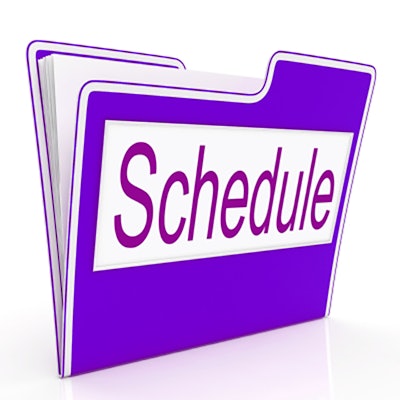
What are the odds of your projects staying in budget if your master schedule is constantly changing? Have you thought in depth about why projects don't come together as planned, or have you just accepted that life is like that in the construction industry as you don't control all of the variables — most prominently you don't have complete unimpeded control of scheduling.
Master schedules fall apart through chain reaction. One domino falls on one project and it knocks several other project schedules down. One project falls behind and the scrambling to add men and equipment to the project to pick up speed messes up the progress of other projects.
When a project gets delayed you find places for the crews to go, which often means you have more people on a project than is efficient. If you are one of the outdoor trades — such as an excavator — weather, permitting and shop drawing submittals mess up your schedule. If you are an interior trade, previous trades running behind mess up your schedules.
Complicating matters is the threat of liquidated damages as completion dates rarely slide.
From a deadline perspective, everything tends to work out kind of okay. Jobs are finished somewhat on time despite, or due to, constant GC and client pressure. What suffers is your bottom line. Having more or less people on a crew than is optimal and was planned for drives up your costs.
Each of the tasks your team performs has an optimal crew size and equipment mix. Keeping projects staffed with the optimal crew size can easily reduce field costs by 10%. That is why keeping a close eye on your schedule and thinking through contingency plans DAILY is so important. It keeps your crew sizes closer to the optimum.
Typically, a project schedule starts unraveling from the moment the GC is awarded the job. The client and the GC lose time tossing the master contract back and forth negotiating out the terms and conditions the design team wrote and which are completely ridiculous. Then the GC and the subs start tossing their contracts back and forth for the exact same reason.
The design team is slow getting new addendums out as the design that was sent out for bid wasn't complete. The design team lags behind in the codes review process. Contractors are slow in turning in the first round of submittals. The design team is slow in turning around the submittals and rejects several just because they aren't "comfortable" with the information provided.
By the time everything is approved and ready to go, the project is already two to four weeks behind the contract schedule, which was overly optimistic in the first place.
By the way, the preceding is why we strongly recommend adjusting your bid price in accordance with the design team's reputation for quality and completeness of their designs and their ability to keep the paperwork flowing on projects. Likewise for the general contractor: adjust pricing based on their ability to get jobs rolling and manage the project schedule.
There is not much you can do to overcome delays caused by those two groups.
What you can and should do is think through how your projects need to be staffed day by day. How are you going to move people around if the preceding trade is behind or weather holds up work? Make those decisions in advance.
Your foremen need to know whether an additional field worker is available should they need him at the last moment. When your project managers are responding to requests and committing to new deadlines, they need to remember the commitments that have been made to other projects. These are discussions that can and should take place in the front office each morning or late afternoon.
Always ask "What do we do if...?" Hound everyone until they habitually stay tuned in to the company schedule.
The last piece of advice I will share on this topic is this: schedule for reality. Analyze your historical job cost data and adherence to past schedules. Build detailed project schedules based on past performance. Your master company schedule will suffer far fewer changes — which improves your bottom line.