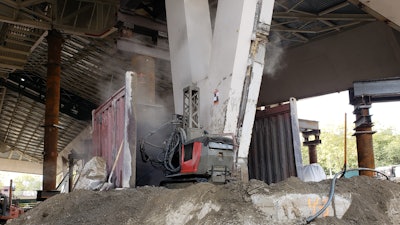
Imagine driving through downtown and being completely oblivious to a nearby multi-million-dollar building expansion – no redirected traffic, no interruptive demolition of surrounding buildings. This situation is almost unheard of in America’s largest cities as they continually evolve and change, especially with a project of such magnitude. However, that subtle, quiet transformation is exactly what is taking place in downtown Seattle, as developers take a different approach to construction: expanding downward.
One of Seattle’s most well-known buildings, the Climate Pledge Arena, is in the middle of a monumental renovation, one that will more than double the square footage of the building. The venue, formerly known as Key Arena, will be fully renovated and reopened by the end of 2021. The ambitious project officially began in the fall of 2019 and has since been the stage for some unique engineering and demolition methods. Contractor Redi Services played a key role in the renovation process by bringing this innovative equipment to the jobsite.
Installing a Superstructure
Expanding a building downward avoids the mess that comes with a traditional horizontal expansion – redesigning a city structure and demolishing surrounding buildings. But the unique approach didn’t actually stem from those concerns. Instead, the inspiration came from a desire and mandate to preserve the building’s roof.
Designed by architect Paul Thiry for the 1962 World’s Fair, the easily identifiable sloped roof received historic landmark status for its original use in a historic cultural event. The landmark designation requires that any modification to the building preserve elements of the historic structure.
Since the renovation process was under a microscope, every aspect of the process underwent additional planning and inspection. The downward expansion – which will take the size from 368,000 sq. ft. to roughly 800,000 sq. ft. – presented a variety of logistical challenges. Crews dug an additional 15 ft. below the current arena floor, about 60 ft. below street level. While accomplishing that feat, there was one small concern: how to hold up the 44-million-pound roof.
The engineers and contractors, including M.A. Mortenson Co. and subcontractor Rhine Demolition, developed an intricate plan. They would install a support system to hold up the multi-million-pound roof while they demolished the current columns and buttresses, and then rely on the supports for several months to allow for installation of the new support system. It seems daunting, but with a well-thought-out approach and step-by-step execution, they made it happen.
Project managers opted to install a temporary support system to hold up the arena’s iconic, multi-million-pound roof while they demolished the current columns and buttresses. They relied on these supports for several months to allow for installation of the new permanent support system.Aquajet
For a demolition project of this stature and configuration, a traditional approach of chipping hammers didn’t seem logical. Hand demolishing each pillar would have taken days, putting the destruction of all 28 columns, four chevrons and one buttress on a timeline of eight months.
Besides the lengthy time commitment of traditional demolition, there was another potential downfall to this approach. The demolition of the structure required extreme precision. Because the bases of the original structures were going to be used as a foundation for the new pillars, engineers required specific amounts of structural material, including rebar and concrete, to be left intact. Concrete breakers could have damaged the rebar and risked microfracturing the concrete columns.
The accuracy and highly regulated stipulations required on this renovation were not a good match for traditional demolition methods. There was a different option, though, that involved a process unfamiliar to many.
Hydrodemolition, and Careful Coordination, to the Rescue
Subcontractor Rhine Demolition used its connection with water blasting specialist Jetstream of Houston to find a precise, efficient and effective solution for the demolition. Jetstream recommended Redi Services, an industrial services support company based out of Lyman, WY.
Established in 2005, Redi Services has 500 employees and offices and shop locations in Colorado, Nevada, Utah, Idaho and Texas. Service offerings include controls and automation services, fire suppression, hydro excavation and fluid vacuum services, hydro blasting, facility turnaround support and coordination, waste management, trucking, pressure safety valve services and more. It also provides mechanical and civil construction services that augment ongoing maintenance service capabilities.
Redi Services proved up for the job, and introduced Aquajet Hydrodemolition robots to the Climate Pledge Arena worksite. For precision and efficiency, the contractor used two Aqua Cutter 710V robots that allow the operator to reach horizontal, vertical and overhead areas thanks to a 3D positioning power head.
“This was the first time we worked underneath a structure this heavy,” says Cody Austin, Redi Services area manager. “Because of our past projects with the Aquajet robots, we were confident it would be the right fit for this demolition.”
For precision and efficiency, the contractor used two Aquajet Aqua Cutter 710V robots to remove portions of 28 columns, four chevrons and one buttress in 30 days.Aquajet
“The timeline was strict,” Austin says. “It was a very fast-paced project where we needed to get in there, remove the concrete and let the others in line behind us get their part done to keep the renovation on schedule.”
Because everyone was working in the same area trying to accomplish their part of the project, it took diligent planning and careful choreography to keep everything moving and to avoid mishaps. Renowned contractor, M.A. Mortenson Co., was up for the challenge.
During the phase of the project that Redi Services was involved in, there were up to 175 contractors and subcontractors on site at a time. With a significant number of groups working, it was important that the logistics planning also considered the safety of everyone involved. Contractors marked exclusion zones with red tape and flags to keep people on the jobsite a safe distance from the high-pressure water jets and the debris from the concrete removal.
Demolition Details
Implementing water rather than sand or traditional jackhammers, Hydrodemolition robots provide a faster and more accurate method for concrete removal. The control system allows the operator to control the depth and accuracy of the cuts, which was important on a precise job like this. The unique design of the Aqua cutters and the absence of vibration allowed the contractor to thoroughly clean the rebar without causing microfracturing.
Besides the robots themselves, Redi Services used additional tower sections to accommodate the height of the columns. It also used two Hydroblast high-pressure water pumps, which provided 20,000-psi water pressure at 45 gpm. The pumps were positioned 50 ft. from the work, with a 100-ft. hose connecting them.
In total, Redi Services demolished structures that totaled 250 cu. yds. of material, all while keeping the rebar intact. The 1 1/2-in. rebar was installed in multiple rows, adding additional obstacles to the demolition.
“Because of the multiple layers of rebar, we had to cut from all four sides of each column,” Austin points out. “And that’s why the Aquajet robots were ideal for this. The robot cut up to 2 ft. thick per pass, which means that we were able to do 2 to 3 1/2 yds. per hour, depending on the rebar placement.”
Regular demolition methods produce debris that needs to be managed. With Hydrodemolition, the cleanup involves water treatment and less physical material cleanup. The blast water needs to be treated before it can be discharged or recirculated through the high-pressure pump. Redi Services opted to bring in two large vacuum trucks with a filtration system to contain and filter the water. Once filtered, the water was safely disposed of in a storm sewer at the top of the worksite.
An old shipping container that was repurposed and cut into shields for three sides of the demolition to contain blast water and increase safety on the bustling jobsite.Aquajet
“We developed the filter system ourselves, since we had done it on other jobsites before and we were familiar with the process,” Austin notes. “When both robots were working, we processed 40,000 gal. of water each shift. We had a third party monitor the environmental aspects of the wastewater, which included testing the pH levels for safe disposal.”
Redi Services encountered very few holdups and issues on the project. It employed a team of eight each day, including one operator for each robot, one to operate each pump, one for each vacuum truck and a supervisor and technician to support both robot “teams.”
The removal of each column was about a three-day process. Workers set up the equipment, spent 16 to 20 hours demolishing each structure, and then moved the equipment on to the next column.
“Rhine Demolition provided an old shipping container that was repurposed and cut into shields for three sides of the demolition,” Austin says. “The shields were removed with excavators with thumbs and moved to the next column. Each move took about an hour, including moving the shields, the robot, setting up the vacuum truck, plastic for spill prevention and moving the hoses.”
Redi Services completed the demolition in 30 days, working eight-hour shifts.
A Successful Sight
The stadium renovation brings plenty of curious onlookers. But the Hydrodemolition aspect of the project attracted attention from not just passersby, but other workers on the jobsite.
One reason for selecting hydrodemolition was the 1 1/2-in. rebar installed in multiple rows. This method allowed Redi Services to thoroughly clean the rebar without causing microfracturing of the concrete.Aquajet
Hydrodemolition was just one aspect in this large expansion project. The Climate Pledge Arena continues to be the site for creative, innovative and efficient methods and equipment. After the original support piers were demolished, crews reconnected the roof to permanent support pillars. They implemented steel and concrete frames to form the seating area of the interior and continually add details that hint at completion.
The arena is on track to be fully completed by fall 2021.
Celebrating Completion of the Steelwork
On January 29, 2021, after being painted and signed by construction workers and the Climate Pledge Arena and Seattle Kraken team members, the final steel beam was raised into place in a traditional Topping Out Ceremony.
Arielle Windham is a writer for the construction and demolition industry. Photos courtesy of Aquajet.