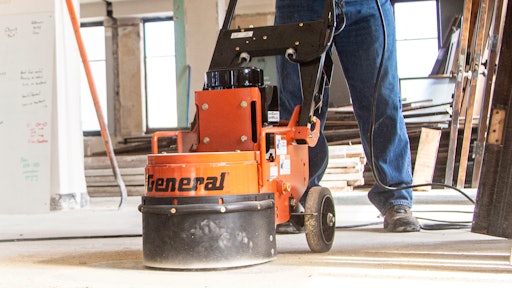
Surface grinders are versatile tools, able to tackle projects like surface preparation, coatings removal, and polishing concrete. But they do require different types of attachments depending on the job. Some attachments are specialized for a single specific use, while others can work for multiple concrete applications. Unfortunately, it is not always obvious to determine the best-performing attachment for a particular jobsite.
There’s no substitute for experience, but these basic guidelines can help with choosing the proper type of attachment.
1. Silicon Carbide Grinding Stones
Perhaps the most commonly used attachment, silicon carbide grinding stones are an easy-to-use, cost-effective solution for grinding concrete floors to prepare the surface for various coatings. They range from 6- to 120-grit to help contactors achieve the desired result.
Six- and ten-grit stones are the most popular because they provide maximum material removal rates. They’re perfect for removing trowel marks, high spots and rough sections on concrete surfaces. 24-grit stones have a lower removal rate but provide a finer finish when grinding concrete. They can also be used for rough grinding on terrazzo and other types of stone floors. 80- and 120-grit are great for polishing concrete. They can also be used for medium grinding on terrazzo and other stone floors when used with a water slurry/mixture. Service life varies for each stone. Six-grit stones may last between four and ten hours, while 120-grit stones may last up to 75 hours.
Although these attachments work very well for surface preparation, they should not be used to remove existing coatings from concrete. The pores clog with material quickly, rendering them ineffective in short order.
2. Tungsten Carbide Attachments
Tungsten carbide grinding attachments are used mostly on large concrete grinding projects where increased production and service life are needed, as these attachments are considerably more aggressive than a course 10-grit silicone carbide grinding stone. Tungsten carbide has a much longer service life as well. In fact, normal life expectancy for this accessory can approach several hundred hours.
More Information
Work smarter, not harder, with the right surface grinder. Here's what you need to know.
3. Scarifier Attachments
Scarifier attachments feature flails and spacer washers in a steel case. Different types of flails can be used to create a variety of results, so contractors need to consider the type and amount of material to be removed from the work surface, purchase cost versus service life, and the surface finish and texture.
The first type of flail available is the star flail, which is made of high-carbon hardened steel. Star flails are a solid, low-cost solution for light cleaning or scarifying, as they create a fine surface texture.
Beam flails are shaped differently for other applications. These are often recommended for medium-duty concrete and asphalt scarifying, descaling steel decks, removing thick material build-ups of grease, paint, oil, vegetable powders and some resins from floors, or removing carpet and tile adhesive that is dried and fully cured. Such style flails leave a fairly smooth finish when done.
Pentagonal flails are designed for more aggressive and rapid removal of a surface than a beam flail can achieve. They create a rather coarse surface texture, making them more suitable for heavy-duty concrete and asphalt scarifying, as well as heavy-duty descaling of steel decks.
General Equipment Company
4. Angled Tungsten Carbide Inserts
Designed for floor coating removal, these attachments use tungsten carbide inserts that are set at a precise angle to create effective scraping action. Productivity rates depend on the tensile strength and thickness of the material being removed. For example, this system can remove thick paint from factory floors at a rate of several hundred square feet per hour, whereas urethane coatings are much more difficult to remove and take more time. A good rule of thumb is that if the coating is thick enough to cut or pry away with a knife, then use tungsten carbide.
Many materials such as adhesives, rubber deposits and mastics have a tendency to extrude or smear, rather than shear off from the concrete surface, especially in high ambient temperatures. This problem can be eased by adding either water or a mixture of sand and water.
5. Diamond Systems
Attachments that utilize diamonds offer superior longevity and production rates for surface grinding and coatings removal applications. Contrary to tungsten carbide systems being most appropriate for removing thicker coatings, diamond systems are best for removing thinner coatings‾no greater than 1/16-inch in depth.
There are a few types of diamond systems available. The first system is a multi-segmented dry diamond disc, which is designed to operate dry but can also be used with water if an external water source is available. The discs fasten directly to the surface grinder’s gimbal head to provide very fast concrete removal rates.
The next option, diamond segment attachments, deliver up to five times greater productivity rates than silicon carbide stones, while having a service life up to 15 times longer. Because diamonds have an anti-clogging characteristic, they are an ideal choice for removing epoxies, paints and many thin film coatings, as well as large concrete removal projects. They are also an excellent choice for prepping and smoothing, readying the surface for a topcoat, or polishing.
The other common diamond system is a PCD (polycrystalline diamond) tooling, comprised of a diamond grit that is fused together with a catalytic metal. These attachments are recommended for removing thin-to-medium glues, mastics, covering materials and cement levelers from concrete surfaces. Sacrificial segments allow aggressive removal rates by the attachment’s PCD inserts while also acting as a stabilizer/depth guide to minimize the potential for surface damage.
It’s important to know how diamond systems are constructed to choose the best for a particular application. The diamonds are embedded in a matrix. During use, the matrix wears away to expose the diamonds. The bond hardness of this matrix varies from one diamond system to another. Ideally, choose a hard bond when grinding soft materials and a soft bond when grinding hard materials, as softer materials wear diamonds more quickly.
Regardless of the type of diamond system used, these attachments come at a premium price when compared with silicone carbide grinding stones, but also provide much higher productivity and service life. It comes down to how often a contractor will be using the grinder. If it’s a one-off job, then going with the cheaper, short lifespan grinding stones may be the smarter choice. But for a regular duty machine, diamonds can be much more cost effective in the long run.
To maximize productivity, be sure to replace or rotate attachments as necessary. If required, contact the equipment manufacturer to determine the life expectancy of each attachment. Always consult the operator’s manual for details on the specific surface grinder being used. For additional assistance, check with the manufacturer or your local distributor or rental center.
About the author
Dennis Von Ruden is President of General Equipment Company, a family-owned manufacturer of specialized light construction equipment based in Owatonna, MN. He holds an engineering degree from the University of Minnesota, a number of design patents and has developed several surface preparation product innovations, which are in wide use. With 50 years of construction equipment industry experience under his belt in multiple market segments, he humbly admits, “I’m still learning.”