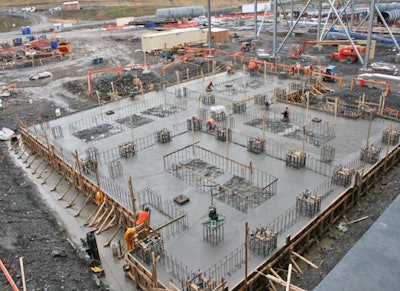
In the ongoing effort to improve jobsite safety, the effects of concrete properties on often unnoticed worker injuries have been largely ignored. The injuries can be grouped into one category: musculoskeletal disorder (MSD). This includes worker injuries to muscles, tendons, ligaments, nerves, joints, and spinal discs. MSDs don’t get as much attention because they don’t cause instantaneous injury as with many trip-and-fall incidents, but instead develop gradually with time. They can, however, result in back pain, carpal tunnel syndrome in wrists and hands, tennis elbow, rotator cuff disorders in shoulders, and bursitis in knees and shoulders.1 These injuries are the single largest cause of medical expense and lost work time among workers in the U.S. and Canada.2 A primary contributing factor to such injuries is shoveling, spreading, raking, and striking off stiff concrete by hand for concrete slabs on ground or for elevated slabs.
In the March 2017 issue of Concrete Contractor, we advocated having the slump requirements determined not by specifications but by an agreement between the concrete producer and contractor. That’s because slump is not a reliable indicator of strength, as it was once thought to be. We said further, that slump does affect the ease with which concrete can be transported, placed, and screeded. That’s one reason for letting the contractor decide the slump: Higher slumps result in greater productivity. But we can add another reason. Default specification values for slump, based on the old idea that stiffer mixtures result in higher quality concrete, actually result in a greater probability of MSDs.
MSD risk factors
The risk factors for MSD can include, forceful exertion, awkward positions, and repetitive motions, all of which are involved in shoveling, spreading, raking, and striking off concrete when slipform pavers, laser-guided vibrating screeds, bridge-deck pavers, or other such mechanical aids are not used.
When building most of today’s large industrial floors or pavements, commercial floors, and bridge decks mechanical aids are used, primarily to increase productivity and reduce costs. But there are still many concrete slabs placed with no mechanical aids because the use of such aids is prevented by accessibility, lack of maneuverability room on site, and obstacles created by reinforcing bars or electrical and plumbing protrusions through slabs.3 On these placements, specified slumps of 4 in. or less increase the likelihood that workers will develop MSDs. This has been shown by both anecdotal information from workers and by experimental evidence.
Ergonomics research shows the dangers
Ergonomics can be defined as fitting the job or task to the worker, with the goal of reducing the risk of MSDs.4 In Australia, the Concrete Industry Association Queensland (CIAQ) established an industry working party. Workplace Health and Safety Queensland (WHSQ) was also represented on this industry working party. The working party’s purpose was to instigate an industry change from a default slump value of 3- to 4–in. for commercial flatwork. This was driven by industry concerns regarding the musculoskeletal injury risks associated with lower slump values.
In July 2008 the Construction Industry Sector Standing Committee (ISSC) received a letter from the CIAQ seeking endorsement for pursuing this issue. The ISSC requested a WHSQ Principal Advisor on Ergonomics to assess the musculoskeletal injury risks associated with a 3-in-slump concrete in a commercial construction setting. The aim of the project was to gather information in relation to the commercial construction industry’s current use of a default concrete slump value of 3-in. during concreting activities and its impact on musculoskeletal injury risks. Anecdotal information provided by workers and management in the concreting industry, WHSQ construction inspectors and industry representatives indicated that slumps of 3 in. contribute to the force required when performing the concreting tasks.3 This anecdotal information has been verified by testing.
Ergonomic testing results
One article from a newsletter, Lifeline from the Laborers’ Health and Safety Fund of North America (LHSFNA),5 discussed the increased body stressing risks with lower slump values and provided a link to tip sheets6 specifically targeting concreting activities. The tip sheet on slump reported results of using an instrumented rake to measure the pull force needed to varying slumps. With a 1-in. slump, the mean force to pull material with the rake was 46 lb. In comparison, a 3-in. slump required an average of 27 lb, and a 6-in. slump required only 20 lb.7
Forces required to move concrete with a shovel have also been measured. In a study by the Canadian Infrastructure Health and Safety Association8 shoveling forces at various slump levels were evaluated by having workers shovel concrete with a load cell attached to the lower portion of the shovel handle. Ten shoveling tasks were performed on concretes with slumps of 3-, 4-, 5-, and 6-in., with the forces represented by the averaged peak forces measured by the load cell. The results indicated that with concrete slumps less than 5-in., lifting forces can exceed 44 lb. and increase the risk of MSDs such as chronic lower-back and shoulder pain.
Consequences of MSDs
The difficulty in recruiting and retaining workers in the concrete industry is at least partially attributable to a decrease in worker health and longevity as a result of MSDs. In addition, workers compensation claims related to the long-term effects of MSDs increase cost. This cost increase is passed on to the owner of the structure being built.
One step that specifiers can take to decrease costs is eliminating default specification requirements for slabs that often include a slump range of 3- to 5-in. or 4- to 6-in. Then let the contractor choose the slump based on the jobsite conditions that dictate the degree to which mechanical aids can be used. This is a win-win solution. Contractors’ workers are less likely to develop debilitating injuries, contractor productivity increases, and building costs decrease.
References
1. Concrete Finishers Health & Safety Manual, Infrastructure Health and Safety Association, Mississauga, Ontario, Canada, 2016, p.7-1.
2. “Washington Ergonomic Project Addresses Concrete Construction,” https://www.lhsfna.org/index.cfm/lifelines/fall-2003/washington-ergonomics-project-addresses-concrete-construction/ Fall 2003.
3. “Concrete Slump Project Report,” Department of Justice and Attorney-General, workplace Health and Safety Queensland, AU, July 2009, p. 11.
4. “Ergonomics in Construction,” Tool Box Tips, Washington University of St. Louis School of Medicine, 2014.
5. www.lhsfna.org/index.cfm?objectID=84B79A28-D56F-E6FA-964965E2316BE729
6. www.lhsfna.org/files/slump_tipsheet_final.pdf
7. “Choose the Best Slump for the Job,” Tip Sheet developed by Build It Smart, Laborers’ Health and Safety Fund of North America, Laborers’ International Union of North Americas, AGC of Washington, University of Washington, Western Washington Cement Masons Training Center, and the Stewart Prezant Ergonomics Group.
8. Vi, Peter, “Effects of Slump Level on Shoveling Weight of Concrete,” Infrastructure Health and Safety Association, April 2016, 4 pp.