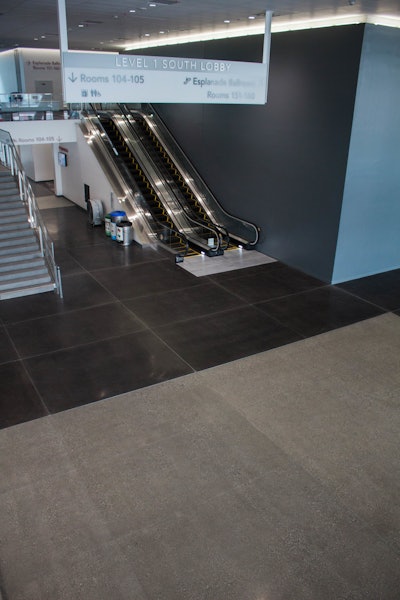
The world of polished concrete has grown exponentially over the past 15 years. Polished Concrete Specifications and manufacture’s complete systems have become much more reliable over the years. However, between the chemical producers, machine manufacturers, diamond manufacturers, architects, general contractors, concrete contractors, polishing contractors, and the various manufacturers’ representatives and distributors, there is plenty of room for incomplete, incorrect, and misunderstood specifications. Architects always intend to provide the very best for their clients. General Contractors want to build the very best for these same clients, and subcontractors want the concrete to be the very best it can be, in most circles anyway.
The architect originally worked with the client and a manufacturer’s rep of some type to create a specification that involved the use of color hardener with a diamond polished finish. Original intent was to gain color along with controlled sand tip exposure with a medium gloss diamond polished final finish. The project consists of over 45,000 sq. ft. of this polished concrete surface combination. The obvious issue here is that color hardener can be applied pretty uniform, but there will still likely be some high spots and low spots or areas of improper hydration and when the diamond polishing system is processed there will be areas where plain gray concrete “burn through” can occur.
Enter Bid Day
Bay Area Concretes Inc / PolishedCrete was the low bidder on this public project and became part of the Webcor general contracting team, along with world renowned architectural firm SOM. President of Bay Area Concretes, Mike Price says, “We bid projects with specification issues all the time, it’s what we do to communicate these issues after the fact, that really counts toward the success of the project and ultimately the team.”
Architects are inundated with manufacturers reps selling their products every day and the architects welcome the flow of new and exciting products and information into their business and creative mind set. Products and processes don’t always equal a successful final end-user surface and this is where the experience of a tried and true architectural concrete contractor can come into play. Bay Area Concretes, Inc has been a cast in place architectural concrete contractor since 1966 and a polished concrete contractor (PolishedCrete) since 1999. This is the perfect combination for understanding the dynamics of color hardener, integral color, plain gray concrete, surface seeding, dye and stain, imbeds, saw cuts, joint fillers, Aggretex surface treatments, stamped concrete finishes/textures and just about anything else you can imagine for finished concrete surfaces. Bay Area Concretes, Inc. works with architects every day and is always available for a no cost provided opinion on a design plan or detail. Once BAC was in contract they began the process of their communication of expectations quest required to arrive at a successful project for all involved parties.
“The most important component to successful architectural concrete contracting is expectations communication” says Price. It’s hard to argue with this concept, as there are so many paid experts on board with a high profile international project of this caliber. Price states, “Everyone is smart and very well educated and facilitating a non-confrontational communication space is key.” How else do you deal effectively with a billion dollar highly respected and very successful general contractor like Webco and a world class architect like SOM and of course, a well experienced client like City of San Francisco. It seems obvious that it takes an experienced team that listens to each other and works together.
Bay Area Concretes got the ball rolling by suggesting that the client execute a no-cost change order converting the color hardener product over to the Aggretex product. Aggretex is a patent protected wet-on-wet concrete placement product that utilizes placement of a pre colored Aggretex mix matrix at 3/8” thickness placed over plain gray sub slab – same day. The cost of Aggretex was definitely more expensive, says Price, but BAC was willing to foot that difference in cost as an insurance policy against “burn through” and other related issues to polishing color hardener. Aggretex has fine and medium sands within its natural matrix and can actually provide a very controlled colored concrete finish – similar to the original intent of color hardener, but with much more thickness of product. The owner had originally wanted uniform sand tip exposure and color hardener seemed like the right product, only because the architect and owner were not aware of Aggretex at the time the specification was designed. Experienced sub-contractors can bring great specialized information like this to the table. Thus, the idea of Aggretex was presented and a mock-up was constructed, all at the cost of Bay Area Concretes, so that original budgets were not impacted by the potential change.
Once the Aggretex sample was completed, the communication of expectations ensued with multiple site meetings. Once the client and the architects got their eyes on the Aggretex surface they realized, this actually created a sea of uniformity, in both a light cream and a medium gray color tone. Thus, the next questioning level was triggered “how will this surface hide inevitable stains?” As Price states, “It was better that this questioning process started then rather than at the end of a completed project.” Thus, the surface was treated with red wine and coffee, and allowed to have the stained areas dwell for three days to a week. This created staining that was still visible after cleaning the materials from the surface. Alarm bells sounded and the owner deemed it will be too hard to maintain. So, what will we do now?
The owner along with the design and construction team, as a unit, decided that maybe the owner was not after high end architectural uniformity in this particular public space, after all. The decision to place a plain gray concrete slab and to cut, grind, and polish this slab in yet another mock up iteration, and to improve the originally specified diamond polish system with a new Prosoco System was executed. Bay Area Concretes suggested Prosoco for their industry best stain resistance and potential add-on maintenance products to help improve against staining even more intently. Once the new mock up was completed on site, the same red wine and coffee was added to the surface and allowed to dwell. The team discovered several things, the Prosoco materials did a much better job of densifying and guarding the polished concrete surface against stains. It was also noted, that the remaining stain residues once cleaned, were now much harder to notice! Because the diamond polished plain gray concrete now showed irregular forms of surface reveal, large and small rock tips, cream pockets, and the like, this now normal polished concrete surface with little controls, provided a camouflage for future stains In the end, Bay Area Concretes offered a two tone coloration via the use of Prosoco dye in a “black” tone, too create architectural differentiation between plain gray polished concrete and black dye polished concrete.
Phase One is now complete and it seems that all parties are happy with the final polished concrete product. Bay Area Concretes suggested a team led by Kevin Sigourney of Prosoco, to arrive on site and meet with City of San Francisco maintenance staff and review cleaning techniques, equipment types, and various Prosoco chemicals. All in the name of completing the sales cycle for this project.
Webcor is a professional general contractor and SOM is a professional architect, and along with Bay Area Concretes helping to drive conversation throughout this process of expectation gauging and communication, everyone was able to maintain an open mind. This gave the design and construction team the ability to work together and find real world solutions for their mutual City of San Francisco owner, even if it meant abandoning the original specification. This article is an example of how any successful project does not simply stop on bid day. Successful polished concrete and all architectural concrete surfaces are a progression of communication by all parties and especially the communication of expectations. We are not perfect all knowing entities in this business and we need to learn how to lean on each other to succeed. Manufacturers, distributors, manufactures representatives, contractors, general contractors and the concrete and polished concrete sub-contractors as a team, will make a project successful. It takes a village folks.