Go see the general contractor. Sit down and ask how you can make the job run perfectly for them. Visit the jobsite; walk the job with the superintendent one or two months before you're supposed to be there. Stay in touch with the project manager or field superintendent on a weekly basis to monitor progress. Ask, "How can we help you meet your project goals?"
5. Manage the jobsite
It would be really special if subcontractors and suppliers treated our jobsites like their own homes. In your home you don't leave trash all over the place. You don't leave a project unfinished. You don't borrow your neighbor's phone, power or toilet without asking. You don't damage other people's work and sneak away without telling someone you'll fix it. You don't create unsafe conditions and leave them exposed for your family members to encounter.
I expect subcontractors to be professional. Here's a jobsite management WOW checklist:
- Weekly safety meetings
- On-going everyday cleanup
- Haul your own trash away
- Provide temporary facilities
- Protect materials from theft
- Keep your tools locked up
- Do your own punch-list
- Keep your own set of plans
- Do your 'as-builts' as you go
- Protect finished surfaces
Check-in with the project superintendent every day before your crew starts work and discuss schedule, priorities, manpower, conflicts, and issues. Before you leave the jobsite, check-in with the superintendent to discuss what's left and what's next. Never leave a job when you think you're finished without a walk-thru to inspect your completed workmanship.
6. Help me
My working relationship with subcontractors and suppliers is a continuous ongoing push and pull versus give and take. I want subcontractors and suppliers who care about the overall project goals and will do whatever it takes to make it happen. I am not asking them to lose money or go beyond the call of duty - just do what they are contracted to do. This includes meeting the schedule, caring about their customer and the ramifications of not finishing projects on time.
7. More WOW ideas
- Send me a thank-you note
- Bring me leads
- Get bids in on time
- Give me value-engineering ideas
- Don't overcharge on change orders
- Send me product literature
- Keep me informed of new ideas
- Help me make a profit
- Give me a referral
- Train my superintendents
- Get an email account, carry a handheld email device and use email
- Carry a digital camera and use your digital camera
- Take me to dinner
- Ask me, "How can we improve?"
How subcontractors and suppliers can WOW general contractors is to be more proactive and less reactive. Help project managers anticipate problems, get the job done properly, provide enough qualified trained field help, finish ahead of schedule, and suggest better ways to save money. It doesn't take a lot to set your company apart from the pack. Try a few of these tips, and you will get more work, make more money and have more fun.
George Hedley is a professional business coach, popular speaker and best-selling author of "Get Your Business to Work!" and "The Business Success Blueprint For Contractors" available at his online bookstore. He works with business owners to build profitable growing companies. Email: [email protected] to request your free copy of "Winning Ways To Win More Work!" or sign up for his free monthly e-newsletter. To hire George to speak, be part of his ongoing BIZCOACH program or join one of his ongoing Roundtable Peer Groups, call 800-851-8553 or visit www.HardhatPresentations.com.