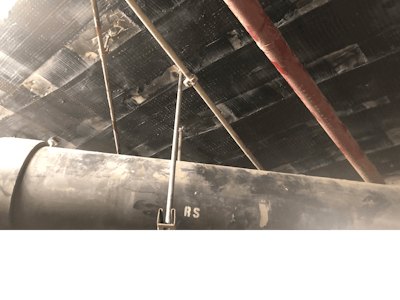
Concrete deterioration can be a major problem for facilities managers anywhere, but it’s especially challenging to address when a facility needs to remain in operation during repairs.
A Terracon client in the amusement park industry approached facilities services staff with a heavily deteriorated, elevated concrete slab project, and specific expectations for the repair program results.
Collecting Concrete Dust Samples
The slab was located within a swimming pool equipment building and had been exposed to moisture and pool sanitizing chemicals for an extended period of time. To get started, Terracon obtained four concrete dust samples from the slab.
Two samples were taken from the top of the slab and two from the bottom of the slab, both representing the concrete surrounding the reinforcement in their respective areas. The samples were analyzed in Terracon's materials laboratory and tested for chloride content according to the ASTM C1218 “Standard Test Method for Water-Soluble Chloride in Mortar and Concrete.” The test results indicated locations where the soluble chloride ion content in the concrete was well over the 0.15% maximum requirement for concrete exposure class C2.
In addition to chloride testing, two types of concrete compressive strength tests were performed; ASTM C42 “Standard Test Method for Obtaining and Testing Drilled Cores and Sawed Beams of Concrete” and ASTM C805 “Standard Test Method for Rebound Number of Hardened Concrete.” The concrete compressive strength test results were found to be acceptable and suitable for a slab rehabilitation.
Due to the handling of highly corrosive materials on top of the slab, a vehicular traffic grade waterproofing membrane was specified.Terracon
Creating a Plan for Slab Rehabilitation
The initial project requirements were to restore the slab while the pool equipment remained in operation and portions of the space remained in use, and the repair design should add 10 years of service life to the slab.
The design process included several iterations. Initially, the client received a budget for a repair program consisting of concrete repair, steel replacement, and waterproofing of the slab. When the client was presented with budget costs for the 10-year life extension repair program, they decided for an investment of that magnitude, the project requirements for added slab life had to be extended to 15 to 20 years.
Terracon’s design team went back to work and proposed adding a cathodic protection system to the repair design. This system includes a combination of an initial intense burst of current to passivate the rebar and long-term protection with the installation of internal impressed current, commonly known as galvanic anodes.
The state-of-the-art type of anodes used are a combination of impressed current applied by the anode’s self-generated electric charge which passivates the ongoing corrosion process and a passive galvanic cathodic protection to prevent future corrosion damage. In layman’s terms, it is a combination of a battery with a limited current life that stops ongoing corrosion, and a remaining cathodic sacrificial material, which will divert the corrosion from the reinforcing steel to itself until it is completely consumed, protecting the reinforcing steel from corroding.
The client had preconceived ideas for the repair program, the project outcome, as well as the cost of the implementation of a cathodic protection system. Terracon advised and educated the client regarding the most cost-efficient methods to achieve the desired outcome. When questions arose about proposed technology and repair method, Terracon’s design team presented the client with research, test results, and case studies to help them understand the repair technology and its benefits. This approach enabled the client to approve Terracon’s design solution and hire a qualified contractor to perform the repair work.
There was considerable concrete deterioration and spalling of the slab soffit.Terracon
Implementing a Cathodic Protection System
The first step when implementing a cathodic protection system is to determine whether the reinforcing rebar mat in the structure is continuous. Reinforcing steel mat continuity is necessary to ensure that the applied current will reach each piece of reinforcing steel in the structure to be protected and to make sure there is an uninterrupted path of migration of the ions towards the sacrificial anode.
Following establishment of the reinforcing steel mat continuity, the anodes are installed at a spacing established by an engineering design, performed by an expert, based on the density of steel in the concrete.
Finally, the deteriorated concrete and concrete removed for the installation of the anodes and their wiring was restored. In this specific case, due to the handling of highly corrosive materials on top of the slab, a vehicular traffic grade waterproofing membrane was specified. The product selected had the following characteristics: 1) It is applied seamlessly to avoid leaks through joints; 2) It has high chemical resistance including to chlorine, 3) It has very low odor and is volatile organic compound-compliant (VOC) for application during active use of the building; and 4) It is slip resistant while surface is wet, making it ideal for this application.
Because of the concrete permeability, the chemicals containing chlorides, with the help of the water seepage, migrated towards the soffit of the slab. There was considerable concrete deterioration and spalling of the slab soffit. During pre-design inspections it was also apparent the bottom rebar mat was extremely corroded and had significant section loss. Upon removal of the concrete, Terracon inspected the rebar to determine whether it had to be replaced or had minimal section loss and could remain in use with proper treatment.
This presented a great challenge since certain locations of the slab soffit were inaccessible, due to of the presence of many pipes and pipe hangers. During the course of the repair work, the contractor requested an alternate method to add supplemental rebar to the areas with heavily corroded steel.
Terracon’s Facilities division had the expertise to propose an alternate solution.Terracon
An Alternate Solution
Terracon’s Facilities division had the expertise to propose an alternate solution, whereby the lost area of steel due to corrosion was replaced with externally bonded carbon fiber polymers (CFRP), which could be applied within the space constraints.
The first step in CFRP design consists of determining the slab’s residual capacity given the reduced area of existing steel in the section. The residual capacity is then compared to the design loads to determine the level of deficiency. If the deficiency falls within the limits of CFRP, then the corresponding number of layers, width, and spacing is calculated and specified in the repair design.
CFRP is applied to a prepared, open pore, concrete surface and is achieved by means of mechanical tools for small applications or media blasting for larger areas. In this case, after the concrete repair was completed, a small hand-held grinder which fit within the limited space was used to prepare the concrete surface. A small brush or roller was used to apply the bonding epoxy to the concrete surface and the CFRP was threaded between the pipes.
The ease of installation in tight spaces made CFRP a viable solution for supplementing the remaining steel section, where required. Quality assurance testing was performed to verify the bond strength between the CFRP and the concrete surface. Additionally, witness panels were made using the specific batch of CFRP material used during the project to confirm the tensile strength and other properties used in the design assumptions .
The final design integrated a combination of repair technologies which met the client’s requirement to extend the life of the slab for another 15 to 20 years. This was achieved using Terracon’s design professional expertise in concert with quality of installation performance.
The selection of an experienced repair and restoration engineering consultant with knowledge of the latest technologies available in the market is critical to achieve a successful project, completed on time and on budget.
References:
ACI Committee 318, “Building Code Requirements for Structural Concrete (ACI 318-14) and Commentary (ACI 318R-14),” 2014, 519 pp.
https://www.vector-corrosion.com/galvashield-fusion-t2
https://www.master-builders-solutions.basf.us/en-us/products/deck-coatings/masterseal-traffic-2500
Carla Ramo VelázquezTerracon
Carla Ramo Velázquez, P.E., is a senior engineer in Terracon’s Facilities practice in Winter Park, Florida. Specializing in business development and project management of concrete restoration projects and constructions services, her experience includes management of contracts and construction activities for the private and public sectors.