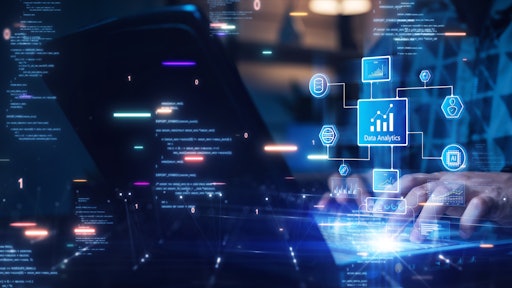
Only a grocer would envy the construction business’s 3%-to-5% profit margins.
On average, only about half of construction work planned for a given week gets done on schedule.
Those two data points are, obviously, related. Yet the systems that keep projects on track financially and those that help plan and manage day-to-day work at a jobsite have had precious little to do with each other.
That’s finally changing with new, cloud-based solutions that connect widely used, ERP-mainstay project financial management systems with emerging software that supports lean construction approaches.
Project financial management systems exist to preserve the (scant) profitability that was built into a project when it was bid. They’re really about managing risk in an industry that bids on high-value, long-term projects amid a thinly informed bidding process done under intense competitive pressure. These systems lessen that risk by providing visibility into a project’s contracts, WBS (work breakdown structure), and other facets while using historical benchmarks to forecast cash flows. When materials come in, work gets done, and invoices come in, the financial impacts get reflected.
Project financial management systems continue to evolve. Artificial intelligence and advanced analytics are coming into play to help spot anomalies before they turn into costly surprises. That can be particularly useful on projects with dozens of subcontractors and thousands of expense line items. But the core features of project financial management are well established and their value to construction projects undisputed.
Go Lean
Lean construction systems are another matter. Some in the industry may have never heard of lean construction, though considering that the Lean Construction Institute is celebrating its 25th anniversary and boasts more than 240 member companies with close to 2 million employees, that’s a shrinking group. Others may still consider it a fad. And then there are adherents. Count me among them.
The universe of adherents is expanding, and for good reason. Lean construction takes lean production techniques honed by Toyota and others and applies them to construction. It’s about optimizing a project in the big picture, minimizing the waste of time and materials, thinking hard about process, assigning responsibility, demanding accountability, communicating relentlessly, and continuously improving, among other tenets.
As opposed to running products through an assembly line, you’re running workers through a project. But there are commonalities. You want an even flow of work. You want people to count on the fact that the work that precedes them is done right and on time so you don’t disrupt the flow. You want someone close to a particular task – framing, drywalling, painting, whatever it may be – to commit to delivering quality output at the right moment.
Emerging lean construction solutions provide the tools and frameworks to instill these principles into projects. It’s about influencing and controlling projects proactively so they deliver on time or early. That’s in sharp contrast to critical-path management approaches that, by and large, seem to focus on retroactively understanding what went wrong and who’s at fault. Lean construction solutions enable that sort of root-cause analysis, too. But they’re fundamentally designed to avoid problems in the first place.
Better Together
That proactive nature makes lean construction solutions powerful allies of project financial management systems. The lean construction solution has its fingertips on real-time jobsite actuals and forecasts – in essence, your jobsite becomes a real-time data factory.
The lean construction solution knows exactly when a piece of work is completed. That information and a lot more goes directly to the project financial management system. In addition to sparing data re-entry and the typos that come with it, managers get instant visibility into what a given piece of work is worth in terms of costs and revenue. Your cost estimating and cash-flow forecasting get sharper.
Which brings us back to the top. Construction businesses are high-risk endeavors working expensive projects with thin margins. Delays are costly, and the sorts of interdependencies that breed delays are everywhere: without framing, you can’t drywall; without drywall, you can’t paint. If you can gain efficiencies on the jobsite in ways in which the benefits exceed the costs, you go for it. Lean construction solutions help do that. Paired with mainstay project financial management systems, they’re the way forward in construction management.