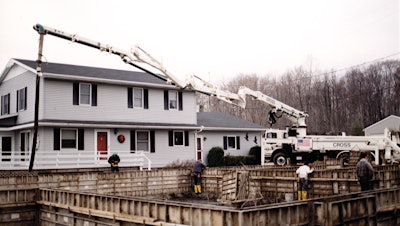
Concrete pumping improves productivity and safety on the job site by taking the most grueling manual labor out of a concrete pour. Reducing activities like wheeling and raking has prevented an uncountable number of injuries over the years, not to mention increased the quality of the concrete. But concrete pumping isn’t risk free. Electrocutions, hose whippings and tip overs are three of the more common safety issues that can be prevented when proper pump setup procedures are followed.
The Right Site
Concrete pump safety starts with a safe, uncluttered space for the pump truck on the job site. The ideal space should be level. It must be large enough for a pump with fully extended outriggers and away from excavations, while allowing room for the expected flow of ready mixed trucks. Per manufacturer requirements, a concrete pump must set up within three degrees of level.
If the pump setup site is near an excavation, follow the One-to-One rule: For every one foot of vertical drop, stay back from the base edge at least one foot. Take measurements from the edge of the outrigger pad nearest the excavation. Less-than-ideal soil conditions and engineered support walls are treated differently, so check with the pump operator for guidance. Some manufacturers may have more restrictive setback requirements depending on the size and weight of the unit. Always refer to the manufacturer’s operation manual.
A Quick Look at the Responsibilities for the Concrete ContractorLearn the ACPA's safety hand signals for concrete pump operators and workers onsite.American Concrete Pumping Association
Outriggers
Properly positioned under the outriggers, cribbing spreads the weight of the pump truck’s load. When in doubt, always use more cribbing.
Soil type on the job site will factor into outriggers. Different soil types have different load-bearing capacities. For instance, virgin ground typically supports approximately 14 psi while firm, compacted gravel supports 72 psi. A large boom can exert up to 120,000 LBF-FT on the soil. It is recommended to confirm soil conditions prior to setting up the pump.
American Concrete Pumping Association
Power Lines
A boom coming in contact with power lines is the Number One cause of fatal accidents when using a concrete pump. It is the position of the American Concrete Pumping Association (ACPA) that if power lines are within 20 feet of the area to be poured, a spotter must be employed whose only job is to observe the movement of the boom and warn the operator if the boom approaches the danger zone. The distance must be changed to 50 feet if the power lines have more than 350,000 volts. (20 feet is 6 m and 50 feet is 15.25 m in the metric system). It is a good idea to mark the danger zone with cones, lumber, spray paint, caution tape or other identifying markers. As stated in the ASME B30.27 Safety Standard for Material Placement Systems, it is the contractor’s responsibility to provide the spotter.
Whenever power lines are present, it is the contractor’s responsibility to inform the pump provider. It is imperative that a pre-pour meeting be held whenever power lines are present on a job site. Everyone on the job site should be trained in power line and electricity safety, where the danger zone is, and the purpose of the danger zone.
Provided by the American Concrete Pumping Association. This article was originally published in February 2013 and updated in February 2023.