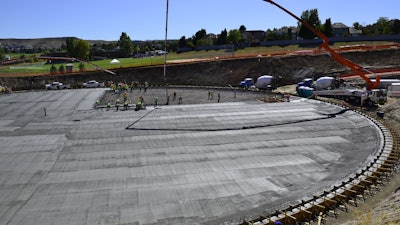
Internally cured concrete helps concrete realize its maximum potential in a simple, economical, and sustainable way. Due to increased hydration, it reduces early cracking, chloride ingress, curling, warping and improves the material’s durability. All of this lengthens the concrete’s service life. Further, because it can widen the acceptable parameters of field curing, internally cured concrete can mitigate risks of delay caused by unfavorable weather conditions. As such, it has become integral to many aspects of the building industry, including prefabricated and prestressed forms, structural concrete, concrete pavement, dams, water tanks, and more.
For concrete producers and contractors, being able to utilize this type of concrete can not only help improve customer satisfaction but also open new business possibilities in concrete pavement production. That said, starting internally cured concrete production can be an intimidating task. Here's a brief overview of internally cured concrete and a how-to guide to starting production.
Presoaked lightweight aggregate ready for batching.Courtesy of the Expanded, Shale, Clay and Slate Institute
What is Internally Cured Concrete?
The American Concrete Institute has defined internal curing as “a process by which the hydration of cement occurs because of the availability of additional internal water that is not part of the mixing water.”
In more general terms, internal curing happens when concrete is cured from the inside out. This process works in conjunction with conventional surface curing to produce more robust concrete by reducing the strain on different sections of the material as it cures.
The additional water required for internal curing comes from presoaked lightweight aggregate. Fine lightweight aggregates made from expanded shale, clay, or slate (ESCS) provide palpable value to the internal curing process. While conventional concrete sands have low absorption rates (1% in some cases) and quick desorption rates, ESCS provides both a high degree of water absorption and optimal desorption rates.
This is due to its internal network of capillary voids. Allowing the material to absorb a much higher percentage of moisture than its conventional counterparts. This absorbed water is returned to the paste matrix after the concrete sets, on demand for when the concrete needs water for curing. As such, ESCS can supply the cementitious mix with an adequate amount of moisture to ensure proper curing, making it an ideal aggregate for internally cured concrete production.
It should be noted that internal curing does require a couple more steps than conventional curing. However, these steps are easily incorporated into normal preparation and batching. The substantial enhancement to the quality of concrete as well as improvements to on-site curing far outweigh the additional steps the process requires.
In conjunction with Trinity LIghtweight and ESCSI, the below video gives some details on the use of internally cured concrete in a long-term water tank replacement project in Denver, Colorado. Engineer Erik Holck explains why internally cured concrete was the product of choice to build the massive multi-million-gallon tanks used to store Denver's treated water.
Testing water ratios before batching to ensure proper levels.Courtesy of the Expanded, Shale, Clay and Slate Institute
Understanding the Proper Ratio of Internal Water to Cementitious Materials
For almost all applications, evidence indicates that 7 lbs. of internal curing water per 100 lbs. of cementitious materials provide the appropriate amount of moisture needed for improved hydration. The amount of prewetted lightweight fines can be easily calculated based on the material's absorption and desorption characteristics. It is encouraged to contact your local ESCS supplier to obtain these values and assist in the calculations.
Soaking & Draining the Aggregate
When producing internally cured concrete, too little moisture will not provide enough hydration for internal curing, but too much will cause handling issues during batching. Proper soaking and draining protocol help maintain ideal saturation levels, so it is important to set up standards and monitor moisture levels throughout the soaking and batching process.
Constructing ESCS lightweight aggregate stockpiles at the concrete batching facility is the first step in maintaining uniform moisture throughout the pile. After this, concrete producers are advised to continuously and uniformly water the stockpiles with an approved sprinkler system for a minimum of 48 hours and until the absorbed moisture content of the aggregate, as determined by ASTM C 1761 and the ESCS producer’s recommendation, is achieved. Turning or mixing the aggregate pile will help to reduce moisture variation.
At the end of the wetting period, the stockpiles should drain for at least 12-15 hours immediately prior to use. Once the stockpiles have sufficiently drained to a typical free moisture range, the fine lightweight aggregate will handle and flow like sand. Even after the recommended drain time, there still may be a high degree of free water on the aggregate at the base of the pile. For this reason, it is recommended that the loader operator keep the bucket elevated approximately 6-9 in. to help drain any excess surface moisture.
The frequency of wetting the stockpiles will depend on the size of the piles and the weather conditions. Covering stockpiles with a non-permeable cover after watering will help reduce evaporation and help improve moisture consistency in the stockpile. Under steady operations, two stockpiles may need to be maintained: one pile of new aggregate to be prewetted and prepared and another ready for batching. It is necessary to periodically conduct moisture checks and possibly rewet stockpiles. Moisture checks should always be conducted prior to batching.
Draining lightweight aggregates before batching.Courtesy of the Expanded, Shale, Clay and Slate Institute
Batching the Materials & Placing Them Correctly
After soaking, draining, and proper moisture checks, ESCS aggregates will be ready to be batched. Producers and contractors can use mix designs based on end-use and replace a small portion of the fine aggregate or concrete sand with a predetermined amount of saturated ESCS material. Concrete professionals can find internal curing calculators online that can show them how to deviate from standard mixes to achieve the level of hydration needed. These calculators use preset mix designs and adjust to accommodate internal curing. (The ESCSI provides one at ESCSI.org/internal-curing/ic-calculator.)
However the mix design is ascertained, it is important that contractors and producers consult with the ESCS supplier to ensure they have the correct percentage of saturated lightweight fines.
Once batching ratios have been determined, the rest of the process of using internally cured concrete will proceed similarly to normal-weight concrete. The volume of lightweight fines used to produce internally cured concrete is not sufficient enough to classify the concrete as lightweight concrete.
If you Batch It, It Will Cure
Starting internally cured concrete production largely involves modifying batching protocols. However, concrete producers and contractors do not need to reinvent the wheel when it comes to the mix design. There are various calculator tools and manuals that can help these professionals modify a standard mix to include saturated fine lightweight aggregates. In addition, lightweight aggregate suppliers can be consulted for best practices for deviating from established mix designs.
By incorporating these batching protocols, concrete producers and contractors can not only provide their current customers with higher-quality concrete but also potentially qualify for new business opportunities since many Departments of Transportation require internal curing for concrete bridge decks.
About the author
Clint Chapman is the Western Region Marketing & Technical Manager for Arcosa Lightweight. Clint is an NRMCA Certified Concrete Technologist – Level 3, with over 20 years of experience in the concrete industry - the majority in the lightweight aggregates industry, focusing on structural lightweight concrete. Clint has been involved in a number of high-profile projects throughout the West, including the Wilshire Grand & the Gerald Desmond Bridge in Los Angeles, along with numerous internally cured water tanks throughout the Denver area.