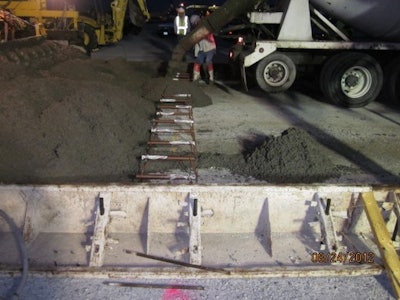
I have worked in the cast-in-place industry 17 years and managed an amazing variety of projects. As the
Concrete Placement Subcontractor, my role became quite a balancing act between customer service,
internal resource management, and personnel needs, constantly meeting the Owner’s schedule, budget,
and quality. These pieces are the overall cornerstones of a successful project. Often times my first look
at the project I was managing would come well after the scope had been negotiated by the estimating
team and the contract had been issued. At that point, as project manager, you have very little leeway in
determining how the project is executed, particularly on a project with prescriptive contract documents.
In the detailed planning process of how to execute work, I would often find myself writing RFI’s and
asking for meetings involving the design team and the General Contractor to make exceptions to
contract document directives that did not allow for specific circumstances of how the work had to be
executed based on site conditions, design conditions, space or time constraints, scope determinations,
and other factors, but would inevitably be met with skepticism from the customers who would naturally
assume I was requesting changes solely due to a potential cost savings on my end or to submit a change
order for extra funds. This was true and false in the sense that I consistently found that the biggest risk
in terms of cost on any project is the potential cost of remedial work, which is never included in the
original budget. That risk is one I tried to avoid simply due to actual cost impact to that particular
project, however; it is also costly to a company’s reputation and relationships with customers as well,
and those factors control the company’s ability to gain access to future work, and therefore, greatly
impact the company’s success overall.
I managed several airfield paving projects during my time as a project manager, and this type of project,
in my experience, required much more planning and discussion regarding exceptions to specifications
than any other. Most of the specifications I read required the use of a paving machine, and the
description of the type of machine and its requirements was extremely detailed including the
size/weight, number and spacing of vibrators and their amplitude and frequency, and so on. After pages
of reading the requirements of the paver, there would typically be a short section in the specifications
stating there may be areas/lanes where a paver may not be practical, and in those areas alternative
equipment could be used as permitted by the engineer and/or Contracting Officer. The issues I
consistently encountered with this type of specification were not only that there would be little to no
information regarding alternative, acceptable equipment for these areas, but more importantly that the
mix design specification had been written only to accommodate the use of a paving machine, which
involves a max 1”-2” slump with no chemical admixures.
There are many advantages to using a paving machine for airfield paving. I never used a slip-form paver
during my time as a project manager, primarily because my company did not own one, but the challenge
of getting the mix design just right to avoid issues with edge slump was one of the reasons why we
chose to form lanes with wood or steel forms, whichever the specifications would allow. Regardless of
the type of machine, the advantages of using this type of equipment are, due to its size and weight,
typically about 75,000 lbs and its system of gang-mounted vibrators, it is able to place and consolidate a
paving lane without requiring much in the way of hand-finishing following strike-off, and therefore
minimizes the chances of future spalling, which is very important to paving anywhere aircraft will be
traveling. Debris on an airfield can cause very costly damage to aircraft when sucked into an engine, and
a concrete spall will do just that. Not to mention, closing a runway for repairs is costly and time
consuming; the best way to give a dense, long-wearing surface is to minimize paste and hand-work at
the surface.
Regardless, there are many areas on any project where a paving machine is simply impractical. Lanes
that have structures (manholes, drop-inlets), lanes that abut existing buildings or even fence lines, lanes
with height restrictions, and even just very short lanes surrounding buildings can make placement with a
paving machine impractical if not impossible. I learned over the years the best way to get approval to
deviate from using a paving machine in these areas was to mark up a drawing identifying the specific
lanes/squares where hand-finishing would be required. At that point, I would provide the alternative,
proposed equipment, and typically would request the use of a pneumatic, vibratory air screed for strike
off. Although the air screed was able to vibrate the concrete, the consolidation could never quite match
that of the gang-mounted vibrators on a paving machine, so we would supplement with a crew carrying
backpack vibrators, especially when paving thicknesses were over 10”. Yet, as you would imagine,
vibrating concrete at a 1”-2” slump by hand is extremely challenging if not impossible. The size and
weight of an air screed cannot compare to that of a paving machine; its light weight and small size,
however, are precisely why I would want to use it in areas where access issues made using the paver
impractical or impossible. Yet I found it was unable to strike off concrete at a 1-2” slump at the proper
elevation. Low slump concrete mounds up when deposited on the ground, and it has to be placed
slightly higher than proposed elevation to avoid low spots at strike off, but even a heavy-duty air screed
is not heavy enough to consolidate low slump concrete and ends up riding up and over the tops of these
mounds rather than striking off at grade. So, the challenge for the Subcontractor at this stage becomes
requesting a slump deviation in order to use alternative equipment. This is something I have found to
be one of the most challenging deviations to approve post-award. However, I also cannot imagine
having much success deviating from the requirement in the pre-bid process, simply because when you
are competitively bidding a project, you do not want to disqualify based on your inability to perform to
Specification requirements. Deviations take months to approve sometimes, and no one wants this time
coming out of a project schedule. Therefore, I have found that as a Contractor, defining these areas as
early as possible in the project timeline is not just beneficial, but necessary in order to maintain project
schedule.
As I transition from the world of project management to independent consulting, I look forward to
teaming up with suppliers, Owners, and design teams in order to find effective solutions to issues such
as this. I know that slump is a reflection of workability, however the water-cement ratio of the mix tells
us the amount of paste. Mixes containing water reducing admixtures can limit the amount of paste and
still provide the required workability. If a collaborative effort were taken to design mixes with a 3"-4”
slump for paving areas where hand-finishing is required without increasing the specified water-cement
ratio, I believe everyone involved in these projects would reap the long-term benefits. When it comes to
placement, time is limited with any mix, but with a 1-2” slump mix design, the time is limited by the
performance of the mix itself, not the time limits defined in the specifications, which is why many
companies use on site batch plants to produce these mixes. Still, I have seen concrete at a 1"-2” slump
set up in a mixer before it was deposited on the ground more than once. Doing trial batches with
admixtures for areas where hand-finishing is required and getting a mix design that performs well in
terms of workability and also provides a durable, long-wearing surface outlined in the specifications
would be beneficial to projects in terms of both schedule and quality. There will always be areas on any
project where the use of the paver is impractical, whether those constraints are foreseeable in the bid
process or not, and post-award deviations take time and can be very difficult to approve. Schedule,
budget, and quality are all influenced by one another, and no one has time or money for deviations or
unnecessary repairs. Since time is limited, it is better to get the concrete poured right the first time in
accordance with the specific result aspects of the specifications while allowing the concrete to be placed
in a way that is practical.