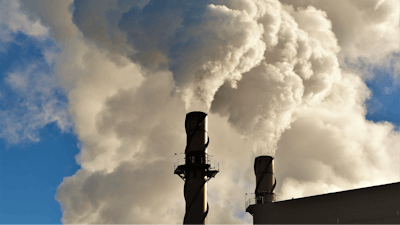
Recently, key players in the cement industry have announced plans and come public with a dedicated commitment to carbon neutrality. Of note, LafargeHolcim, the Portland Cement Association, as well as the International Cement Review - a website dedicated to the cement industry based in the United Kingdom.
LafargeHolcim's climate pledge includes:
- reduce direct CO2 emissions from the activities of an organization under its control to a target consistent with a net zero pathway,
- be carbon-neutral in indirect emissions from electricity purchased and used by an organization
- and reduce all other indirect emissions from activities of the organization from sources that they do not own or control - significantly, targeting a 50% reduction
The Portland Cement Association (PCA), also came forward with its plans to develop a roadmap by the end of next year (2021) "to facilitate its member companies achieving carbon neutrality across the concrete value chain by 2050." In the announcement, the PCA explains that "the roadmap will identify how to address the challenges that stand in the way of driving down emissions to achieve carbon neutrality, such as developing advanced technologies to reduce energy consumption, and developing and adopting regulations to allow for such technologies."
On September 21-24, the virtual conference "Decarbonising the cement industry – pathways to a sustainable future," organized by International Cement Review / CemNet.com. The following is a report of the happenings of that event. Published below with permission.
By ICR Research
Achievements and pledges
In the opening presentation, Mahendra Singhi, CEO of Dalmia Bharat Ltd (India), provided an inspirational start to the conference as he laid out the urgent need for decarbonisation and making the industry more sustainable. He emphasised the importance of choosing the right technology in this journey but was confident on the benefits for the industry: “Soon, there will only be an acceptance for zero carbon transition once the benefits of moving into a decarbonisation journey start unfolding for the companies who have proactively taken the steps.”
Following on, Dinah McLeod, chief executive of the Global Cement and Concrete Association (GCCA), highlighted the need to position concrete as the sustainable material of choice, supported by the organisation’s pledge to achieve carbon-neutral concrete by 2050. Furthermore, she stated that innovation is absolutely key to bring about an industry fit for the future, emphasising the important role to be played by Innovandi, the new cement and concrete research network, set up by the association.
Magali Anderson, chief sustainability officer of LafargeHolcim (Switzerland), presented the company’s global strategy for decarbonisation and confirmed its Net Zero Pledge, validated by the Science Based Targets initiative. New intermediate targets will see LafargeHolcim seek to lower its CO2 intensity to 475kg net CO2/t of cementitious material by 2030.
Ms. Anderson also highlighted the importance of the circular economy: “Really our pledge today is about climate and I’m talking a lot about CO2, but I think where we have fantastic opportunities is on the circular side [….] We really need to show the world we are more circular. Concrete is a 100 per cent circular product and I’m not sure many people know about that. At the end of the life of a building, once we demolish it we can reuse and put it straight in our cement or in our concrete.”
Sustainable technologies
During the conference, cement producers and equipment suppliers shared examples of the application of sustainable technologies in cement plants. Mauricio Giraldo of Argos Cement in Colombia explained how his company had significantly improved alternative fuel (AF) substitution in its Colombian plants. In addition, Stanislaw Sobczyk of LafargeHolcim in Poland showcased best-in-class AF utilisation at the company’s Kujawy plant, where substitution rates are close to 90 per cent.
Clinker reduction was also explored in detail with two presentations focussing on the technologies for calcined clay. Steven Miller, FLSmidth (Denmark), and Luiz Felipe de Pinho, Dynamis (Brazil), both showcased state-of-the-art technologies in this emerging area and case studies from recent projects.
Peter Hoddinott followed by looking at a new type of pozzolan-based cement invented by Vladimir Ronin of EMC. This ‘energetically modified cement’ is an ultra-low CO2 cement based on globally available minerals. Mr Hoddinott argued that “CO2 emissions reduction by clinker substitution will reach 35 per cent, but just when needed most, slag and fly ash availability are in decline.” EMC offers an attractive and new alternative.
From India, Atul Priyadarshi of Bharathi Cement, part of Vicat Group, shared an account of its renewable energy journey including WHR and solar power projects.
Pathways to improvement
Energy and process optimisation also remain part of the solution to lower CO2 emissions, with several presentations identifying proven technologies that can now be deployed in plants. Jens Breidenbach, KHD (Germany) revealed how upgrading existing ball mills with highly-efficient roller press-based grinding circuits can provide significant gains in CO2 reduction for cement companies.
Digitalisation of the industry is also providing further opportunities to improve the industry’s environmental performance through better data collection and decision-making. Javier García Sedano, CEO of Spain-based Optimitive, focussed on the application of artificial intelligence (AI) in the cement production process.
“We propose to apply artificial intelligence connected in real-time to the cement process, reading the data, learning from that data and applying optimal settings at all times in automatic-pilot mode in closed loop or open loop and in this way achieving optimum performance at all times,” Mr García Sedano said.
Dr Paul Flachskampf of INFORM (Germany) emphasised the importance of CO2 reduction efforts in logistics and transport, pointing out that the delivery of two truck loads of cement will generate emissions equal to the CO2 released in producing 1t of cement. Optimisation of logistics is therefore a crucial area of focus for all cement companies, and can be achieved most successfully by using AI and machine learning software to optimise truck fleets.
A look into the future
Speakers provided a number of insights into the industry’s commitment to improve its sustainability record going forward.
Jim O’Brien of Jim O’Brien CSR (Ireland) examined whether the cement industry was indeed walking the sustainability talk. He concluded that, while great progress had been made, advances had slowed in recent years and the pace now needs to pick up. There remains room for improvement, particularly in the area of safety despite recent advances.
Tony Hadley, THAA (EU), urged a shift in culture from complacency and compliance to leadership in industrial excellence. The industry needs to be fully carbon-reformed by 2040 – not 2050, he argued. Moreover, those companies that fail to show they are moving in the right direction will be penalised by investors and society.
Ultimately, the industry needs more research, pilot- and industrial-scale trials to push ahead in decarbonising its operations. Communication with all stakeholders and the creation of alliances with technology providers, research institutes and universities will be key in fostering innovation and achieving the successful implementation of these new technologies. This is particularly true in the area of carbon capture, storage and reuse, one of the most important pathways to meaningful large-scale carbon reduction.
Jan Theulen of HeidelbergCement (Germany) outlined the company’s carbon neutrality strategy and the part played by its cutting-edge carbon capture technology research and investments, including the LEILAC2 project.
Dr Laury Barnes-Davin of Vicat (France) informed the audience about the company’s two cutting-edge innovative projects: aggregate production by carbonation of kiln dust using Carbon8 technology and the carbonation of recycled concrete aggregates using cement flue gas within the framework of France’s National Project, Fastcarb.
Meanwhile, Mirko Weber and Joseph Kitzweger of LafargeHolcim shone a spotlight on Austria’s C2PAT initiative, which aims to capture CO2 from LafargeHolcim’s Mannersdorf cement plant in Austria and process it with renewable-based hydrogen to produce hydrocarbons for products such as plastics or kerosene.
Investment will be key in the implementation of the industry’s initiatives to reduce its carbon footprint – a fact not lost by Eric Trusiewicz, Breakthrough Energy Ventures (USA and Spain), who explained the interest of cleantech venture capital in investing in low-carbon technologies in the cement industry.
As Mr Singhi said at the start of the conference: “Now it’s time for cement companies and its professionals to dream big, aim big, plan big and create a roadmap for carbon-free cement. Ultimately we have to convert our sector from grey to green.”
The original article can be found at cemnet.com.