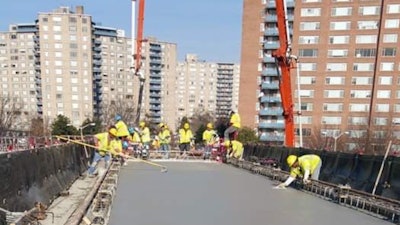
As a concrete slab place and finish contractor, lightweight concrete is one of the most difficult mixes to place. Any project requires a certain amount of planning up front with regards to the mix design being used. The mix must be designed in accordance with project specifications, but project specifics make mix design or schedule adjustments necessary to project success at times, not just beneficial to aid with placement.
Often contractors rely on the concrete company to create a mix for pumping because lightweight mixes must achieve the specified unit weight, and because it is typically specified for elevated decks, the mix typically must travel through a pump and system to its point of placement. For that reason, most lightweight mixes have air content higher than the 3% maximum required by ACI for hard troweled floors. Concrete suppliers have told me air is in the mix to aid with pumping, and the theory is that the air dissipates through pumping to yield an end product with less than 3% to allow a hard-troweled surface. A contractor working a mix with higher than 3% air will not successfully close the surface during the finishing process for a hard trowel finish, even if all the correct tools and workmanship is in place, which can lead to delamination. Checking air at the point of placement is therefore preferred, and checking at least the first three trucks to establish consistent air content is a good practice, even if the specifications require less frequent air testing.
Lightweight mixes also typically contain a certain amount of water reducing admixture. Any mix, lightweight or normal weight, will lose slump as it runs through a pump and system. The more system, the more slump loss. The more twists, turns, elbows (especially 90 degrees), the greater the chances are that the contractor will have problems with the mix, the pump, or possibly both. These are sometimes problems a contractor can overcome during a pour, but occasionally they lead to long term problems with the end product, which is why it is important that the access for the pump on a lightweight pour is an uninhibited as possible. My preference with any mix is to limit admixture usage. Even though higher slumps can be achieved with admixtures, the mixes are sticky and set time is affected in ways that may be unanticipated, particularly in periods of extreme weather. In addition, some admixtures can potentially have adverse effects on follow on work to the slab if a decorative finish is specified.
The defining characteristic above these concerns for lightweight is the aggregate, which is a very porous stone, such as vermiculite, perlite, or pumice. The porosity of the stone makes it capable of absorbing water like a sponge, and if the aggregate is not completely saturated with water prior to entering the pump and system, the aggregate will soak up any water in the mix, which will cause problems with workability once the mix is at the point of placement, if it even reaches that point; a dry, lightweight aggregate absorbing water in the mix within the line of a pump can and will cause a pump failure, which is very difficult for a contractor to overcome during a pour. The contractor’s due diligence is to make sure the concrete supplier is soaking the aggregate prior to the pour.
In winter when temperatures outside are below freezing, aggregate soaking becomes a challenge for the concrete supplier. As a project manager, I would visit concrete plants to see for myself what the aggregate soaking process entailed at least once; more than once if my crew was having consistent problems with a mix. What I found is that the typical aggregate soaking process involves a pile of stone located outdoors with sprinklers and soaker hoses doing the work of saturating the aggregate. In winter with below freezing temperatures, this does not work. Even if water is left running overnight, frozen stone is not a good plan for a workable mix. A lot of bigger concrete companies do, however, have indoor, heated spaces where they can park mixing trucks overnight. I would ask them to store the aggregate within the drum of the mixer with water overnight before a big pour, which they would gladly agree to doing.
I have found from experience that winter lightweight concreting in particular takes special consideration. All of the issues discussed above present challenges, but particularly with soaking aggregate in freezing temperatures, it is in the best interest of the contractor to visit the concrete plant and discuss with the quality control manager the method for soaking. Is the aggregate soaked indoors or outdoors? If the weather leading up to the pour is above freezing more than half a 24-hour time period for several days, perhaps outdoor soaking is acceptable. This method is preferred for larger pours simply because the space is not as limited. Making sure someone in the yard is regularly moving the aggregate so that the entire pile of stone, as opposed to just the top or bottom of the pile, is getting saturated is a necessary check. If the pour is occurring during a period of time with consistent temperatures for three days or more below freezing for more than half that time period, I recommend requesting aggregate soaking take in a climate-controlled facility. As mentioned above, the concrete contractor will usually accomplish this by placing the aggregate in the concrete trucks overnight and submerging it in water, storing the trucks in a warehouse that is heated. I like this method because submerging the porous aggregate in water should saturate it more efficiently than using sprinklers or soaker hoses on a large aggregate pile outdoors. However, the issue becomes the time period the concrete company is able to do this. Most companies are running other pours with their trucks the day prior, and so the aggregate soaking does not commence until all the pours from the previous day are finished. This is an important consideration when it comes to the timing of the lightweight pour as the
contractor wants the aggregate soaked as long as possible.
The other potential issue with regard to soaking aggregate indoors in concrete mixers is the size of the pour vs. how many trucks will fit in the indoor space. This is another area where the contractor must discuss with the concrete company how much aggregate and water can be stored in each truck and how many trucks will fit in the indoor space. At this point, the contractor should run a calculation on the size of the pour and compare that to the amount of aggregate that will be soaked. Usually the pour schedule and sequence have been discussed and set for weeks if not months ahead of the pour date, however, an adjustment to the pour size may be necessary if there is not enough saturated aggregate available for that pour. If the pour size is 200 cubic yards, but there is only enough space available to soak aggregate for 100 cubic yards, the contractor should adjust the pour size accordingly to avoid issues with placing and finishing as well as handing over a consistent, quality product.
As a contractor, I experienced challenges placing lightweight concrete from time to time in both summer and winter, but I found the winter months to require additional planning. Checking the temperatures several days prior to the pour is critical for winter concreting, and during that process, the contractor should be questioning how lightweight aggregate in particular is being soaked at the plant. Factors to consider include indoor vs. outdoor, the timing of the pour, and the size of the pour as a result of how the supplier is proposing to soak the aggregate. Asking these questions and taking a look for yourself are good practices. As contractors we are schedule-driven, and so adjusting times and pour sizes should be avoided if possible, but if they are necessary in order to deliver a consistent, quality finished product, it is in the best interest of all parties involved to do so.
Corey LeFebvre is a consultant at Polished Concrete Consultants. She previously served as a project manager at Century Concrete Inc.