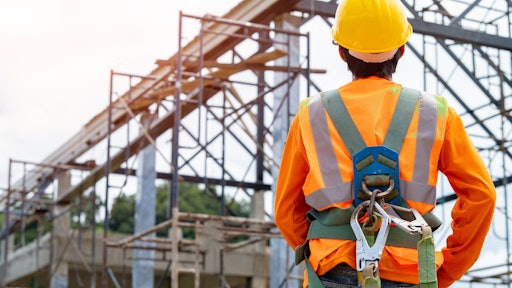
Helping protect your business from financial loss often comes down to how prepared you are. There are many safety hazards—especially in the construction industry.
A well-designed and implemented safety program, most importantly, helps protect your employees. But it can also help keep your injury costs and financial losses under control—workplace injuries not only affect your business’ ledger, but also your team’s productivity and ability to meet deadlines.
A strong safety record can help build and maintain your reputation as an employer who cares about their workers. And it may be a requirement of other companies you’re looking to partner with.
If you don’t already have a safety program in place—or haven’t updated it recently—consider creating one specific to your business and the hazards you and your employees face on and off the jobsite. There are many aspects to consider when creating or updating your program.
Here are four key elements to include.
1. Bolster Your Hiring Process
Despite the best-laid plans, accidents happen. But building a team of responsible, dependable employees helps reduce their frequency. Being intentional about who you hire is key to helping protect your business.
Here are a few steps you can take to help bolster your hiring process:
- Before you fill an open position, have a legal expert review your company’s recruitment and hiring processes to help ensure they’re in line with state and federal requirements.
- Conduct a background check and check motor vehicle records (MVRs) of potential new hires to help identify red flags, such as a poor driving record or a history of unsafe behaviors.
- Request references from potential new hires, then ask those references about the candidate’s overall professionalism and commitment to safe practices.
- Establish and then follow employment guidelines and job qualifications that detail what is required and expected.
These are just a few ways to help ensure you’re building a strong team. When you hire new employees, it’s important to remain engaged with regards to safety. Test new employees’ safety knowledge and skills and provide relevant training.
Once you’ve done so, continue to communicate clear safety expectations and provide easy access—on paper, via signage, and directly to employees via their mobile devices—to your safety procedural guidelines and any needed safety resources.
2. Address Specific Hazards
In the construction industry, there are many hazards that come with working on a jobsite. To help prevent injuries, it’s important to identify specific or unique dangers your employees may face.
Before starting a new job, it’s helpful to assess the area your employees will be working in to determine if there are any environmental hazards. Consider the property’s history, age, and location. If you identify any areas of concern, take proper precautions to help protect your workers. Perform periodic workplace and project site reviews as conditions evolve on the jobsite.
In addition to evaluating the jobsite itself, make sure your equipment is safe. Ensure your employees are properly trained to handle equipment, perform daily safety inspections before doing so, and have what they need to protect themselves from potential hazards, including sound exposure or ergonomic issues.
Your safety program needs to address any potential exposure to chemicals, fumes, asbestos, and other environmental factors.
You can also designate a supervisor or group of employees to oversee your safety program. Empower these experienced employees to help identify and address potential safety concerns and be points of contact for questions.
Remember, creating a strong safety culture begins at the top—with you. Make safety a priority and motivate your employees to do so as well.
3. Periodically Assess—And Update—Your Plan
It’s not enough to have a plan in place—you need to ensure your employees follow it and that it’s up-to-date. It’s vital to periodically reassess your plan and determine whether measures you have in place are working. That includes communicating clear procedures on how to report a worksite hazard and incident.
The first question OSHA will ask when they visit a jobsite is, “where’s your safety plan?” Is it easily accessible to your workers and do they have the resources they need to conduct their jobs safely?
Again, reputable contractors want to work with other contractors who have a strong safety record. Often before agreeing to partner on a project they’ll ask to see your incident log.
Here are some questions to ask when you periodically review your safety plan: Have you had incidents in the past that caused injury or safety concerns for your employees? What are they and what can you do to proactively prevent an injury? Are your employees following the measures you have in place? Do they have regular ongoing training on how to do their job safely?
Here’s a brief checklist to help you periodically update your plan:
- Readjust your safety program strategy based on past incidents and evolving risks
- Identify what needs to be done first to help lessen on-the-job incidents
- Provide the necessary resources, including personnel, to carry out your plan’s new objectives and procedures
- Communicate and implement the changes by developing appropriate training plans and providing easy access to your updated plan and needed resources
- Continue to measure your company’s progress to ensure the changes are being implemented and that they’re effective
Reassessing your plan on a regular basis can help you identify weak spots or areas for improvement. Staying vigilant about your plan’s effectiveness can help you avoid an incident down the road.
4. Review Your Insurance Policy
Your safety plan—and the culture of safety you cultivate with your team—is your first line of defense to help prevent incidents and protect your bottom line. Your insurer may have a safety team to help assess your job-site risks and perform periodic safety plan reviews. It’s also important to talk with your insurance provider to ensure you have the right coverages for you and your business.
Your employees are your business’s most valuable assets. Take the necessary precautions to protect them and your company’s reputation. Implementing a strong safety program is a win for everyone.
These four elements of building a better safety program aren’t meant to be a complete list. It’s important to consistently evaluate your business and determine what makes the most sense for your safety program. As always, reach out to your insurer or local experts to help develop a plan specific to your business.